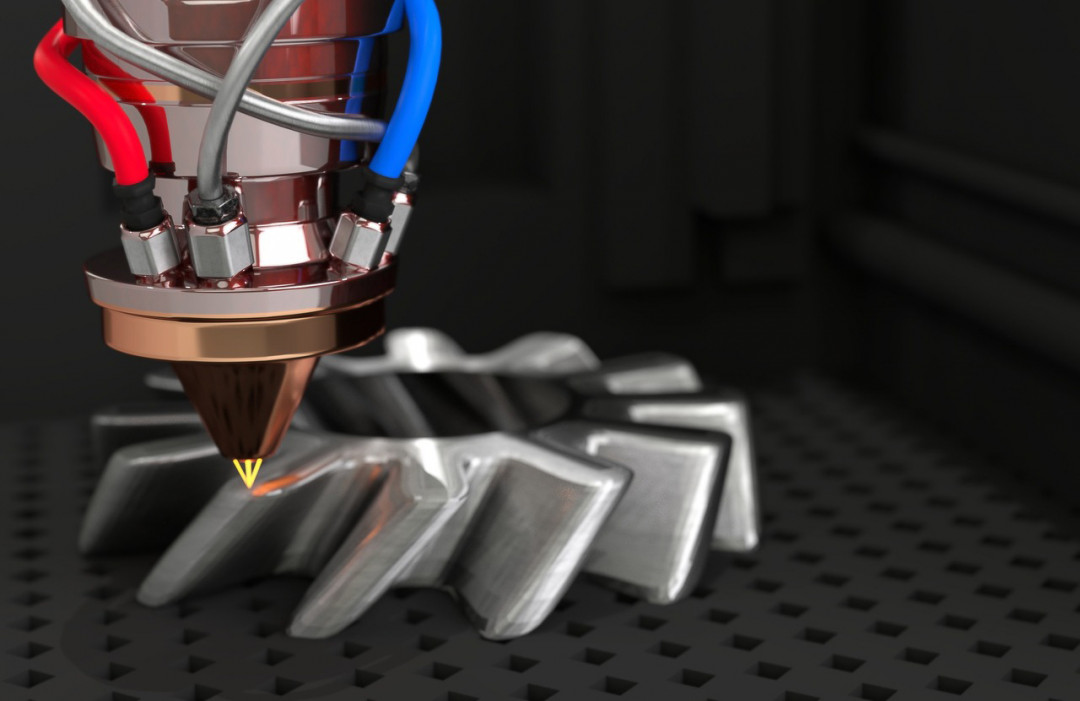
Additive Manufacturing as a Driver of the Future
Additive Manufacturing (AM) is transforming the manufacturing landscape, including in the welding industry. In conversation with Marvin Keinert, Dr. Simon Jahn and Markus Langer – members of the program committee for the event #AdditiveManufacturing: Metal in Top Form – the versatility and progress of this technology are highlighted. The experts discuss how Additive Manufacturing complements traditional approaches, creates new applications and addresses challenges on the path to industrialization. The event, organized by DVS (German Welding Society) in December 2024 in Essen, offers a platform to discuss current developments, standards and the future of Additive Manufacturing.
Additive Manufacturing is an increasingly relevant topic in the welding industry. What is your view on its role?
Keinert: Additive Manufacturing offers numerous exciting opportunities for the welding industry. Techniques that have long been successfully applied in welding, such as joining and coating, provide an excellent foundation for additive applications. We see strong growth in Additive Manufacturing in areas such as personnel qualification, research and standardization, especially within DVS committees. The future potential is immense.
Langer: I completely agree. In my experience, Additive Manufacturing combines a variety of technologies I’ve encountered in conventional manufacturing. What I find particularly exciting is the high demand for interdisciplinary collaboration across manufacturing engineering, production and process engineering. This interplay makes Additive Manufacturing a fascinating and rapidly evolving field.
How does Additive Manufacturing offer specific advantages to metalworking over traditional welding techniques?
Keinert: Additive Manufacturing allows for the creation of entirely new components rather than simply joining or coating parts. This significantly expands the scope for design innovation.
Jahn: Absolutely. With over 20 years of experience in research on layer-based manufacturing, I can confirm that Additive Manufacturing offers substantial added value. However, continuous expansion of knowledge is essential. Events like Metal in Top Form, organized by DVS, are crucial for knowledge exchange and advancing Additive Manufacturing.
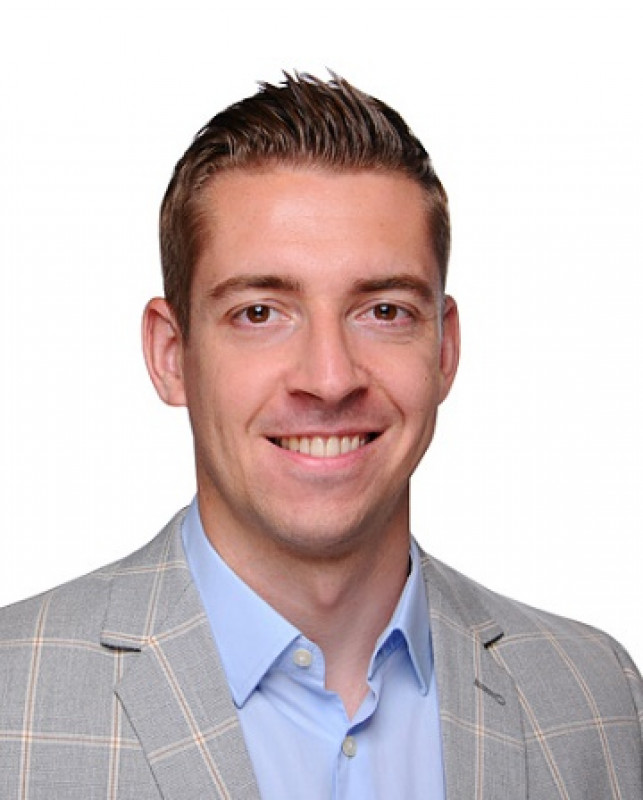
What aspects of the December event are particularly relevant for welding technology?
Jahn: The event will focus on the process category "Directed Energy Deposition" (DED), previously known as "Shaped Welding." We’ll not only address this method but also explore less-known approaches such as sheet lamination and multi-material processes, offering a comprehensive overview of the latest developments and applications in Additive Manufacturing.
Keinert: Another key topic will be quality assurance for DED processes, such as arc welding or laser / electron beam welding. Sessions will also cover innovations like Liquid Metal Printing for processing aluminum alloys. It’s an excellent opportunity to learn about the latest advancements and applications.
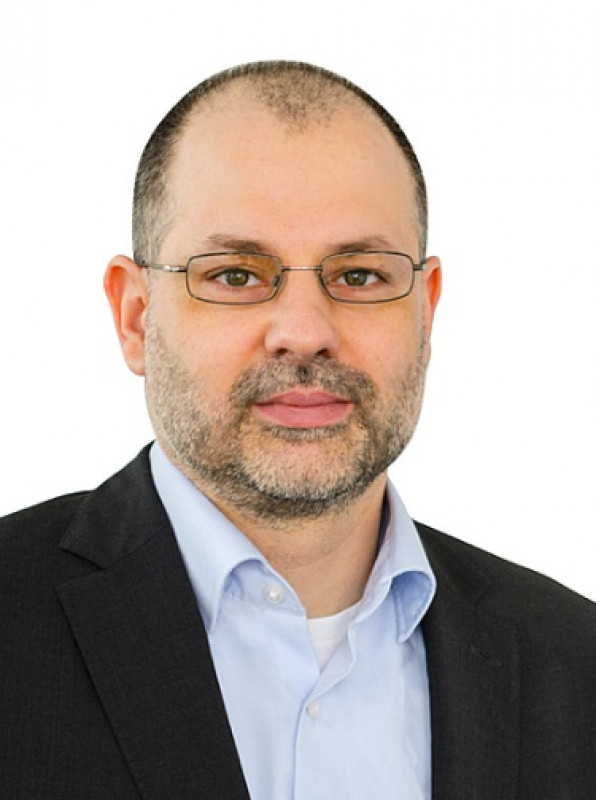
What new requirements must welding engineers and technicians meet when working with Additive Manufacturing techniques?
Keinert: Since February 2024, DIN EN ISO/ASTM 52935 has defined principles for qualifying supervisory personnel in Additive Manufacturing. At the event, DVS will present a qualification concept available through its training facilities. These certifications are becoming standard, especially for overseeing Additive Manufacturing processes.
What challenges do you see in industrializing Additive Manufacturing in combination with welding technology?
Keinert: A recently completed research project on combining Additive Manufacturing and welding provided valuable insights into processes like laser beam, plasma and friction welding. These findings are being incorporated into a DVS technical bulletin and the event will showcase the key results.
Langer: In addition to scientific presentations, we expect lively discussions on industrializing Additive Manufacturing technologies. Faster access to research funding, reduced bureaucracy and quicker transfer of scientific findings to industry are crucial, particularly given the dynamic development of Additive Manufacturing. The event is an ideal setting to foster synergies between science and industry.
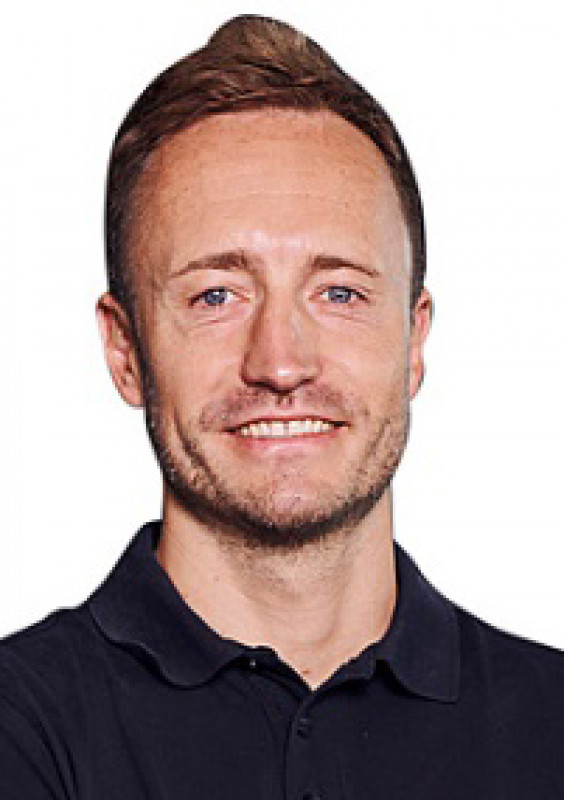
Where do you see the greatest potential for future developments in Additive Manufacturing and welding technology?
Keinert: For Powder Bed Fusion (PBF) processes, quality assurance systems are already well developed and industrially applied. Now, the focus is on advancing DVS guidelines for Directed Energy Deposition (DED) processes to drive further standardization.
Jahn: I also see significant potential in layer-based manufacturing, enabling parts with added value, such as near-contour cooling. These features are unattainable with conventional manufacturing methods. Specific applications and their implementation are particularly exciting to me.
Do you believe Additive Manufacturing will become a standard process in the welding industry?
Keinert: It already is in industries like aerospace and pressure equipment manufacturing, where small series are being produced using Additive Manufacturing. This trend is likely to expand to other application areas.
Thank you very much for the conversation.
Schlagworte
Additive ManufacturingAMDEDDirected Energy DepositionManufacturing