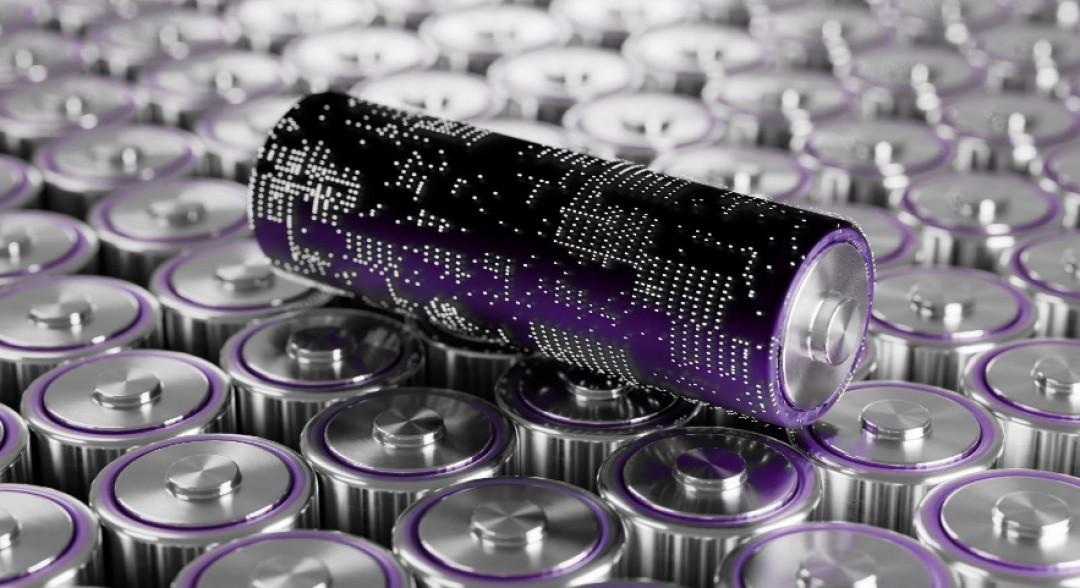
New Research Shows Benefits of Digitalization in Battery Cell Manufacturing
Digitalization makes the production of batteries for electric vehicles cheaper and cleaner. This is a key finding of a new research report Fraunhofer FFB and Accenture were presenting at Hannover Messe 2024. Leveraging digital solutions, a battery cell factory with an annual capacity of 40 gigawatt hours can save up to 27 million euros and reduce its emissions by nearly 10 % per year.
One example is scrap rate—the proportion of materials and batteries that cannot be used or sold due to quality defects. High scrap rates are a known issue in battery cell manufacturing. Digital predictive quality and traceability solutions can reduce these rates by up to 10.3% compared to conventional production methods. With material accounting for more than two-thirds of total battery cell production costs, digital solutions are especially effective when lowering costs and waste.
Driving efficiency with digital technologies
Another example is energy consumption, which accounts for about 5 % of total battery production costs. With digital tracking and optimization solutions, manufacturers can lower it by up to 9.5 %. These solutions can also help avoid up to 9.7 % of emissions from the production process. A third example is machine downtime, which digital predictive maintenance applications can lower by up to 7.1%.
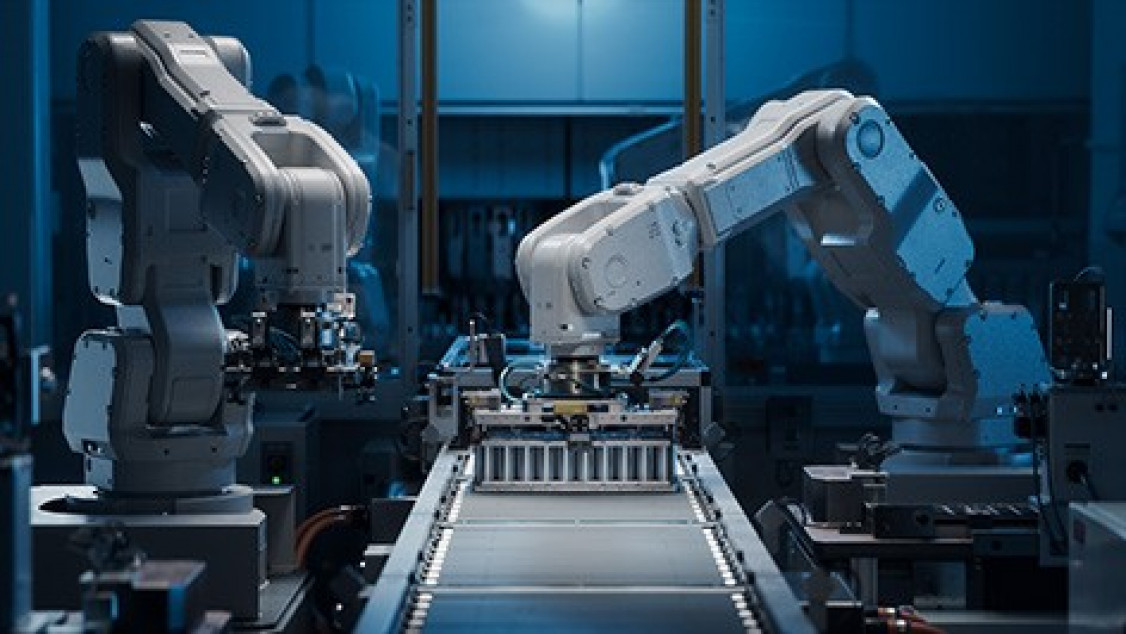
“The comprehensive Digitalization of the value chain is a key enabler for a more sustainable battery production,”says Dr. Jonathan Krauß, interim head of digitization in battery cell manufacturing at Fraunhofer FFB. “Digital investments show clear economic benefits, especially through the reduction of production costs. The challenge for battery manufacturers is to identify the right technologies and invest in them in a timely manner.”
Digital solutions will notably benefit electrode production. Most of the materials are used in this first step of battery cell production. “Efficiency and quality are key in battery production, especially in Europe, where we are establishing a new industry under high cost and time pressure,” says Dr. Philipp Wunderlich, senior manager and battery technology lead at Accenture. “By leveraging advanced digital technologies, we have an opportunity to secure a competitive advantage. But manufacturers have yet to catch up on digitization, even in more basic applications such as data collection and real-time analytics, which are a prerequisite for benefiting from transformative technologies such as generative AI.”
(Source: Fraunhofer FBB Press Release)