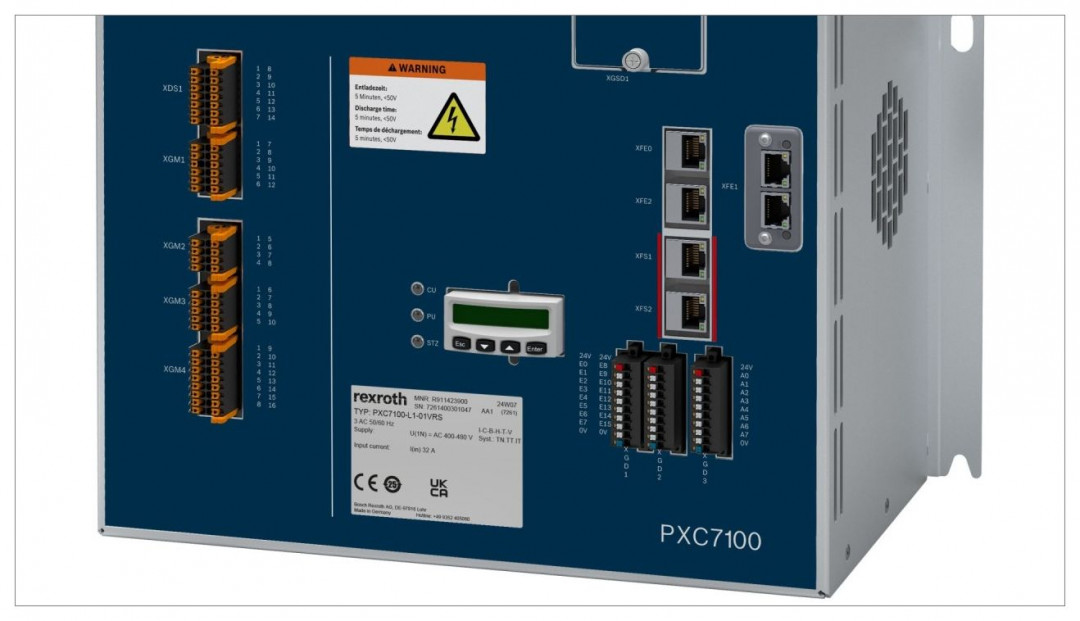
Cost-Effectiveness and Productivity in Precision Welding
With the new PXC7100, Bosch Rexroth is expanding its portfolio of welding controls with a particularly cost-effective solution for precision welding of small parts for the metal and electrical industries. The adaptive precision welding control offers tools for intuitive, assistant-guided commissioning, is equipped with modern process controllers and opens up possibilities for AI-supported process optimization. This provides several levers for increasing the productivity of the welding process.
Bosch Rexroth, market leader in the field of welding control systems for automotive body construction, is expanding its control system portfolio with a particularly cost-effective precision welding control system for applications with very low currents. This is the first time the company has offered a solution specifically for the precision welding of mainly small and electrical parts for the metal and electrical industries. The new development can be used, for example, for contacting sensors, compacting micro-strands or welding batteries. One focus of the system development was ease of use. The web-based user interface PRI-web enables simple, intuitive operation of the PXC7100 – also via mobile devices such as tablets. Another advantage is the setup wizard, which enables the system to be commissioned quickly. Welding generates a great amount of process data that can be used for process optimization, predictive maintenance or quality assurance.
The IoT Connector from Bosch Rexroth enables users to transfer data for further processing according to specific requirements. For example, AI-supported analyses can evaluate processes used for quality assurance. The IoT Connector supports the MQTT and OPC UA protocols. The MGD module (Measuring-Gun-Data-Module) available in the function bundle mainly functions as an analogue/digital converter and digitalizes all analogue sensors and process data directly on the welding head (e. g. force signal, position signal, current signal, transformer data). The pre-processed data is transferred via the WIC bus (Weld-Interface-Controller) in real time (1 kHz cycle rate) directly to the welding control for further processing. Scaling data, counters and mechanical data are also stored in the MGDM. Another advantage is the reduction in wiring work, as only one bus cable needs to be installed between the module and the welding control.
(Source: Bosch Rexroth AG Press Release)