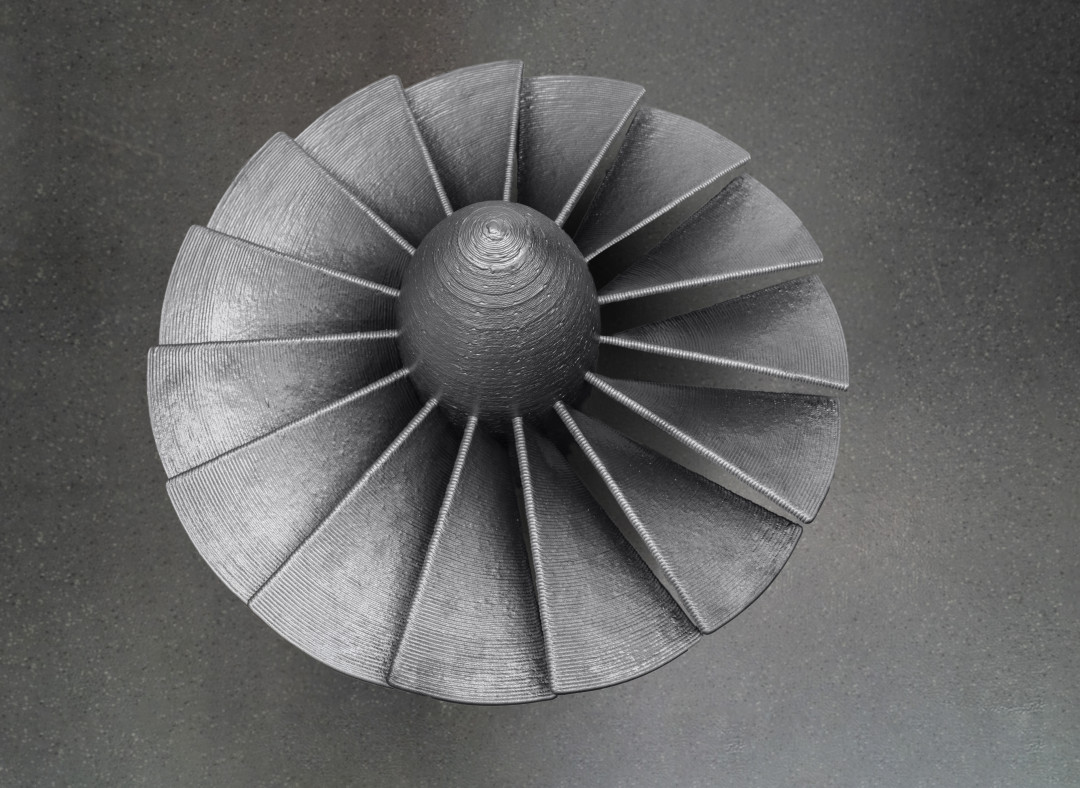
Metal 3D printing perfected in one welding characteristic
Using additive manufacturing, components, spare parts and even prototypes can be manufactured in flexible, resource-efficient and profitable way. The required components can be produced quickly and from scratch, regardless of the location. With CMT Additive Pro, Fronius presents a 3D-optimized welding process with features such as an particularly even layer structure, as well as high quality and stability.
Metal 3D printing is on the rise in many industries including automotive, oil and gas, aerospace engineering, ship and train building and the manufacture of construction equipment and tools. Compared to conventional production processes, such as casting, machining, or milling, the requirements in terms of molds and materials are low. This process saves a lot of time and material and provides flexibility when designing and adapting different components.
More cost-efficient and flexible
Additive manufacturing has much potential, especially where the degree of individualisation is high. Today, unique metal components can be printed in highly complicated geometries that have previously been difficult or even impossible to achieve. One example of this is rapid prototyping, which allows manufacturers to quickly adapt and refine their product designs before moving to mass production. Topology optimisations that could not be achieved using conventional methods are now possible. Metal 3D printing also simplifies repairs and on-demand printing of spare parts. It allows components to be manufactured "just in time", eliminating the need for storage and the costs associated with it.
The USP: exclusive 3D features combined in one welding characteristic
CMT (Cold Metal Transfer) is already the preferred method for 3D printing around the world. Fronius has now optimized CMT specifically for metal 3D printing and put all its know-how into the development of CMT Additive Pro. The integrated arc-on rate stabilizer ensures a consistent wire speed, resulting in an even and predictable build-up of layers. This improves the overall stability of the manufacturing process. “Another innovation is the adjustable heat input, which ensures consistency in the height and width ratio of the bead, regardless of the current temperature of the base material or the previously welded layer. Weld layers usually become wider and flatter as the component heats up,” explains Roithinger. “The power correction feature counteracts this, so that identical welds can be stacked on top of each other, layer after layer.”
The start of the weld within the construction process is another important criterion for metal 3D printing. Welding errors or cambers in the area where the weld was started can affect the quality of the result. Fronius has a solution with the Pulsed Hot Start function, which simultaneously achieves sufficient penetration and a constant layer height by starting welding within the pulsed arc. Here, the whole process is controlled automatically, so no extra settings are necessary.
360° service from the feasibility study to the pilot series
Schlagworte
Additive ManufacturingAMWelding