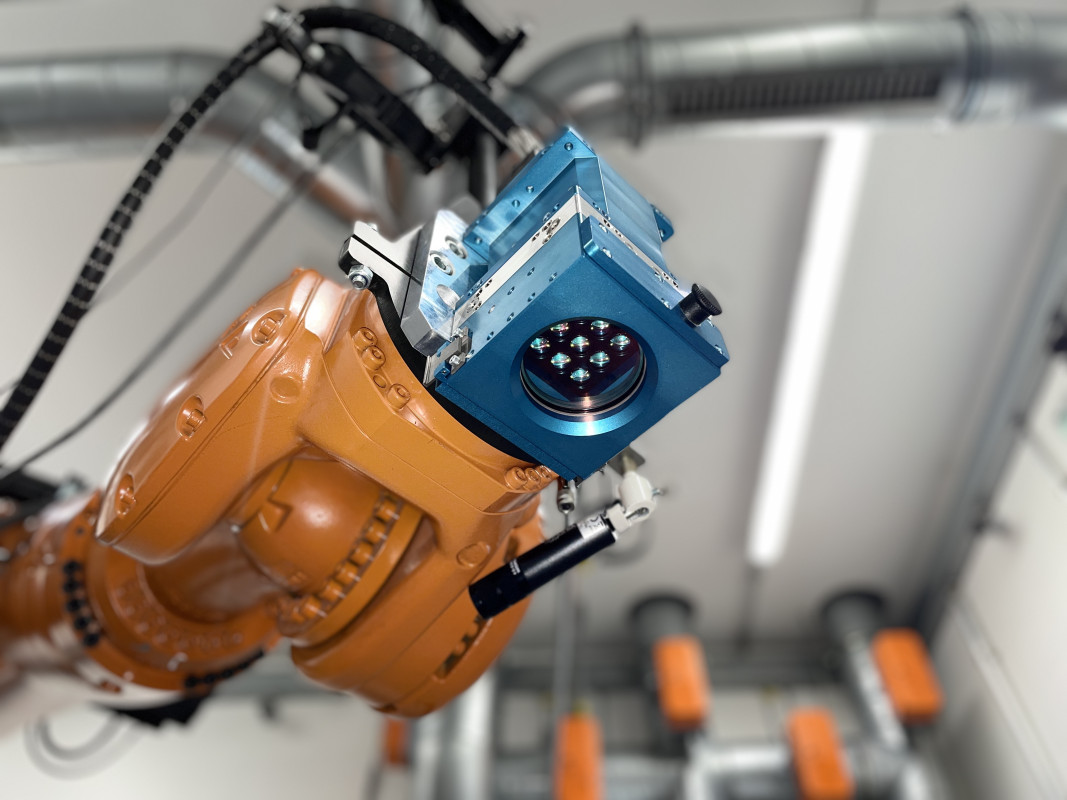
Two New Optical Concepts Improve the Weld Seam in Hairpin Manufacturing and Joining Plastics to Metal
The laser beam tool has become an integral part of modern production. At the same time, the requirements in terms of efficiency and possible applications are growing – and by the same token the demand of the laser. With new fields of application, component geometries and materials, conventional optics with limited movement and limited beam shaping options often are no longer sufficient to guarantee a flawless welding result. These include, for example, joining of thermoplastics and metal as structural components in vehicle construction and the welding of hairpins in electric motors. This is why LMB Automation GmbH has developed two new approaches in collaboration with partners that can be used to positively influence the melt pool with more flexible control and more precise power distribution. With the twin-weld process, better mixing in the melt pool is achieved, so that gaps can be bridged more quickly. MULTISPOT allows the intensity distribution within a laser focus to be varied locally and temporally resulting in precise adaptation of the performance to the weld geometry and material properties.
"The laser is an established tool in manufacturing," says Peter Schlüter, Managing Director of LMB Automation GmbH. "Despite its versatile possibilities and characteristics, its use has a few stumbling blocks that can be overcome through adaptations and continuous development." Not all laser beams are the same: the shape of the beam influences product quality by determining power density, cutting width, melt pool dynamics and heat influence. Depending on the application, the beam can be focused, expanded or divided. Particular attention should be paid to the melt pool, which affects the geometry, strength and microstructure of the joint and thus the quality of the weld seam. The better this dynamic can be controlled with optimized optics regardless of location and time, the sooner typical problems such as cracks, pores, splashes, undercuts or insufficient penetration in the keyhole can be avoided.
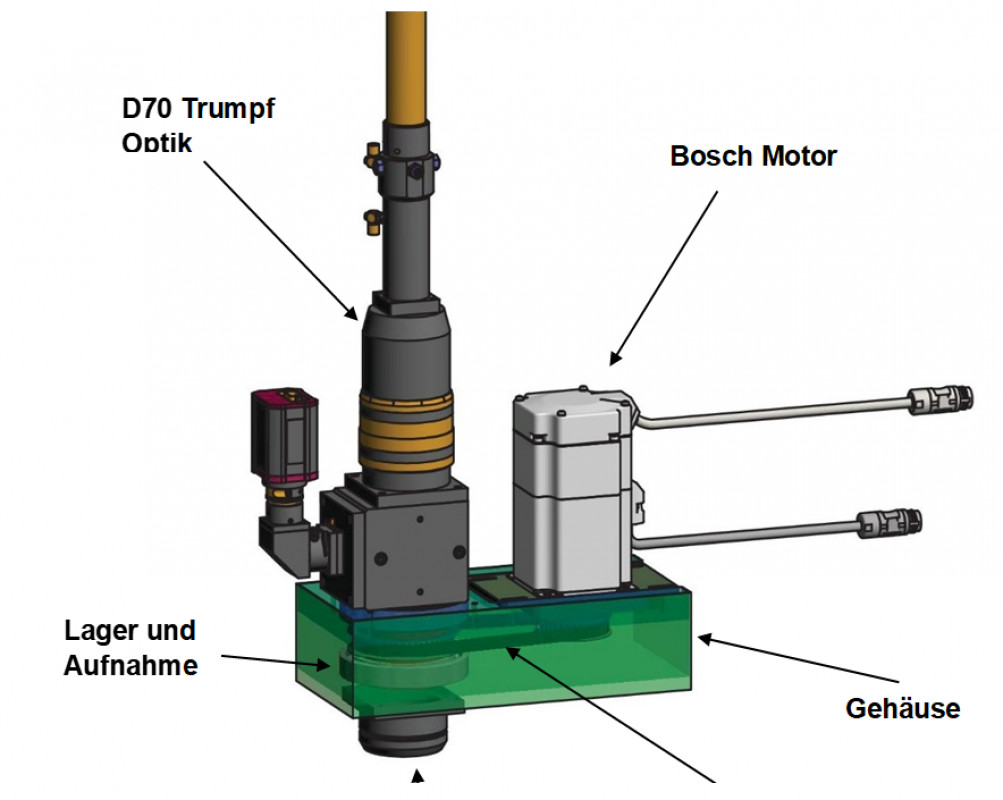
Structure of optics with rotating components
A typical case in which the combination of the demanding material and insufficient flexibility of the optics can lead to problems is the welding of copper joints, which are laid in the case of the hairpins, for example, in stator production. The viscous molten copper leads to pronounced process dynamics, which causes the material to spray very quickly. For production, however, a process with as little splash as possible is necessary for the production, as no ejected material must get into the stator. To ensure this, LMB uses an adapted bifocal optic in the twin-weld process, which additionally splits the beam in forward motion compared to conventional, fixed scanner optics and allows it to rotate in small circles around the optical axis. "In the melting area, the two partial beams use two keyholes to ensure that the molten material is better mixed and pressed into the gap by the rotational movement," explains Schlüter. As a result, the weld seam gains strength. At the same time, the pitch and rotation ensure that the time span when crossing a reference point is halved compared to just one focus point, thus accelerating the entire welding process.
With the combination of high rotation speed and flexible optics, the Twin Weld process makes it possible for the first time to process all contours with this optics. This would not even be possible with fixed bifocal optics. In addition, the higher rotation speed significantly reduces the number of pores that occur at the top of the weld. "Since Cu - components in particular are very prone to spatter, we wanted to prevent this. We achieve this by quickly melting and pressing in the heated material so that it cannot escape from the keyhole," says Schlüter.
Laser optics for joining plastics with a wide seam
Thermoplastics represent a new challenge for laser welding. They are more and more used as structural components in the implementation of lightweight construction concepts. Although laser welding of plastics is not new, it is mainly used to create relatively narrow weld seams, for example in the field of microfluidic applications. For structural components, on the other hand, large connection areas between the individual components are necessary to ensure sufficient power transmission. In order to achieve higher strengths and tightness when welding different plastics as well as plastics with metals, wider weld seams are necessary than can be achieved with standard optics. "In principle, homogenized laser focuses can be used to produce wide weld seams”, remarks Schlüter. “However, studies have shown that the maximum process temperatures when joining with a large laser focus at small diameter lead to partial overheating of the material indoors." The main reason for this is the severely limited or non-existent possibility of being able to vary the intensity distribution within the required large laser beam spot in terms of location and time during the joining process.
This is where the new MULTISPOT welding head comes in, which LMB developed in collaboration with six partners as part of an "SME innovative" project. The optics use a matrix of 3 × 3 laser diodes, which can be controlled individually, allowing the intensity distribution in the laser focus to be determined very flexibly. For this purpose, each of the individual optics is supplied by its own laser diode. The outer area in focus can be exposed to a higher beam power and the inner area to a reduced beam power. This allows the welding process to be adapted much more precisely to the welding geometry and material properties.
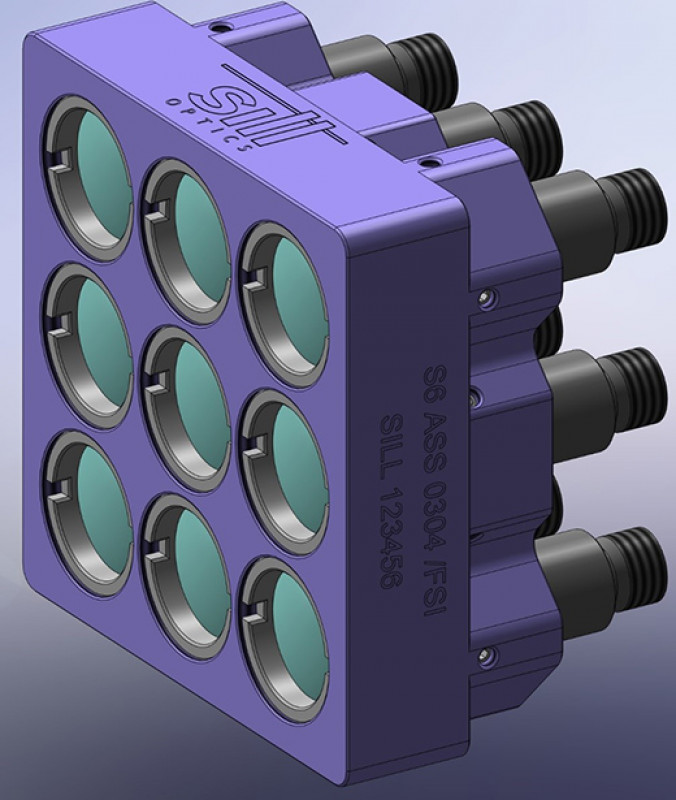
Interaction of plastic and metal in lightweight construction
This optics has shown particular promise in the welding of plastic with metal, which is being used more and more frequently in vehicle construction for doors or in interiors, for example. "In the tests, the load-bearing element was a sheet metal frame, to which a plastic cladding was to be attached for protection and, above all, to reduce weight," reports Schlüter. At the same time, the weld must achieve high strength and be tight so that no moisture reaches the frame. To prepare for the process, the joining surfaces of the metal part were first roughened with a different laser system. Subsequently, both components were pressed together and the metal was heated with the new MULTISPOT welding head. Due to an input of 100 W per diode, a total of 900 W could be used to melt the pressed plastic at the contact surface to form the hot metal. Thanks to the adjustable intensity distribution, the melt flowed evenly into the textured areas without heat loss, resulting in a particularly homogeneous and stable seam.
Both optics are currently being used for more in-depth application tests in prototype setups to find out how the intensity distribution and the melting result behave with different geometries and materials. The goal is to gain important insights into how the structure and operating costs can be made more efficient in the future.
(Source: LMB Automation GmbH Press Release)
Schlagworte
Joining PlasticsLaser Beam WeldingLightweight ConstructionWeld Seam