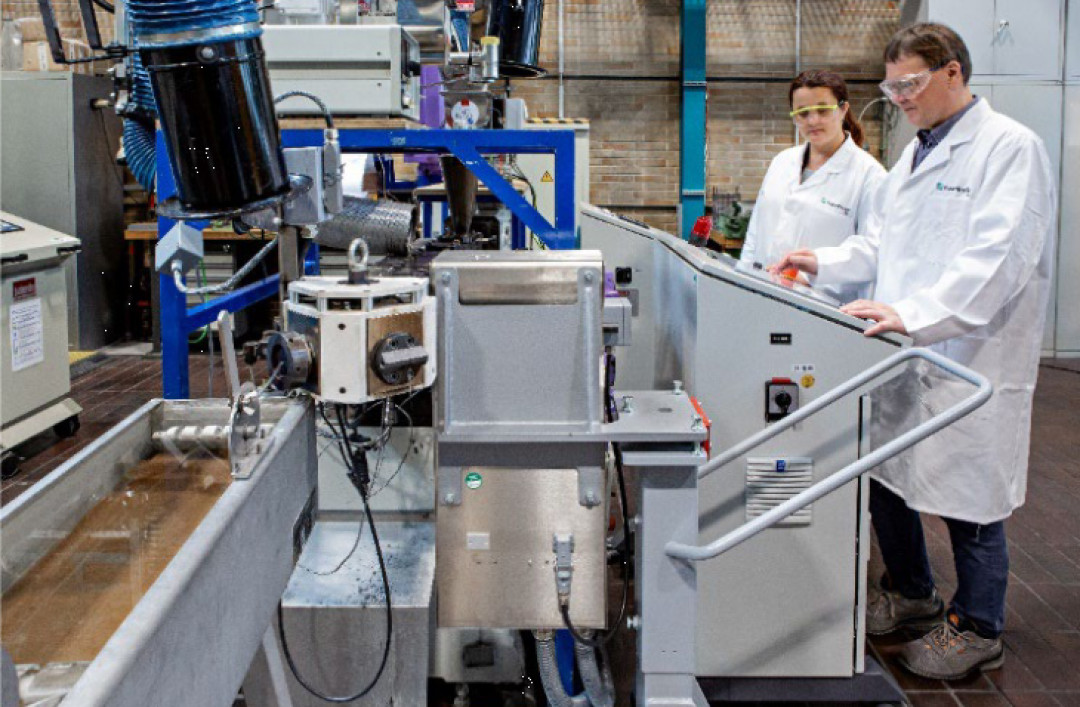
Polypropylene Recyclates: Best Quality at Minimum Cost
All organic substances, including plastics such as polypropylene (PP), undergo auto-oxidation in the presence of oxygen. This happens millions of times faster at the high temperatures of compounding and injection moulding. The result for PP is a degradation of the polymer chains, i.e. a reduction in molecular weight, which means that products made from these plastics can no longer be recycled. Antioxidants added during the manufacturing process slow down the degradation. Without these additives, many everyday objects could not be produced in a usable form. Researchers at the Fraunhofer Institute for Structural Durability and System Reliability LBF have further enhanced rheological online testing to identify specific additives more rapidly and optimize costs.
Until now, when developing new compounds, the optimum proportion of antioxidants has been determined in extensive and therefore cost-intensive test series. Ultimately, the processor wants to optimise the properties of the plastic. However, lengthy pre-tests are not profitable when producing recyclate from old material batches with highly variable quality and varying residual stabiliser content. The approach of simply adding "enough" stabiliser is unsuitable or too costly for a consistent circular economy. There is also an upper limit for the compatibility of stabilisers with the polymer. This is because the plastic should not only have a second but also a third, fourth etc. life. During each life cycle, the stabilisers are used up as intended, with their by-products remaining in the plastic. This makes it even more important to add only the absolutely necessary amount of stabiliser during recyclate production. Online rheological tests accelerate the process of achieving exact stabilisation and optimising costs.
Online characterization for stabilization tailored to recyclates
In order to obtain immediate information about the effectiveness of the stabiliser addition, the Fraunhofer researchers are taking the approach of characterising the melt online during compounding. Meaningful information on the processing behaviour of plastics can be obtained using an online rheometer. It measures the flow curves of both shear and elongational viscosity. In initial tests at the Fraunhofer LBF, a marginally stabilised virgin PP served as a model polymer. A clear correlation was established between the viscosity values and the stabiliser concentration or the viscosity values and the molecular weight. Considering recyclates, one post-industrial and one post-consumer PP were analysed.
The post-industrial PP from start-up material and sprues from injection moulding still has a high stabiliser content. This means that no significant improvements in preserving the molecular weight can be achieved here with stabiliser additions of more than 0.1 % – the flow curves for the stabiliser additions investigated are therefore almost on top of each other. In the post-consumer PP, the antioxidants are consumed to a high degree, which is associated with significant damage during processing, which is noticeable in a low viscosity/flow curve. For optimised stabilisation and minimised damage to the recyclate, an addition of 0.5 % additive is required here.
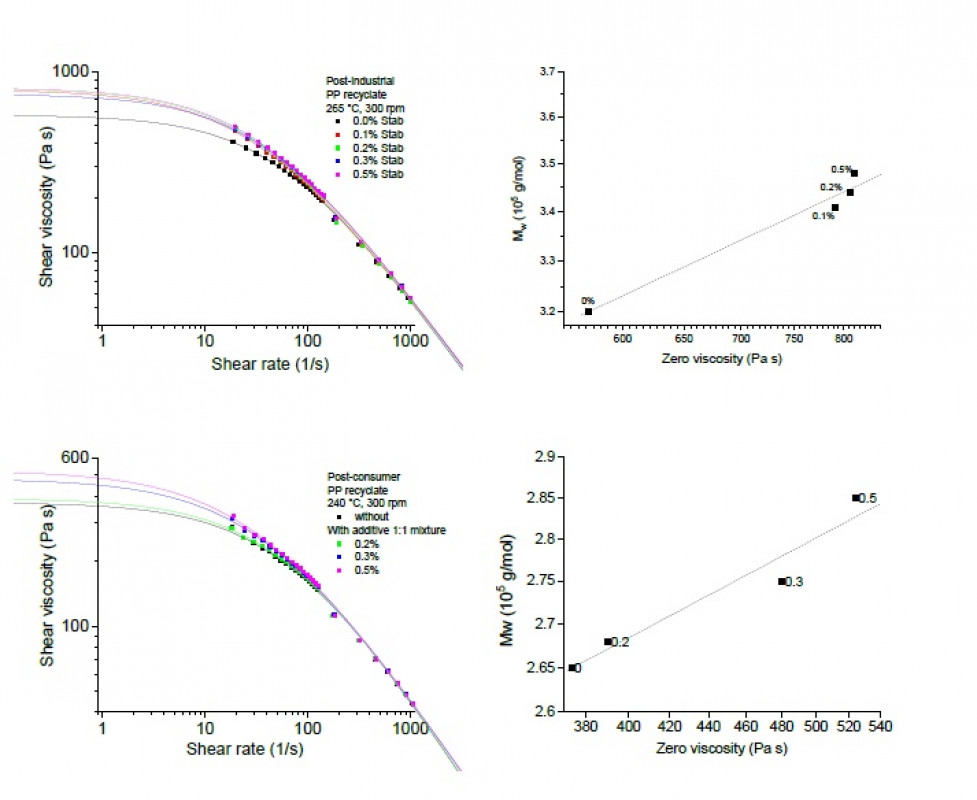
Making plastic formulations more profitable
The online rheological measurements can be used to draw meaningful conclusions about the number of antioxidants that should be added to the respective batch of used plastic. The online rheology presented here is available to Fraunhofer LBF project partners. Plastics processors thus receive immediate information on the effect of a process stabiliser and can produce their formulation more cost-effectively and make it more profitable.
In addition, the flow curves of the elongational viscosity reflect the stability of the melt. In contrast to shear viscosity, extensional viscosity is very sensitively influenced by the fibre content and fibre distribution. As melt stability is an important criterion for the use of a given compound for blow moulding processes, online rheology can also support the compound developer in this respect.
(Source: Fraunhofer Press Release)
Schlagworte
Circular EconomyPlasticsPolymerRecyclatesResearch