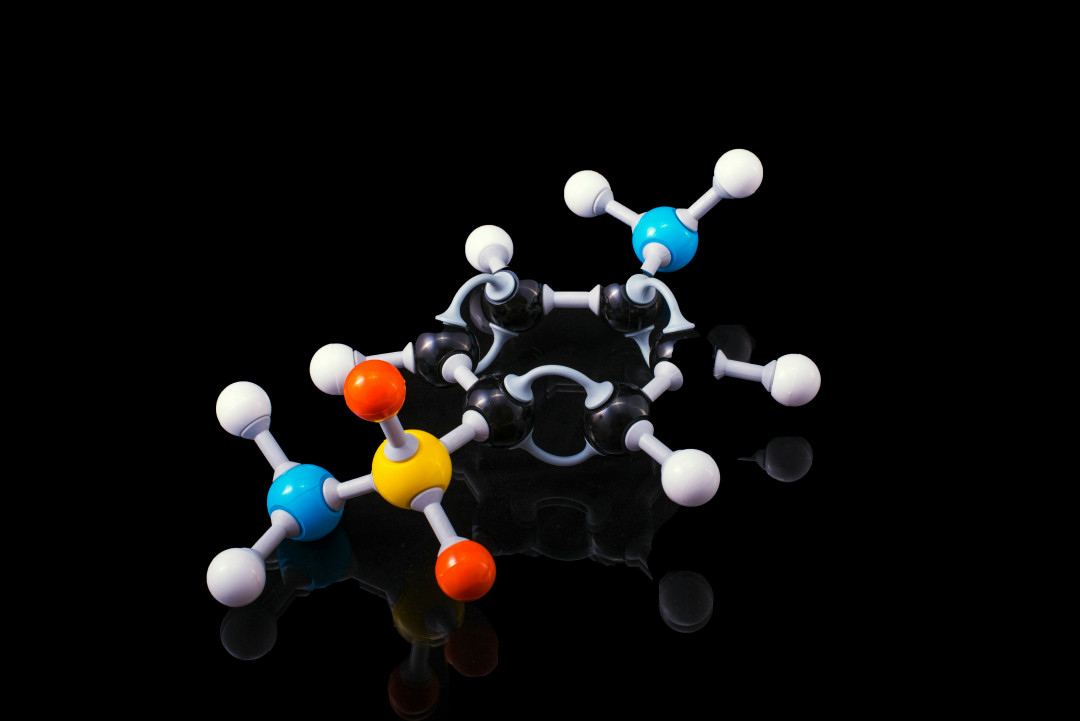
Lowering Cost using thermoplastic, fibre-reinvorced plastic pipes
Hydrogen is becoming increasingly important as an energy carrier within the context of the energy transition. However, the production of green hydrogen using polymer electrolyte membrane electrolysers (PEM electrolysers) is still very expensive due to the high cost of the equipment. A promising solution to reduce these costs lies in the use of thermoplastic, fibre-reinforced plastic pipes for the entire system periphery, replacing expensive steel materials.
This substitution offers significant savings potential, supported by automated manufacturing processes and efficient joining techniques, which are addressed by the "PolyH2Pipe" research project. This project is being realized in cooperation between the Institute for Plastics Processing (IKV), the Institute of Welding and Joining Technology (ISF) at RWTH Aachen, and the Federal Institute for Materials Research and Testing (BAM) across three joint projects as part of the AiF leading technology project "PolyH2Pipe" (IFG project 63-65 LN).
Pipe production
Pure thermoplastic piping systems are not durable under the process conditions occurring in electrolysers, such as internal pressures of up to 50 bar, temperatures of up to 100°C, and the different media used. For this reason, multilayer pipe systems are being developed as part of the project. The exterior of thermoplastic pipes is reinforced using a plastic-glass fibre laminate layer, whose matrix consists of the same material as the thermoplastic pipe, applied through a tape winding process. This ensures the required internal pressure resistance when handling various hydrogen-containing media such as H2/H2O, O2/H2O, deionised water, or H2O/glycol. The inside of the thermoplastic pipes is coated with a plasma coating to reduce the permeation of hydrogen out of the pipes and the penetration of foreign ions from the pipe into the medium being transported.
Joining of pipes
Since both the installation of the piping systems and the joining of the individual system components must be adapted to the process conditions of hydrogen production (temperature, pressure, and medium), the joining process plays an essential role. Therefore, both welding and adhesive bonding are considered in depth as possible joining methods for multilayer composite pipes. Both methods offer the potential to produce large-scale, reproducible joints, which are necessary to reduce the economic barriers to market entry for PEM electrolysers. The welding of multilayer composite pipes is carried out using heated tool butt welding and heated tool socket welding. The adhesive bonding aspects address the entire process chain, starting with the selection of adhesives, the optimisation of suitable long-term surface pretreatment methods and the design of the application in the final use.
Specially adapted couplings are developed as auxiliary elements for the welding and bonding processes to ensure maximum process reliability. However, the primary focus of all joining methods is on the permeation behaviour and durability over the lifespan under the process conditions during PEM electrolysis. These criteria are assessed through component characterisation of the joined multilayer composite pipes using optical and mechanical testing methods. A topological characterisation, as well as the quantification of resulting defects, is carried out through depth composition using a reflected light microscope. Mechanical tests identify not only the condition of the joint strength but also potential weaknesses in the connection. For this purpose, tensile tests, creep rupture tests, and burst pressure tests are conducted. At the conclusion of the project, all findings will be tested in real-world conditions to facilitate the rapid transfer into industrial application and economic utilisation.
The project is funded by the Federal Ministry for Economic Affairs and Climate Action based on a resolution of the German Bundestag.
Source and Contacts:
Institute for Plastics Processing in Industry and Craft at RWTH Aachen; Prof. Dr.-Ing. Christian Hopmann; Prof. Dr. rer. nat. Rainer Dahlmann; Patricia Fatherazi, M. Sc.; RWTH Aachen, Phone: +49 80-93806, e-mail: zentrale@ikv.rwth-aachen.de and Institute of Welding and Joining Technology (ISF); Prof. Dr.-Ing. Uwe Reisgen; Dr.-Ing. Alexander Schiebahn; Maximilian Heym, M. Sc.; RWTH Aachen, Phone: +49 80-96351, e-mail: office@isf.rwth-aachen.de.
Schlagworte
Energy TransformationHydrogenJoining PlasticsSteel