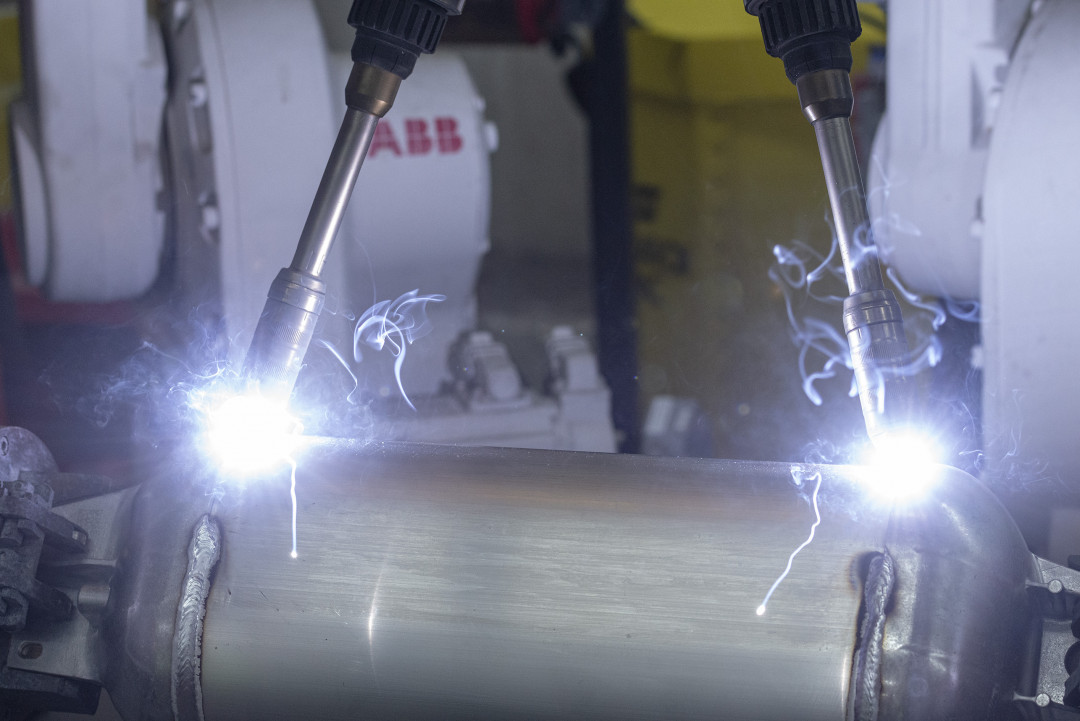
Making light work Saving CO2
The Salzburger Aluminium Group (SAG Group) integrates innovative lightweight construction into vehicle construction, helping to cut CO2 emissions. When sleek sports cars or high-end automobiles accelerate to sixty miles per hour in just a few seconds, lightweight rheocasting components from Austria are playing their part. Heavy goods vehicles also benefit from advanced lightweight components made by the SAG Group. They are welded using patented Cold Metal Transfer and WireSense technology from Fronius.
The SAG Group traces its origins back to Salzburger Aluminium AG, founded in 1898, and today employs around 1,100 people at nine locations in Europe, Mexico and the US. As a manufacturer of aluminium tanks for heavy trucks, SAG is a global supplier for many well-known OEMs. Other products include lightweight components for carriages, air reservoirs, air pressure tanks and special components for the car, commercial vehicle, rail and special vehicle industries.
Special rheocasting technology for the manufacture of highly robust lightweight components was brought to series maturity by the SAG Group after years of research. With this method, aluminium is not processed in a completely liquid state, as in conventional casting processes, but in a semi-solid or semi-liquid form and then turned into lightweight components for the automotive industry. The laminar, almost turbulence-free filling process prevents unwanted gas inclusions during casting. Cavities, so-called shrink holes, are sealed by shrinkage of the solidifying melt. This makes rheocasting components very easy to weld due to their low porosity. The process remains unique within the automotive sector. Compared to steel, rheocasting components are up to 60 % lighter. The innovative casting process also won an innovation award from Volvo due to the significant weight savings and other advantages.
WireSense compensates for air gap deviations
Before finally testing WireSense after several trials with various assistance systems and sensors, SAG was unable to find an ideal solution to compensate for manufacturing inaccuracies such as air gap deviations during joining. This impaired the welding process and had a negative impact on production times due to the unacceptably frequent need for constant rework.
Component deviations such as varying air gaps or clamping tolerances can cause severe welding problems. In the worst case scenario, these deviations result in a change in the welding position and cause a lack of fusion in the weld seam. For this reason, many manufacturing companies use optical measuring devices – so-called seam tracking sensors – for robotic welding. These are expensive, sit in front of the torch body and restrict component accessibility because of their disruptive contours. This in turn leads to problems with using cameras or lasers. They also need regular cleaning and require additional calibration between the Tool Center Point (TCP) and the sensor. WireSense by Fronius offers a simple alternative without restrictions.
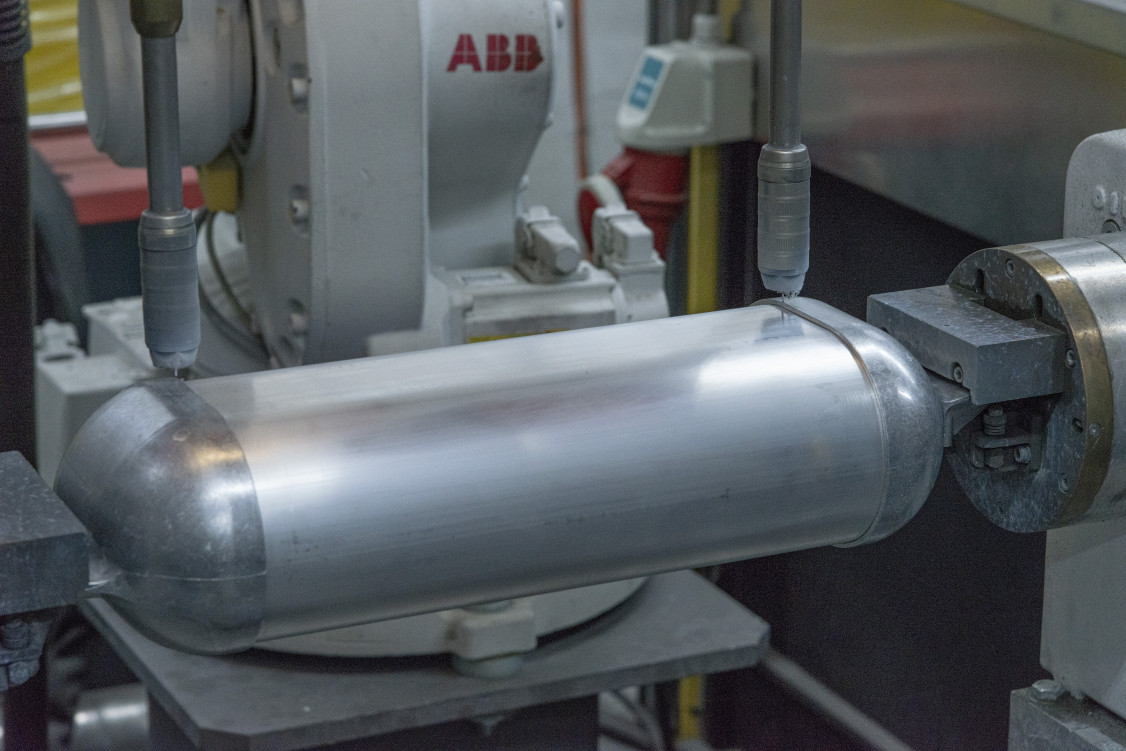
The science behind WireSense
WireSense technology does not require any hardware components – instead the wire electrode is used as a sensor that scans the component with a high-frequency reversing wire movement. Before this scanning process begins, an extremely low sensor voltage is applied to the welding wire and the current is simultaneously reduced to a minimum. When the robot moves to the required position and starts the WireSense process, the welding wire touches the component and creates a short circuit without arc ignition. The short circuit is then cleared by raising the wire. The change in the position of the welding wire at the instant the short circuit is created is analyzed by the intelligent TPS/i power source using special evaluation algorithms and presented as a height measurement signal. The reversing wire movements take place in milliseconds. By evaluating the individual pieces of height information, the robot not only determines the edge misalignment and the position of the individual sheets in relation to each other, but also the actual edge height.
In the case of lap joints such as those used in SAG’s air pressure tanks, WireSense detects the weld seam path, reacts to any deviations and corrects the originally created welding program. It can be used equally with steel, stainless steel, aluminum and other alloys.
CMT technology is a basic requirement
WireSense can be used with any Fronius TPS/i welding system configured to use the cold metal transfer welding process. The precise wire movement resulting from the interaction between the wirefeeder on the wire drum, the wire buffer and the second Robacta Drive CMT wirefeeder which sits directly on the torch body, is crucial. The metal surface is scanned and the weld contour detected in a reversing wire movement that takes place at around 100Hz.
(Source: Fronius International GmbH Press Release)
Schlagworte
AluminiumLightweight ConstructionWelding