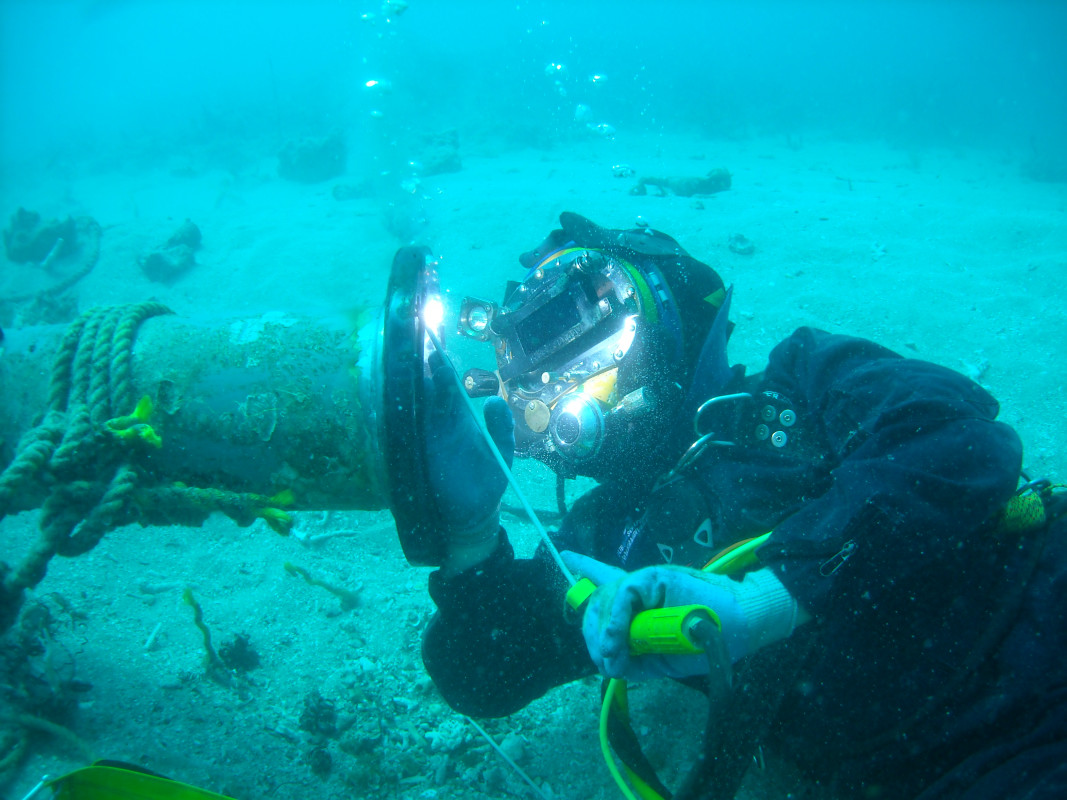
Hyperbaric wet welding – factors influencing the weld quality
There are several different factors influencing the quality and the ease of production of underwater wet welding. The figure below gives an overview of the most important factors in question. In the following subsections of the influencing factors are briefly discussed.
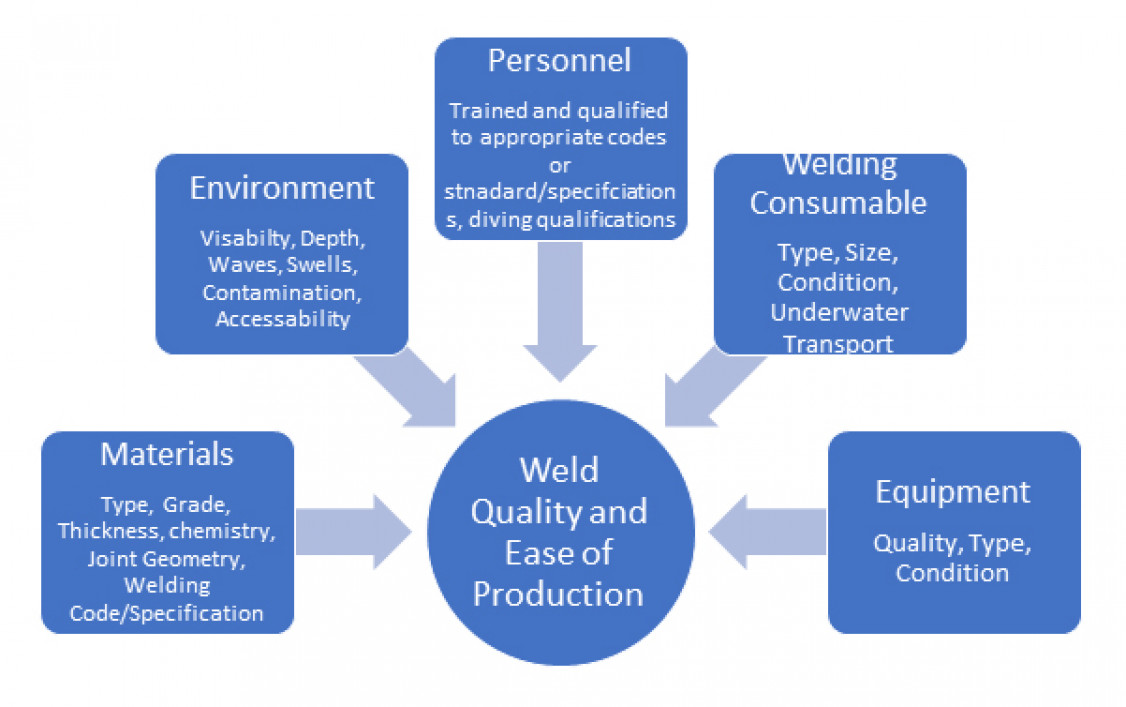
Materials
Steels
Wet welding is performed in a wet environment that is “hostile” to both the weld and the welding process. Welding in a wet environment results in higher cooling rates and produces significant amounts of martensite in the heat affected zone (HAZ) in almost all low alloy steels. The IIW (International Institute of Welding) formula for calculating the carbon equivalent (CE) is used to determine the wet weldability of steels. Materials with a higher CE may have a highly martensitic microstructure and become increasingly susceptible to cracking. When the CE value of low carbon steels approaches 0.4, the fusion line hardness may exceed the HV 400 hardness value on the Vickers scale. The generally accepted CE upper limit for wet welding with ferritic electrodes is ≤ 0.4. The ideal materials for wet welding should have a CE ≤0.38% and a carbon content of C≤ 0.16%.
Joint geometry
Fillet welds
The root gap for a fillet weld should be kept to a minimum (approx. 1 mm). If the gap exceeds 2.5 mm, the gap should be reduced by build-up welding, rather than trying to bridge the gap with a single weld bead. Always weld multi passes to increase weld ductility and strength due to tempering effect of subsequent weld passes, with three passes being a recommended minimum.
Groove welds
Penetration is extremely difficult to control in welds with an open root gap. If a partial joint penetration (PJP) is unacceptable, a fusible backing bar is required. To ensure good access to the root, a larger root opening is essential. If the use of a fuseable backing bar is not possible, the weld joint needs to be prepared with no root gap, but with a root face ≥3 mm. After welding the first side, the root side of the joint needs to be back gouged and filled with weld metal. If the root side is not accessible, either a doubler plate can be welded over the area to be repaired or, in the case of a pipe, a scalloped sleeve may be considered.
Welding Positions
Underwater wet welding can be performed, as top site welding in all positions, flat, horizontal, vertical and overhead, with welding performed vertically, the progression will be downward (downhill). Due to the emerging upward traveling bubbles, the diver would not be able to see the weld joint. Welding downhill underwater will produce, unlike on top site a deep penetration, as shown in photograph below. Due to the fast-freezing weld puddle, welding downhill underwater will also be performed at a relatively slow travel speed.
Codes and specifications
In the following, codes and specifications related to underwater welding are being presented. What code or specification to be used is usually dictated by the project specifications, or other applicable rules or regulations.
AES D3.6M: Underwater welding code
First published in 1983, AWS D3.6 became the industry standard for all welding operations under hyperbaric conditions, particularly wet welding. Subsequent editions of the standard were published in 1989, 1993, 1999, 2010. The current edition was published in 2017. The next edition is planned to be published in 2025. The current edition of AWS 3.6 specifies three quality classes (A, B and O). These three quality classes cover the spectrum of quality and properties that can currently be achieved by underwater welding in both dry and wet environments.
Each weld class defines a set of criteria for weldment properties that must be established during qualification, and a set of weld soundness requirements that are to be verified during construction. The standard does not address the selection of the class that meets the service requirements of a particular application. The selection of the class of weld to be provided is to be determined by the customer or regulatory body.
A weld class specifies a level of serviceability and a set of required properties, as defined by mechanical tests, surface appearance, and nondestructive examination requirements, to which welds of a given class must conform.
There are three weld classes to choose from.
- Class A
Welds suitable for applications and design stresses comparable to conventional surface welded counterparts by virtue of specifying comparable properties and testing requirements. - Class B
Intended for less critical applications where lower ductility, moderate porosity, and other limited discontinuities can be tolerated. - Class O
Class O underwater welds must meet requirements of another designated code/standard, as well as additional requirements, specified in AWS D3.6, to deal with the underwater welding environment.
ISO standards for underwalter wet welding
- ISO 15618-1:2016: Qualification testing of welders for underwater welding — Part 1: Hyperbaric wet welding.
- ISO/DIS 15614-9: Specification and qualification of welding procedures for metallic materials — Welding procedure test — Part 9: Underwater hyperbaric wet welding. (scheduled to be published at the end of 2024 or during 2025).
EWF European federation for welding, joining and cutting
- EWF-570r1-14/SV-00: Minimum requirements for the education, examination and qualification of European Manual Metal Arc (MMA)-Diver-Welder.
DIN standards for underwater wet welding
- DIN 2302:2005: Schweißzusätze - Schweißzusätze für das Nassschweißen unter Überdruck von unlegierten Stählen und Feinkornstählen - Abnahmebedingungen für die Prüfung und Qualifizierung von Schweißzusätzen für das Nassschweißen unter Überdruck
(zurückgezogen)
(Welding consumables – welding consumables for underwater hyperbaric wet welding of non-alloy and fine grain steels – Acceptance specifications for testing and qualification) (withdrawn). - DIN 2302:2018: Schweißzusätze — Umhüllte Stabelektroden zum Lichtbogenhandschweißen von unlegierten Stählen und Feinkornstählen in nasser Überdruckumgebung — Einteilung
(Welding consumables — Covered electrodes for manual metal arc welding of non-alloy and fine grain steels in a wet hyperbaric environment — Classification) - DIN EN ISO 15618-1: Prüfung von Schweißern für Unterwasserschweißen - Teil 1: Unterwasserschweißer für Nassschweißen unter Überdruck
(Qualification testing of welders for underwater welding — Part 1: Hyperbaric wet welding).
AWS standards
- AWS D3.6M:2017 Underwater Welding Code
- AWS A5.35/A5.35M: 2015 Specification for Covered Electrodes for Underwater Wet Shielded Metal Arc Welding
DVS guidelines and standards
- Richtlinie DVS 1801 Anforderungen an Betriebe und Personal für das nasse Unterwasserschweißen – Herstellerqualifikation (Requirements for companies and personnel for underwater wet welding – manufacturer qualification).
- Richtlinie DVS 1811 Lichtbogenschweißen unter Wasser (Underwater arc welding)
- Merkblatt DVS 1812 Arbeitsschutz beim Unterwasserschweißen und -schneiden (Safety in underwater wet welding and cutting).
- Merkblatt DVS 1813 Unterwasser-Lichbogenhandschweißen mit umhüllten Stabelektroden (Manual underwater arc welding with covered stick electrodes).
- Merkblatt DVS 1814 Gefahren durch elektrischen Strom beim nassen Unterwasserlichtbogenschweißen und notwendige Schutzmaßnahmen (Electrical shock hazards while manual underwater wet welding and required protective measures).
Environment
Environmental influences can significantly affect both the welding process, and the quality of the weld produced. Some of these challenges are:
- Water depth: Water depth has a direct impact on weld quality and is an essential variable in the Welding Procedure Specification (WPS). As depth increases, micropores increase and ductility decreases.
- Visibility: Visibility has a direct impact on weld quality. Restricted visibility can affect the welder diver's ability to see the arc and inspect the resulting weld.
- Water- or ship movement: Has a direct impact on the quality of welding. Swells, waves, water currents or the movement of the ship can have a detrimental effect on the welder diver to remain stable.
- Contamination: A special diving suit that restricts freedom of movement may be required.
- Access: Is the joint to be welded accessible to weld according to the WPS?
Personnel/Training
Wet welder training provides opportunities to learn and experiment with the wet welding process while being under tuition. Historically and currently, it is commonly assumed that qualified and experienced top site welders can easily apply his/her skills underwater without the need for further training. Experienced top site welders may find it difficult to break habits that work fine on the surface but may be difficult if not impossible to apply underwater.
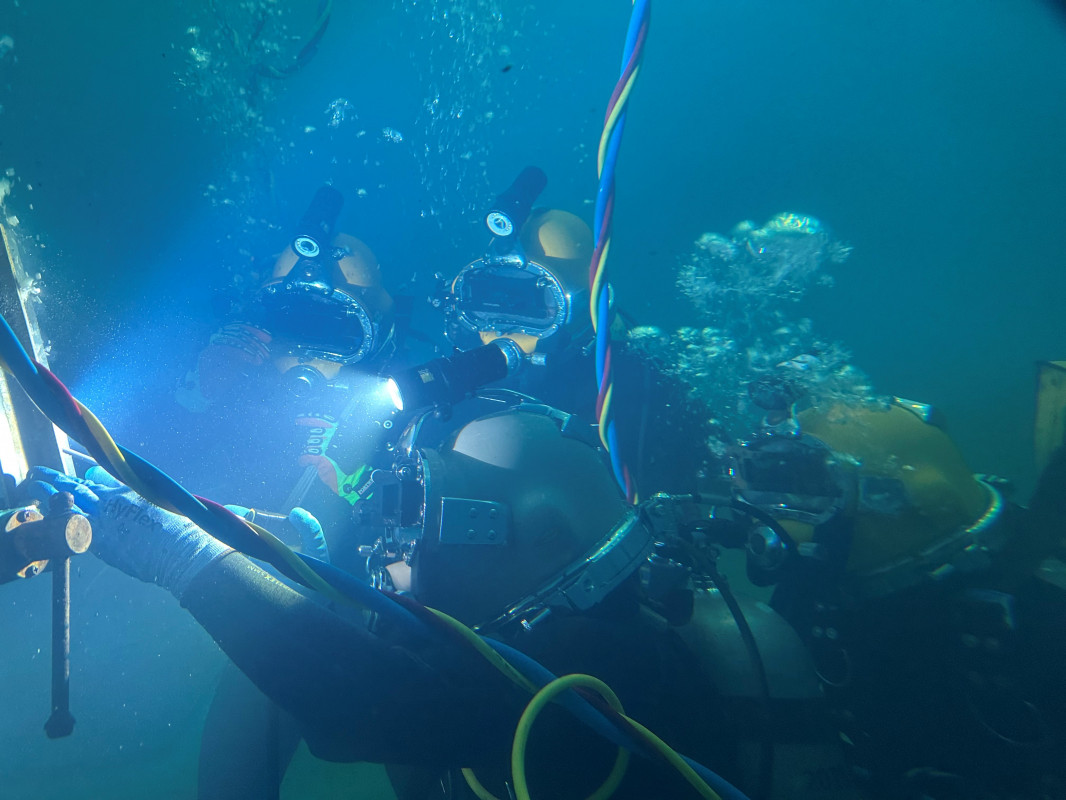
Underwater wet welding electrodes
Historically wet welding was completed using surface welding electrodes that were modified to keep the flux in place underwater during welding by applying electrical tape, wax, lacquer or paint to the flux. Some of these electrodes produced reasonably looking welds but their mechanical properties and user friendliness were comparatively poor. The development of new purpose-built welding electrodes improved the weld quality significantly.
Almost all underwater wet welding is performed with the shielded metal arc welding (SMAW-111) process. Extensive research was performed regarding underwater wet welding with the flux cored arc welding (FCAW) process. The development of welding equipment for FCAW is still ongoing.
Welding Equipment
For underwater wet welding, the type and condition of the welding equipment is essential. Poorly maintained or damaged equipment can affect arc performance and the quality of the resultant weld, in particular the equipment which is submerged underwater such as: Welding cables, connectors, electrode holder, earthing clamp/plate. Current leakage through the water will reduce the amount of current getting to the tip of the electrode and may/likely result in electric shock to the diver.
Come back tomorrow for more information on case studies.
Authors
Uwe Aschemeier, SGS Subsea Global Solutions, Miami FL, USA
Kevin Peters, SGS Subsea Global Solutions, Miami FL, USA
Schlagworte
Hyperbaric dry weldingHyperbaric wet weldingUnderwater Welding