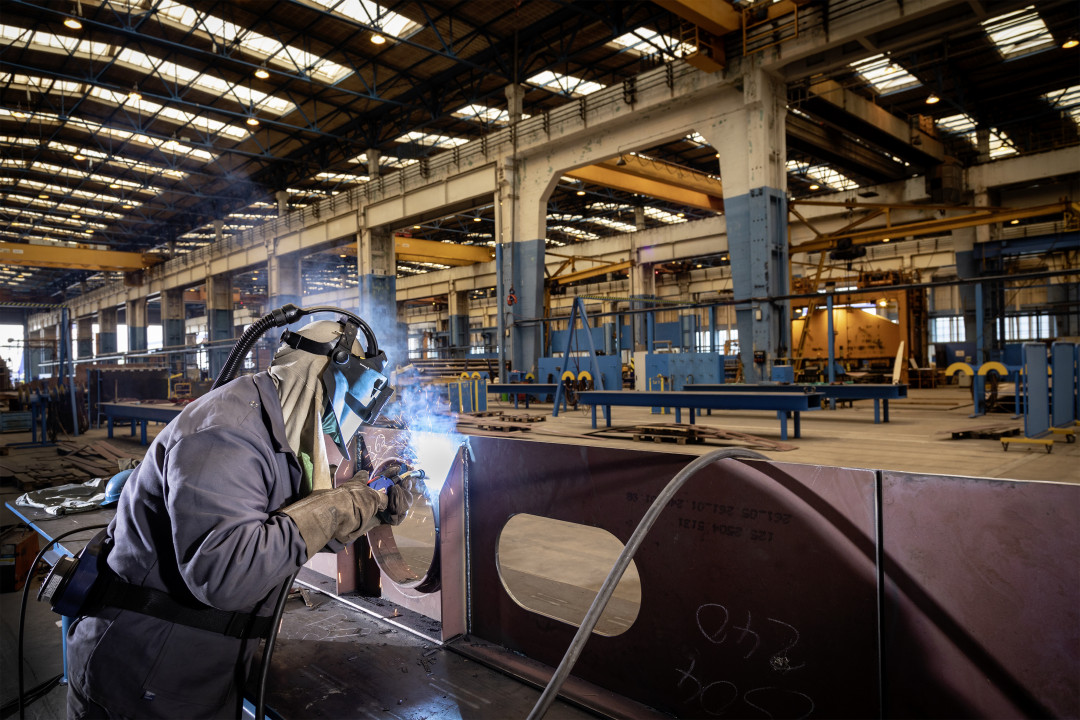
Beyond the Limits of PPE
The fact that personal protective equipment (PPE) must be used to protect against weld spatter, radiation, noise and harmful fumes during welding is basic knowledge for anyone who welds. But what can you do when these protective measures reach their limits?
Additional protection against fumes
PPE is mandatory when welding. But the problem is evident in the name itself: Personal protective equipment is used exclusively for your own protection. Radiation, fumes, ozone and other hazards are dispersed around the welding area and posing a risk to other employees working nearby. They inhale everything unfiltered with the air they breathe. Unfortunately, this fact is often overlooked.
In areas with extensive welding, stationary hall extraction systems or hood extraction systems are typically used. When working with a hood extraction system, the hood must always be positioned precisely over the weld in order to absorb as many fumes as possible. The problem: Moving the extraction funnel is inconvenient and often forgotten. Extraction systems mounted on the hall ceiling often recirculate the air throughout the entire hall. With both solutions, the fumes first have to rise before they can be captured by the extraction system. Fine dusts have ample time to disperse further. Welding specialists can protect themselves by wearing a helmet with a fresh air supply, but everyone else in the vicinity breathes in the fumes.
Best: extraction at the source
The German “Gefahrstoffverordnung” (Hazardous Substances Ordinance) GefStofV Annex I No. 2 – DGUV information “Effective capture and separation of welding fumes”, as of 25.10.2021) clearly states (translated from the original): “A safe method of protecting welders and other employees in the vicinity from welding fumes is to capture the welding fumes at their point of origin. This prevents them from entering the welder's breathing zone and the hall air in the first place. For this purpose, either torch-integrated capture systems must be used or suitable capture elements must be positioned close to the source [...].”
Extraction at the source – so-called spot extraction – is the safest method of protecting welding personnel from harmful fumes. The system of the xFUME line from ABICOR BINZEL offers such a method. If the extraction torch is in its ideal position for fume extraction, between 90 % and 99 % of the fumes can be extracted – provided an extraction unit from the xFUME line is also in use. In this case, as much as 99.95 % of these absorbed dust particles > 0.1 µm are absorbed in the filter system of the extraction unit. This is referred to as separation efficiency.
The ideal extraction torch for every requirement
The xFUME range of extraction torches suits every requirement. The xFUME COMPACT is ideal for smaller repair and workshop jobs. For more demanding tasks with longer welding times, an extraction torch from the gas or liquid-cooled xFUME PRO series is the most suitable option. If thick sheets with high currents are frequently welded, the liquid-cooled xFUME PRO HD (HD = Heavy Duty) should be used. The gas cooled xFUME TIG is the best choice for very fine TIG welding work where the main focus is on the appearance of the weld seam and high-alloy stainless steel or aluminium is processed.
Spot extraction can be used not only for manual welding, but also for automated welding. Why is this necessary? Wherever automatic welding machines or welding robots are in use, there are also people working, such as loading the machines. ABICOR BINZEL's automatic extraction torches from the xFUME AUT line and the xFUME ABIROB robot extraction torch from the xFUME ROBO line can be used for this purpose.
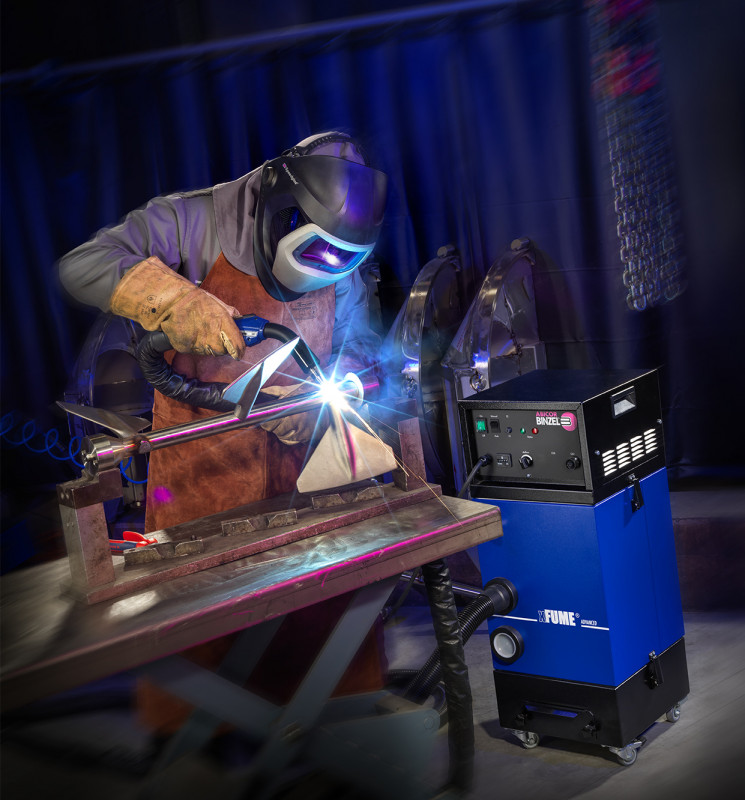
Best utilized together: Extraction torch & extraction unit
For optimal extraction performance, extraction torches and units must be properly matched. All fume extraction torches from ABICOR BINZEL guarantee reliable and safe fume extraction with, for example, the xFUME ADVANCED W3 extraction unit. The W3 marking indicates that this fume extraction unit can also be used when welding alloyed steel. This is because highly harmful dusts containing alloy components such as nickel and chromium as well as nickel-based alloys are produced, which must not enter the respiratory organs under any circumstances. Many welders tend to be dismissive of fume extraction torches because they typically associate them with bulky, heavy welding torches that lead to early fatigue and obstruct a clear view of the welding process due to their size. However, modern fume extraction torches are no longer comparable with their predecessors. Development has advanced to the point where it feels like holding a standard welding torch. With their more streamlined design, they also provide a clear view of the process.
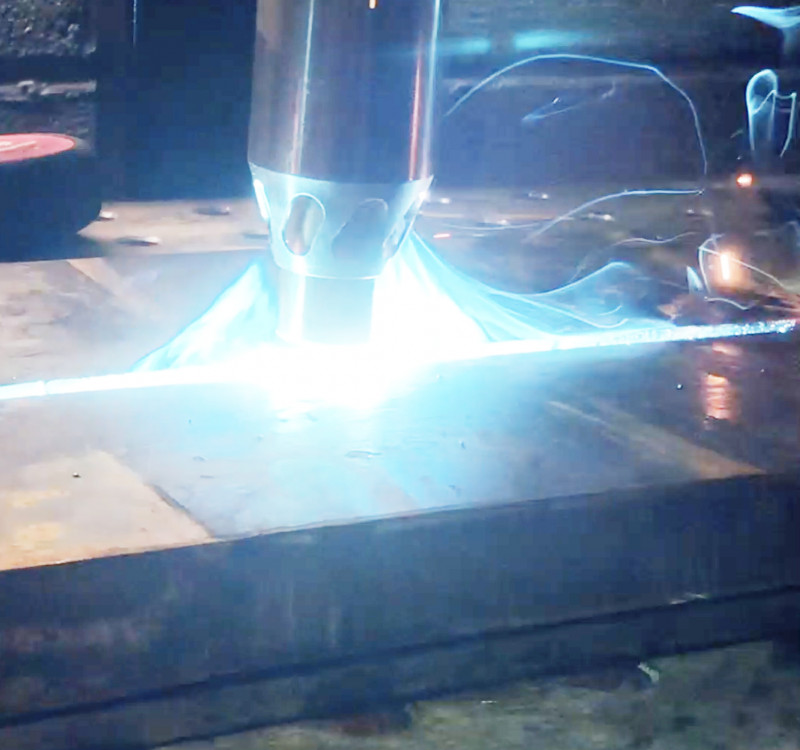
To ensure optimal protection for all your employees from welding fumes, PPE is insufficient. The most effective approach is to rely on spot extraction, i.e. extraction at the source.
(Source: ABICOR BINZEL Press Release)
Schlagworte
ExtractionFumesPPEWeld FumesWelding