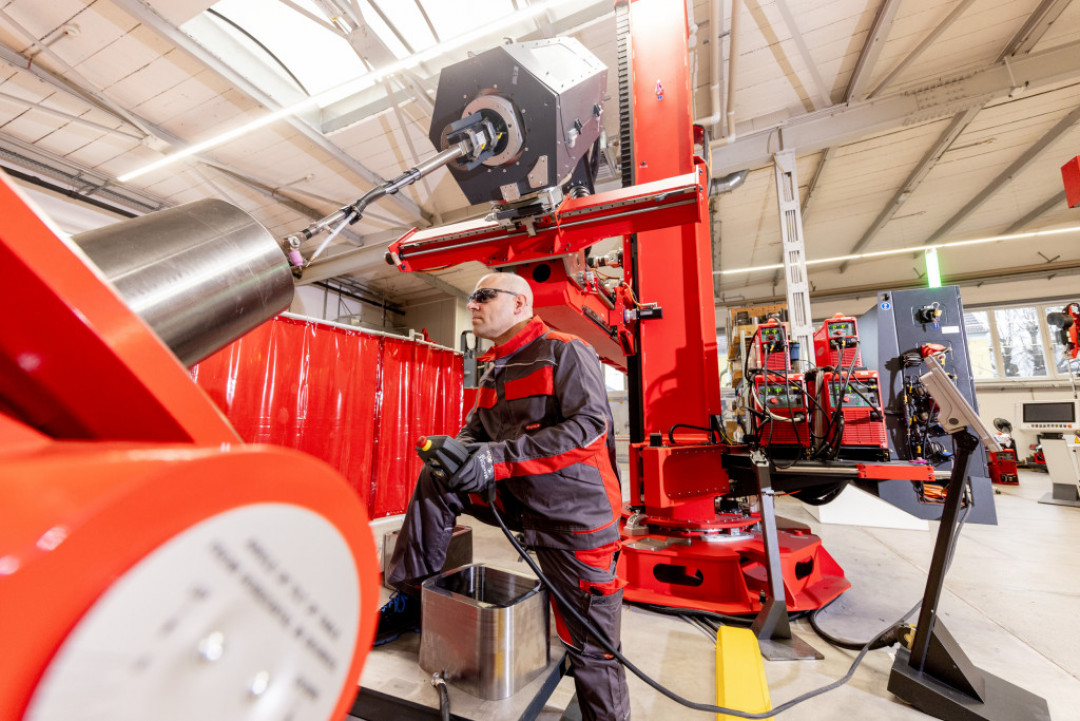
Cladding hat einen Partner: die Fronius Welding Automation
Fronius ist einer der weltweit führenden Hersteller von Auftragschweißsystemen. Immer wieder bringt das Unternehmen innovative Neuheiten wie das nachrüstbare, mit dem Excellence-in-Welding-Award ausgezeichnete SpeedClad-2.0-Verfahren auf den Markt. Als Generalunternehmer bietet man seinen Kunden entscheidende Vorteile: Sie alle erhalten ihre Anlagen aus einer Hand – inklusive Inbetriebnahme. Dabei ist die Fronius Welding Automation von Anfang an und während der gesamten Lebensdauer einer Schweißanlage um einen kompetenten, kundenfreundlichen Service bemüht. Nicht zuletzt profitiert jeder einzelne Anwender und jede einzelne Anwenderin von Cladding-Systemen, die dank Update-Möglichkeiten und Retrofit über Jahre hinaus dem neuesten Stand der Technik entsprechen.
Über den gesamten Produktlebenszyklus an der Seite der Kunden
Von der Planung über Engineering, Fertigung und Inbetriebnahme bis hin zur Wartung und Instandhaltung von Cladding-Systemen: Die Fronius Welding Automation steht mit ihrem weltweiten Service- und Partnernetzwerk verlässlich an der Seite ihrer Kunden. Stets im Fokus steht dabei das perfekte Cladding-Ergebnis. Sämtliche Systeme werden im Sinne der Anlagensicherheit nach internationalen Compliance-Standards gefertigt. Die technische Inbetriebnahme durch Fronius Expertinnen und Experten und die Vorabnahme durch Käufer aus der Öl- und Gasindustrie erfolgen am Fertigungsstandort im österreichischen Steinhaus. Anschließend werden die Anlagen geliefert, am Einsatzort – zum Beispiel in Saudi-Arabien, England oder den USA – installiert und von internationalen Kunden aus dem On- und Offshore-Bereich endgültig übernommen. Expertentrainings und Prozessoptimierungen während des Produktionsstarts sind Teil des umfangreichen Fronius Inbetriebnahme-Service.
Realitätsnahe Schweißversuche und Machbarkeitsstudien
Neue Cladding-Projekte startet die Fronius Welding Automation mit Machbarkeitsstudien und Schweißversuchen. Auftragschweißen ist hochkomplex. Neben dem Grundmaterial der zu beschichtenden Komponenten spielen auch Parameter wie Stromstärke, Drahtgeschwindigkeit, Schweißgeschwindigkeit, Zusatzmaterial, Schutzgas, Umgebungstemperatur oder Luftfeuchtigkeit eine entscheidende Rolle. Bereits geringfügige Abweichungen können ungewollte Auswirkungen auf das Schweißergebnis haben. Deshalb sollten Schweißversuche so realitätsnah wie möglich ausgeführt werden – mit Bauteilen, Zusatzmaterialien und Schutzgasen, die auch im späteren Realbetrieb zum Einsatz kommen. Wenn möglich unter den gleichen klimatischen Verhältnissen, wie sie später am Einsatzort vorherrschen. Lässt sich Letzteres nicht realisieren, müssen die Schweißparameter während der Inbetriebnahme an die Produktionsumgebung angepasst und optimiert werden. Um keine Überraschungen zu erleben, am besten von Fronius Expertinnen und Experten.
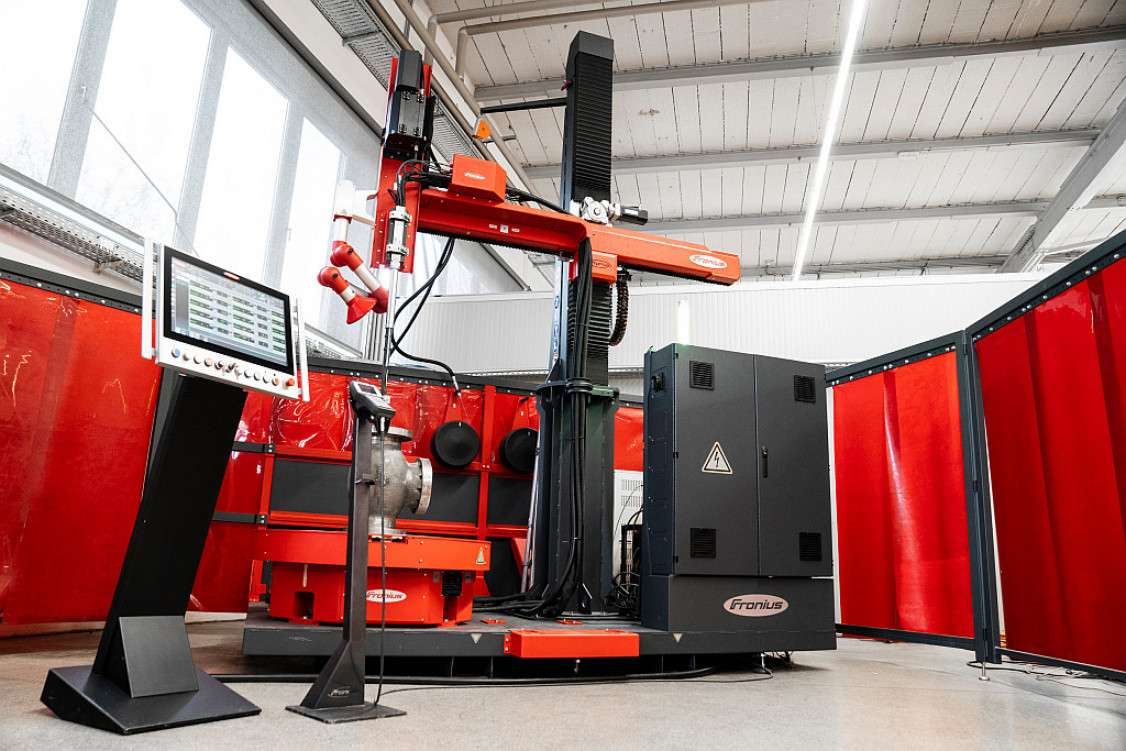
Anton Leithenmair, Head of Welding Automation: „Für ein kundengerechtes Customizing von Cladding-Anlagen benötigen wir von Anfang an einen offenen und vertrauensvollen Informationsaustausch. Gibt es Vorgaben beim Zusatzmaterial und Schutzgas? Wie sieht es mit den klimatischen Verhältnissen vor Ort aus? Besonders wichtig ist, dass wir unsere Schweißversuche mit Originalbauteilen durchführen können und nicht auf Dummys zurückgreifen müssen. Nur so können unsere Anlagen auch im harten Dauerbetrieb die gewünschten Schweißergebnisse liefern.“
Komplettlösungen für die Öl- und Gasindustrie
Erfahrung ist das Reservoir, aus dem die Fronius Welding Automation innovative Ideen für neue Systemlösungen schöpft. Seit über 40 Jahren entwickelt Fronius anwendungsbezogene Cladding-Systeme, die entweder standardisiert zum Einsatz kommen oder für spezielle Kundenanforderungen modifiziert werden.
Compact Cladding Cell (CCC) – smart und anwenderoptimiert
Mit einer Standfläche von 6 m² (64,5 ft²) ist die auf einer transportablen Plattform montierte Compact Cladding Cell die kompakte Lösung im Bereich des Auftragschweißens. Entwickelt wurde sie für kosteneffizientes Innenplattieren von Ventilkomponenten. Die maximale Bohrungstiefe und der größtmögliche Bauteildurchmesser betragen 1 m (0,39 in), das höchste Bauteilgewicht 2.500 kg (5.511,56 lb). Trotz ihrer Kompaktheit ist die Anlage ein extrem leistungsfähiges Cladding-System. Sie besticht durch einfache Bedienung, präzise Bewegungsabläufe und umfassende Datenaufzeichnungsmöglichkeiten.
Ergonomisches Design mit Drahtrollenaufnahme in Bedienhöhe, Brenner-Schnellwechselsystem und Stromquellen auf einem Schienenauszug sprechen für sich. Dazu kommen innovative Softwarefunktionen, maximale Prozesssicherheit und höchste Zuverlässigkeit im Dauereinsatz. Die Automatic-Multi-Sequence-Funktion erlaubt das Speichern mehrerer Schweiß- und Bewegungsparameter in Form von Sequenzen. Ausgehend von der Home-Position werden sie der Reihe nach vollautomatisch ausgeführt. Einen überdurchschnittlichen Bedienkomfort bietet die HMI-Systemsteuerung mit 21-Zoll-Touchdisplay, Real-Time-Prozessvisualisierung, Multi-User-Verwaltung und vielem mehr. Wird höchstmögliche Produktivität gefordert, ist der optional erhältliche SpeedClad-2.0-Prozess Gebot der Stunde.
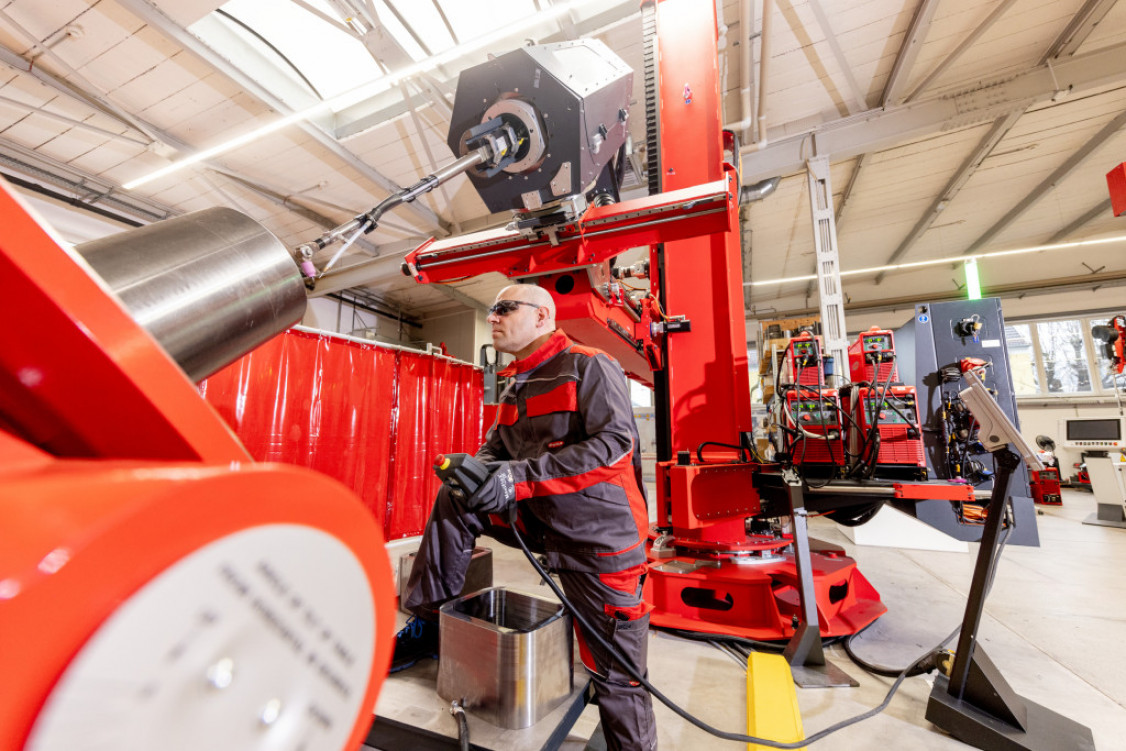
Endless Torch Rotation System (ETR) – nahezu unbegrenzte Möglichkeiten
Das ETR-System wurde für große, komplexe Komponenten entwickelt und ist seit Jahren etabliert. Das Herzstück ist ein endlos rotierender Schweißkopf. Dieser ermöglicht das Schweißen von Bauteilen mit unterschiedlichen Bohrungen und Bohrungswinkeln bis zu einem Innendurchmesser von 1 m (0,39 in). Dabei rotieren Brenner und Drahtvorschub gemeinsam um die Bohrungsachse. Die Bauteile werden vollautomatisch zentriert. Das verkürzt die Rüstzeiten erheblich und spart Produktionskosten. Besteht die Gefahr einer Brennerkollision mit dem Bauteil, stoppt die elektropneumatische Kollisionserkennung alle Bewegungsachsen und schützt den Brenner vor Beschädigung. Zuletzt hat Fronius seinem erfolgreichen ETR-System das noch flexiblere ETR-Ultimate-System zur Seite gestellt. Die vielseitige Anlage ermöglicht neben Cladding-Aufgaben auch das Fügen größerer Bauteile mit herausfordernden Geometrien und schwierig zu schweißenden Nahtverläufen. Wie bei der Compact Cladding Cell sind sowohl beim ETR- als auch beim ETR-Ultimate-System die komfortable 21-Zoll-Systemsteuerung mit Touchdisplay, Real-Time-Prozessvisualisierung und Multi-User-Verwaltung Standard. Gleiches gilt für das zeitsparende Brennerschnellwechselsystem. Bei Bedarf bewegen sich Schweißbrenner und Positionierer bei beiden Systemen – ETR und ETR-Ultimate – synchron. Auch hier verleiht SpeedClad 2.0 dem Cladding-Prozess höchste Produktivität.
Alle Parameter live im Blick
Großer, intuitiv bedienbarer 21-Zoll-Touchscreen, Multi-User-Accounts mit individueller Berechtigungsvergabe, Prozessvisualisierung in Echtzeit, Parameteranpassung on-the-fly, innovative Funktionen wie X-Ray-View, Component-Editor, Bore-to-Bore-Advanced, Istwert-Monitoring in Echtzeit, STEP-File-Import – all das macht die HMI-T21 zu einer Systemsteuerung der Industrie 4.0. Und natürlich ihre Fernwartungsmöglichkeit. Die X-Ray-View stellt Bauteile transparent dar und bietet eine exzellente Sicht auf das Bauteil. Sind mehrere versetzte Querbohrungen mit Winkeln ungleich 90° oder Flansche mit Bohrungen zu beschichten, hilft die Funktion Bore-to-Bore-Advanced. Alle relevanten Schweißparameter werden live im systemintegrierten Istwert-Monitoring dargestellt.
Eine Bedienung, die keine Wünsche offenlässt
Im Component-Editor legt die Schweißfachkraft Bauteile Schritt für Schritt an. Sie nutzt dafür den Touchscreen der HMI-T21. Höhe und Durchmesser werden per Eingabe definiert. Die diversen Komponenten scheinen dabei in Echtzeit als 3-D-Grafiken am Bildschirm auf. Neben zylindrischen sind auch flache und konische Formen möglich. Bohrungen sowie Extensions – zum Beispiel Flansche – können ebenfalls modelliert werden. Die bei Fronius integrierte CNC-Technologie erlaubt noch mehr Bauteilgeometrien als bisher: Zum Beispiel sind Verschneidungsbohrungen an konischen Bauteilen möglich. Programmiert werden die Schweißabläufe im Program-Editor. Bedienerinnen und Bediener wählen die einzelnen Abschnitte der Bauteile aus und bestimmen die Schweißfolge. Standardgemäß ist die Schweißrichtung von unten nach oben festgelegt, kann aber bei Bedarf geändert werden. Hilfreich: Am Startpunkt lässt sich der Brenner einblenden.
Sämtliche Schweißparameter werden im Weld-Editor definiert. Das System bietet eine Auswahl von Jobs mit festgelegten Parametern, die jederzeit angepasst werden können – auch on-the-fly im Menü Weld-Adjust. AVR (Actual Value Recording) zeichnet die Istwerte von Schweißstrom, Spannung, Drahtgeschwindigkeit, Gasmenge und Schweißposition während der Schweißvorgänge in tabellarischer Form auf. Optional sind für grafische Auswertungen und Analysen die PC-Softwarepakete Data Logger HMI und Data Viewer HMI erhältlich.
Sobald die Home-Position des Brenners kalibriert ist, bewegt er sich bei jeder Cladding-Anwendung selbstständig zum Startpunkt. Siegfried Wiesinger, Cladding-Experte bei Fronius, erläutert: „Unmittelbar vor dem Zünden lassen sich verschiedene Parameter noch mit dem Fernregler feinjustieren – zum Beispiel mit der AVC-Funktion (Arc-Voltage-Control-Funktion) der Startpunkt und Brennerabstand zum Bauteil.“
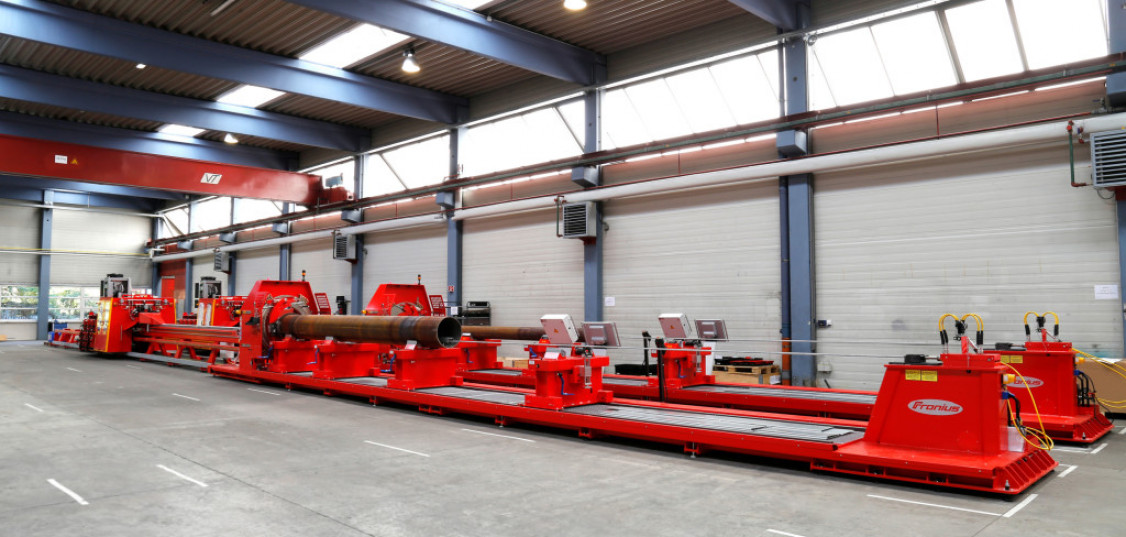
SpeedClad 2.0 – preisgekrönt und rasend schnell
Schneller, effizienter, wirtschaftlicher: Mit SpeedClad 2.0 setzt Fronius neue Maßstäbe beim Auftragschweißen von Ventilkomponenten. Verglichen mit den branchenweit verwendeten gepulsten WIG-Heißdraht-Prozessen ist SpeedClad 2.0 deutlich wirtschaftlicher. Die Innovation besticht durch hohe Abschmelzleistung, beeindruckende Geschwindigkeit und geringen Schutzgasverbrauch. Aufgrund der hervorragenden Resultate wurde der Prozess mit dem Excellence-in-Welding-Award der American Welding Society ausgezeichnet. Die Verleihung fand am 13. September 2023 auf der FABTECH in Chicago statt. Folgende Fakten überzeugten die Jury: Die Abschmelzleistung der beim Plattieren verwendeten Nickelbasislegierung wurde von 1,63 kg (3,59 lb) auf bis zu 6 kg (13,23 lb) / h erhöht, wobei Fronius anstelle des 1,14-mm-Drahtes (0,045 in) ab sofort einen 1,6-mm-Draht (0,063 in) verwendet. Die Schweißgeschwindigkeit wurde von 33 cm (13 in) / min auf bis zu 135 cm (53 in) / min erhöht und der durchschnittliche Impulsstrom von 240 Ampere auf 460 Ampere gesteigert. Dies garantiert allen Fronius Kunden einen idealen Wärmeeintrag bei gleichzeitiger Reduktion des Argon-Gasverbrauches von 516 l / kg auf bis zu 140 l / kg. Mit dem völlig neu entwickelten Brennersystem können bedeutend schmälere Bauteilbohrungen plattiert werden: 100 mm (3,94 in) anstelle von 150 mm (5,91 in). Als Ausgangsbasis für die Optimierung des Cladding-Prozesses diente die Wärmeeintragsformel: Wärmeeintrag = Volt x Ampere x 60 / Schweißgeschwindigkeit. Nachhaltigkeit ist Fronius Welding Automation in die Gene geschrieben, deshalb sind viele ihrer Innovationen nicht nur mit technischen Verbesserungen, sondern auch mit der Reduktion von Verbrauchstoffen verbunden – so auch der SpeedClad-2.0-Prozess.
Auch Längs-, Rundnaht- und Roboterschweißsysteme im Portfolio
Als Lösungsanbieter erzeugt die Fronius Welding Automation nicht nur Cladding-Anlagen, sondern auch mechanisierte Schweißsysteme und Roboterschweißsysteme für alle Branchen. Beispiele dafür sind Längsnaht- und Rundnahtschweißsysteme, Schweißtraktoren und Handling-to-Welding-Roboteranlagen. Kollaborierende Systeme, intelligente Sensorik, Softwarelösungen für das Datenmanagement sowie Offline-Programmierung samt Schweißsimulation eröffnen metallverarbeitenden Betrieben bereits ab Losgröße 1 wirtschaftliche Möglichkeiten beim Schweißen. Gemeinsam mit den Kunden werden die jeweiligen Anforderungen an die Schweißtechnik analysiert. Im Anschluss daran folgt die Konzeption der individuellen Lösung. Dafür steht ein Baukasten aus standardisierten Komponenten zur Verfügung. Beginnend bei der Machbarkeitsstudie über Planung, Engineering, Fertigung und Inbetriebnahme wird der Verkauf von Schweißanlagen als Projekt abgewickelt. Seit 1975 sind in 45 verschiedenen Ländern mehr als 3.500 installierte Systeme bei über 2.000 Kunden im Einsatz. Auf einer Betriebsfläche von mehr als 11.000 Quadratmetern kümmern sich rund 150 Fronius Expertinnen und Experten um die schweißtechnischen Herausforderungen der Kunden.
(Quelle: Presseinformation der Fronius International GmbH)
Schlagworte
AuftragschweißenAuftragschweißsystemeAutomationCladding