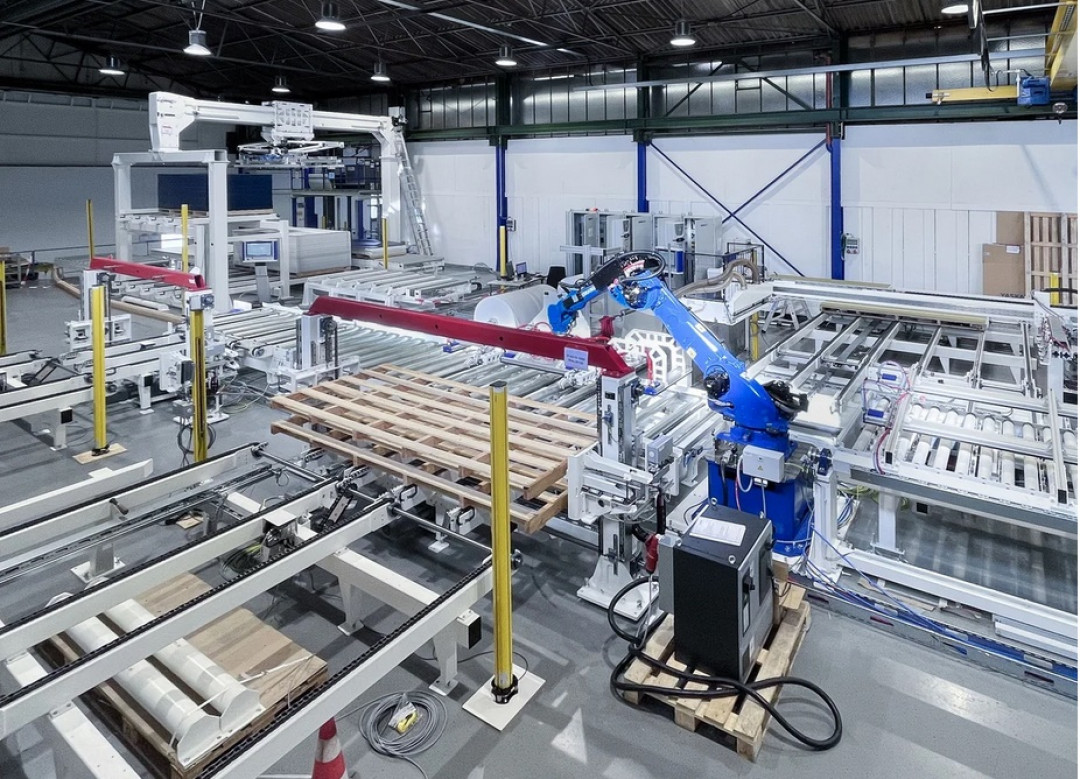
Digital Twin Optimizes Bürkle Systems
With an integrated tool chain, Robert Bürkle shows how to plan, build and commission complex systems more efficiently. Virtual commissioning helps save both valuable time and material. With a few clicks the robot picks up one of the exterior building panels from the coating system, turns it, and then transports it to the stacking unit. Then an error message pops up, indicating that the holding force has dropped too low. Normally the panel, which weighs around 80 kg, would then just fall to the floor unchecked. Today, Marian Michels, software engineer at Robert Bürkle, is able to analyze and eliminate such errors using a digital model: he and his colleagues can now rely on a digital twin for development and design. This digital twin, based on the CAD model of the system as a “single source of truth,” serves as the foundation for all subsequent process steps, as Jürgen Müller, head of mechanical design at Bürkle, explains.
Responding to new market challenges
Then, two opportunities brought virtual commissioning at Bürkle a step forward: a large customer project well-suited as a pilot project for virtual commissioning and the end-to-end tool chain from Siemens. The collaboration with Siemens proved successful and Bürkle was able to present its virtual commissioning at LIGNA, the most important trade fair for the wood industry, Müller continues: “The solution for the digital twin that Siemens presented to us was a very good match for our existing tool landscape.” The integrated tool chain – with the NX Mechatronics Concept Designer for mechatronic development, Simit for simulating the automation application, and PLCSim Advanced as a virtual image of the physical Simatic controller that will later be installed – works perfectly with the engineering in TIA Portal. This tool chain eliminates unnecessary system discontinuities and Bürkle can integrate new tools into its development processes more easily. Ultimately, every developer should be able to carry out virtual commissioning, Müller states: “We don’t want to have one expert but will use the digital twin in our day-to-day work.” The seamless cooperation with Siemens’ software tools also means that Bürkle does not have to enter data multiple times.
Two projects in parallel
As a software engineer, Marian Michels was responsible for first implementing the digital twin and had to deal with two projects at once: first, preparing the showcase for the trade fair and second, commissioning, both virtually and in real life, a complex system used to paint external building panels. “The crux of the customer project was that the panels have very special material properties. That’s why we used a robot with a specially designed holding fixture,” Michels explains. For the trade fair presentation, the virtual commissioning also had to be “polished” as a showcase of the company’s expertise. However, Michels was able to count on Siemens’ support for both projects: “We worked very well together, both during the project and afterwards – we didn’t have to explain much; our colleagues from the Siemens Application Center (APC) knew what was important to us and supported us wonderfully, especially with kinematization.”
Testing new technologies on the model
Next was the “acid test” for the digital twin, the virtual commissioning of the customer project. The task was to integrate the robot into the PLC program, including testing that the functionality and operating range were correct. Using the model, Michels was able to detect problems at an early stage and adapt the program accordingly. He benefited greatly from using the Simatic Robot Integrator (SRI), the new standardized interface SRCI (Standard Robot Command Interface) between the robot and the PLC. Thanks to SRI, the sequence can be programmed in the PLC quickly, easily and without extensive expertise in robotics. Using an international standard, different robot manufacturers can be integrated without having to change the programme.
Siemens and Yaskawa, the manufacturer of the robot used in this project, developed the interface together, making it easy to integrate the robot into both the system simulation and the real system. “The prerequisite for us to be able to implement the solution so quickly with a robot and combine virtual commissioning with robotics,” says Marian Michels.
Nevertheless, the project was under enormous time pressure. Application engineers at Siemens supported the development team at Bürkle. The results were then verified and tested on the model in advance. This advance testing allowed the team to concentrate on the technologically demanding processes involved in separating and stacking. Jürgen Müller is certain: “The schedule for the project was ambitious. The only way to keep the deadlines was with virtual commissioning.”
Savings in time, resources and materials
The effect of virtual commissioning has been significant, especially when it comes to integrating the robot into the stacking process, which includes complex movement sequences and a challenging space situation, not least because testing the system with real materials is more efficient, adds Marian Michels: “The plates are three meters long and over one meter wide. You can imagine the effort involved in reloading the system for a trial.” What’s more, Michels was able to supervise a large part of the commissioning virtually from the office. “A journey of 500 kilometers for commissioning also means that developers spend five hours in the car. With the digital twin, many things can be tested in advance and considerably less effort is required for real commissioning, meaning that working time can be spent more efficiently,” explains Müller.
(Source: YASKAWA Press Release)
Schlagworte
AutomationCoatingDigital TwinRobots