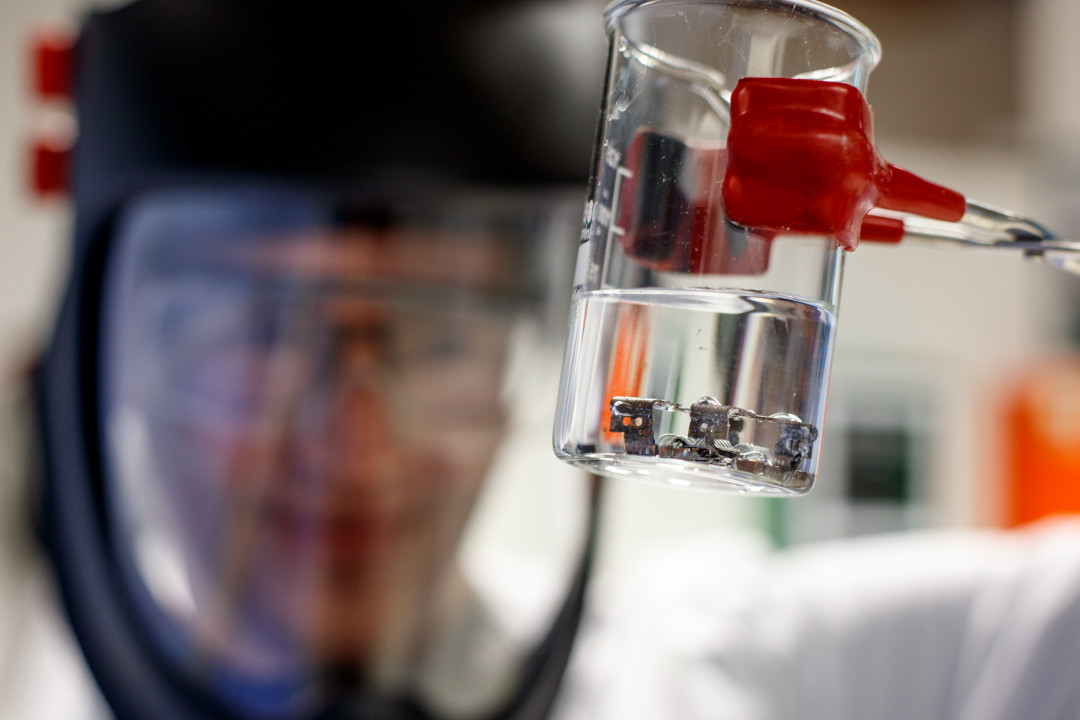
Focusing on carbon footprint for more sustainable welding
Fronius is taking a step in terms of sustainability and its use of resources by carrying out a certified life cycle assessment (LCA) for welding applications. Taking a holistic view of welding, from device manufacturing through customer use to end of life, yields insights into the key areas where the carbon footprint can be reduced.
Welding creates long-lasting bonds between metals. But how can the process in the application for the customer be made more sustainable – in terms of environmental impact? “For our customers, in addition to cost effectiveness, the carbon footprint of their production processes and components is becoming more and more important. That’s why we want to create added value for the users of our welding solutions, not only by further minimising the carbon footprint of our devices, but also by helping companies to reduce their consumption of resources during welding,” emphasizes Harald Scherleitner, Global Director of Sales and Marketing, Business Unit Perfect Welding, Fronius International.
Facts over emotions
The topic of sustainability is being discussed emotionally, but Fronius' approach to sustainability is based on the evidence. “We examined two typical, real-world applications that our customers use when welding steel and aluminium, and had the analysis certified by the renowned Fraunhofer Institute,” explains David Schönmayr, Team Leader for Product Sustainability at Fronius. Fronius experts, together with partner to4to (together for tomorrow), assessed the environmental effects of the welding variables, such as material, energy, gas, and emissions using standardised methods as part of a life cycle analysis. This comprehensive “cradle-to-grave” approach starts with the procurement of the raw materials, includes the production of the welding machines and transport, as well as years of use in industrial shifts, including wear parts, and also examines what happens when the welding machine has reached the end of its life cycle after a long service life.
CO2 footprint allocated to 1 meter of weld seam
Every component and every welding application is individual and influenced by many factors, such as the base material, the seam geometry and the welding parameters used. Fronius chose the scope of analysis that allows the results to be presented clearly so they’re easy to understand. “We allocate the CO2 portion of the relevant parameters to 1 meter of weld, because it instantly shows us where our starting point should be,” Schönmayr explains. “For the CO2 portion in use, we’ve based our calculations on the welds of robot series production with a typical duty cycle of eight years. We were referring to actual customer examples, an automotive supplier that uses the TPS 400i in its robot configuration for steel welding and a vehicle manufacturer that welds with the TPS 320i CMT.”
The key lever: resource-efficient use
In the life cycle of a Fronius TPS/i welding system, only around 0.5 % of the total CO2 equivalents comes down to the production, repair and disposal of the welding machine. The rest is split between the filler metal, the shielding gas and the consumed energy , which highlights the importance of making efficient use of these resources in particular. “The good news is that at Fronius we have already been working for many years to keep our material and energy consumption during welding as low as possible. [...] When it comes to efficiency, we believe that digitalization continues to present tremendous potential,” affirms Scherleitner.
Economic benefits = environmental benefits
Fronius wants to work with its customers to tackle areas where CO2 can be reduced. High welding quality plays a central role to ensure the materials are used as efficiently as possible or, in other words, by avoiding wasting resources with rejects or rework. Reproducible, high-quality welded joints protect both the bottom line and the environment, which is why taking a holistic view of production at component level (TCOP—total cost of production) can have a huge impact.
“Sustainability in joining is at the top of our agenda. Our experts in research and development follow the ‘Sustainability by Design’ approach. In this way, we create environmentally inspired innovations combined with our understanding of the challenges faced by our customers. However, the best way to save material, time, and money while gradually reducing the carbon footprint is by working together. Our LCA is only the starting point for a series of tips that we’ll be sharing with our customers,” summarizes Scherleitner.
The experts at Fronius can provide targeted support to help customers identify carbon savings potential in production, for example by using the OPT/i Gas digital gas controller or the WeldCube Premium monitoring and analysis tool.
(Source: Fronius Press Release)