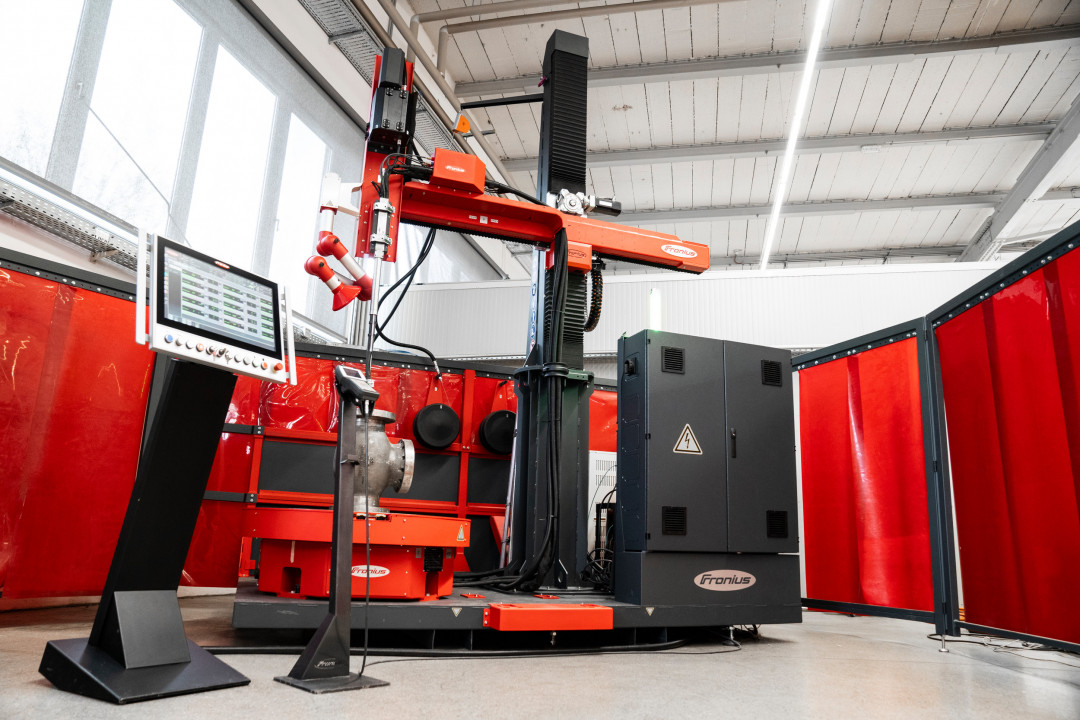
Fronius Welding Automation Cladding Solutions
From planning, engineering, manufacturing and commissioning to the maintenance and servicing of cladding systems, Fronius Welding Automation supports its customers with a global service and partner network. All systems are manufactured in accordance with international compliance standards to ensure safety and reliability. Technical commissioning by Fronius experts and the preliminary acceptance by buyers from the oil and gas industry take place at the production site in Steinhaus, Austria. The systems are then delivered, installed on site and finally accepted by international customers in the onshore and offshore sector. The comprehensive Fronius commissioning service includes expert training sessions and process optimizations at the start of production.
Realistic welding tests and feasibility studies
Every new cladding project begins with feasibility studies and welding tests. cladding is a highly complex process. In addition to the base material of the components, parameters such as amperage, wire speed, welding speed, filler metal, shielding gas, ambient temperature and humidity also play a decisive role. Even minor deviations can have unwanted effects on the welding result. This is why welding tests should be as realistic as possible – with components, filler metals and shielding gases that will also be used when the system goes into live operation. If possible, the tests should be performed under the same climatic conditions that exist at the intended place of use. If these conditions cannot be achieved, the welding parameters must be adapted and optimized in line with the production environment during commissioning.
Anton Leithenmair, Head of Fronius Welding Automation: “We need an open, trusting exchange of information from the outset to ensure that overlay welding systems are customized to customer requirements. Are there any specifications regarding the filler metal and shielding gas? What about the local climatic conditions? One particularly important factor is being able to conduct welding tests with original components rather than resorting to dummies. This is the only way our systems can deliver the desired welding results, even under the harsh conditions of continuous operation.”
Compact Cladding Cell (CCC)—Smart and user-friendly
With a footprint of approximately 6 m² (64.5 ft²), the Compact Cladding Cell mounted on a transportable platform is acompact solution for overlay welding. It was developed as a cost-effective inner cladding solution for valve components. The maximum bore depth and largest possible component diameter are 1 m (39 in), the highest component weight is 2,500 kg (5,511.56 lb). It is easy to use, with precise movement sequences and comprehensive data recording options. The ergonomic design includes a wire spool holder at a comfortable user height, welding torch quick-change system, and power sources on a rail. Plus, the CCC boasts innovative software functions, maximum process security and reliability in continuous operation. The HMI system controls offers a 21-inch touch display, real-time process visualization, multi-user management and more.
Endless Torch Rotation System (ETR)
The ETR system was developed for larger, more complex components. Its key feature is an endlessly rotating welding head. This makes it possible to weld components with different bores and bore angles up to an internal diameter of 1 m (39 in). The welding torch and the wire feeder rotate together around the bore axis. Components are centered automatically, which shortens set-up times and saves production costs. The electropneumatic collision detection system stops all axes of movement and protects the welding torch against damage if collision is imminent. Most recently, Fronius has enhanced its ETR system with the more flexible ETR Ultimate system. In addition to cladding tasks, this versatile system also makes it possible to join larger components with challenging geometries and difficult seams. As with the Compact Cladding Cell, both the ETR and ETR Ultimate systems come with the convenient 21-inch system controls with touch display, real-time process visualization and multi-user management as standard. The same applies to the welding torch quick-change system, which is designed to save time. If necessary, the welding torch and positioner move in sync in both the ETR and ETR Ultimate, while the SpeedClad 2.0 delivers maximum productivity for the overlay welding process here as well.
All parameters live and at a glance
The HMI-T21 system controls are ready for Industry 4.0 with a large, intuitive 21-inch touchscreen, multi-user accounts with individually assigned authorizations, process visualization in real time, on-the-fly parameter adjustments and innovative functions such as X-Ray View, Component Editor, Bore-to-Bore Advanced, actual value monitoring in real time and STEP file import. The X-Ray view provides a transparent outline of the component to give the operator an excellent overview. The Bore-to-Bore-Advanced function offers assistance when several offset transverse bores with non-90° angles or flanges with bores need to be surfaced. All relevant welding parameters are displayed live in the system-integrated actual value monitoring.
A service that meets every need
The welding professional creates components step by step in the Component Editor via the HMI-T21 touchscreen. The height and diameter are defined by entering the relevant dimensions and the various components appear in real time as 3D graphics on the screen. In addition to cylindrical shapes, flat and conical shapes are also possible. There are also options to model bores and extensions, such as flanges. The CNC technology now integrated at Fronius creates scope for even more component geometries than before, including intersection bores on conical components. The welding processes are programmed in the Program Editor. Operators select the individual sections of the components and define the welding sequence. All welding parameters are defined in the Weld Editor. The system offers a selection of jobs with fixed parameters that can be adjusted at any time – even on-the-fly – in the Weld Adjust menu. AVR (Actual Value Recording) records the actual values of the welding current, voltage, wire speed, gas quantity and welding position during the welding processes in table form.
Once the home position of the welding torch is calibrated, it moves independently to the starting point for each cladding application. Siegfried Wiesinger, cladding expert at Fronius, explains: “The remote control can be used to fine-tune a range of parameters even just before igniting the arc – for example, the AVC (Arc Voltage Control) function adjusts the starting point and distance of the welding torch to the component.“
Longitudinal and circumferential seam welding systems and robotic welding systems
Fronius Welding Automation not only offers cladding systems but also mechanized welding systems and robotic welding systems for all industries. These include longitudinal and circumferential seam welding systems, welding carriages and handling-to-welding robotic welding systems.
(Source: Fronius Welding Automation Press Release)
Schlagworte
CladdingRetrofittingRobotsWelding