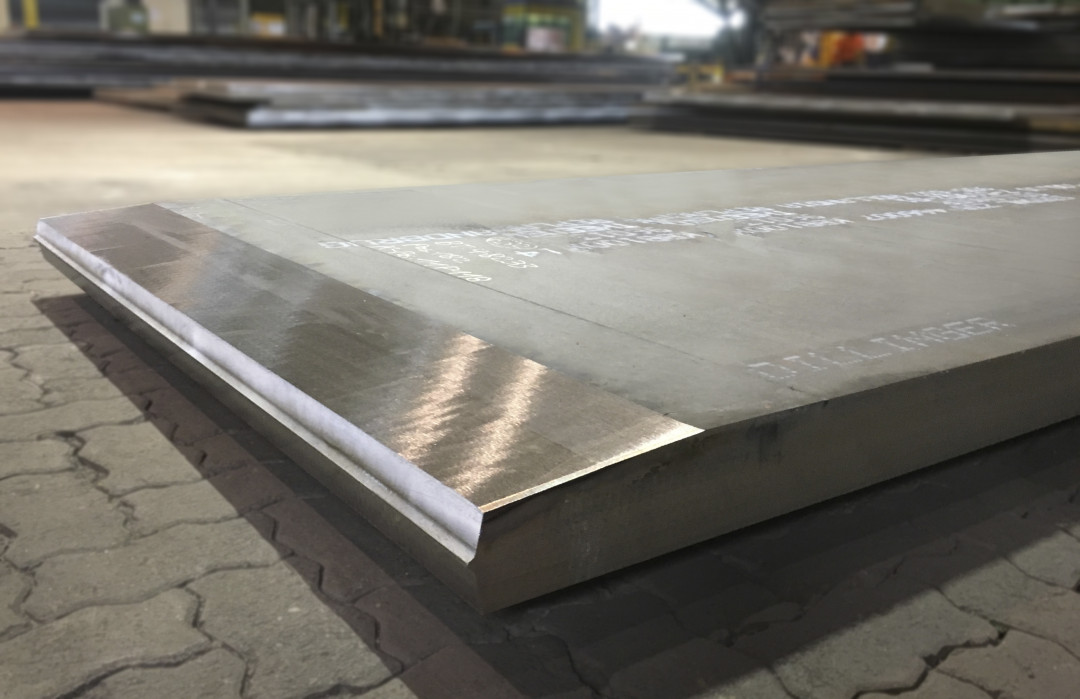
Klare Kante: Mehr Präzision und weniger Zeit bei der Schweißnahtvorbereitung
Mit über 350 Mitarbeitern ist Hollandia B.V. eine führende niederländische Stahlbaugruppe für Infrastrukturprojekte. Eines der jüngsten Projekte – die Thomassentunnelbrücke im Rotterdamer Hafen – ist mit 4.200 Tonnen verbautem Grobblech zugleich die größte Brücke in der Unternehmensgeschichte. Konstruktion, Engineering, Produktion, Montage und Installation am endgültigen Standort liegen ebenso wie das Projektmanagement in den Händen der Unternehmenstochter Hollandia Infra B.V. Gemeinsam mit der Dillinger Weiterverarbeitung entwickelte sie ein neues Design für die Schweißnahvorbereitung für den Stahlbau. Das ermöglichte die Lieferung von 188 Blechen – bis zu 120 Millimeter dick und 17 Meter lang – einbaufertig und just in time.
Die 1928 gegründete Hollandia B.V mit Hauptsitz in Krimpen aan den IJssel ist spezialisiert auf Entwicklung und Bau von komplexen Stahlkonstruktionen wie Brücken, Schleusen oder Hochwasserschutzanlagen. Dennoch zählen auch so berühmte Bauwerke wie das London Eye, das Wembley Stadion, der 162 Meter hohe Aussichtsturm British Airways i360 in Brighton oder die Renovierung der Wuppertaler Schwebebahn zu den Referenzen. Über 500 in den letzten Jahrzehnten gebaute Brücken in Nordwesteuropa – ein Viertel davon für den Eisenbahnverkehr – unterstreichen jedoch eindrucksvoll die ausgewiesene Expertise im Brückenbau. Seit rund zehn Jahren ist die Hollandia Infra mit 100 Mitarbeitern verantwortlich für diese Art von Projekten.
Mit dem Bau der Thomassentunnelbrücke ist sie an einem bedeutenden Infrastrukturprojekt im Rotterdamer Hafen beteiligt. Ein Konsortium aus fünf Bauunternehmen – darunter auch Hollandia Infra – wurde mit dem Unterbau der sogenannten Theemswegtrasse für den Eisenbahnverkehr beauftragt. Die Verlegung des Schienenverkehrs auf diese Trasse soll den zunehmenden Güterverkehr zwischen dem westlichen Hafengebiet und der Betuweroute nach Deutschland verbessern. Bisher führte die Strecke über die Calandbrücke bei Rozenburg – eine Hubbrücke für Bahn- und Straßenverkehr –, die derzeit regelmäßig für den Schiffsverkehr vom und zum Brittanniëhaven geöffnet wird. Künftig nutzt der Schienenverkehr die neue Trasse mit zwei Brücken. Eine davon ist die zweigleisige Thomassentunnelbrücke, die über den gleichnamigen Autotunnel führt.
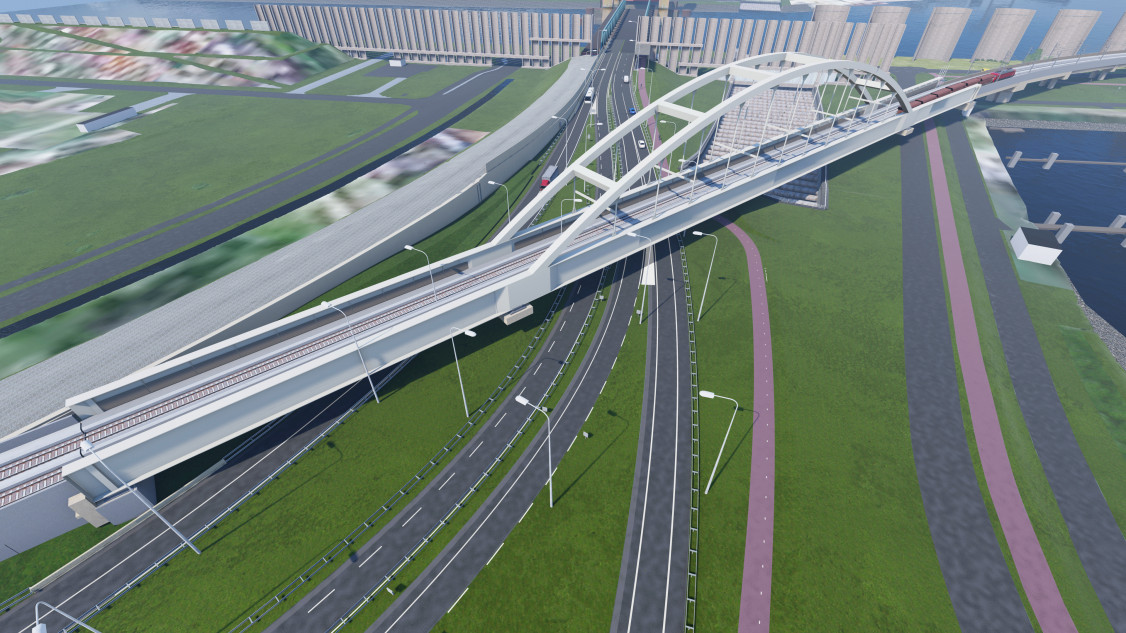
Herausfordernde Konstruktion
Das mit dem Bau dieser Stahlbogenbrücke für Hollandia verbundene Aufgabenspektrum war komplex: So reichte es von der Detailplanung über Materialbeschaffung, Produktion der Brückenkomponenten und abschnittsweise Montage der Bogenbrücke auf der unmittelbar an den finalen Standort angrenzenden Montagefläche bis hin zur Installation der kompletten Brücke am endgültigen Platz. Die eigentliche Herausforderung dabei war jedoch aus Sicht des verantwortlichen Projektmanagers bei Hollandia, Guus Olierook, die Ausarbeitung der Montagepläne: „Die Frage war, ‚Wie kommt diese große Brücke zum Montageplatz direkt neben dem Tunnel und von dort an ihren finalen Standort?‘“
Die Montage musste zudem inmitten eines dicht bebauten Industriegebietes mit einer Vielzahl an Unternehmen erfolgen – darunter auch petrochemische Betriebe mit entsprechend sensibler unterirdischer Kabel- und Rohrleitungsinfrastruktur. Hollandia entschied sich für einen maximalen Vorfertigungsgrad in der eigenen Werft, um so die Transporte zum Montageort zu minimieren. So unterteilte der Stahlbauer die Brückenkonstruktion in fünf Sektionen, die erst nach ihrem Transport am Montageplatz miteinander verbunden wurden. Die komplett zusammengebaute Brücke wird im Mai 2020 mit einem einzigen großen Transportvorgang mit SPMTs an ihrem endgültigen Platz installiert.
Bei der Dimensionierung der Sektionen galt es für den Stahlbauer auch die Größe seiner Lackiererei zu beachten: Kein Bauteil durfte länger als 60 Meter sein. Hollandia Infra konzipierte drei der fünf Sektionen als Kombinationen aus je einem Brückendeck- und Bogenabschnitt. In der Fertigung entstand zunächst jeweils das Bogenteil, unter dem anschließend der Bau des Brückendecks erfolgte. Zum Verschweißen der Komponenten hoben vier Mobilkrane den Bogenabschnitt auf das Deckelement. Danach wurde die fertig gebaute und lackierte Sektion zum Montageplatz transportiert. Zunächst baute Hollandia allerdings die westliche Vorbrücke, erst dann wurden die drei Kombisektionen aus Teilen vom Brückendeck und Bogen gefertigt. Den Abschluss des Produktionsprozesses markierte die Vorbrücke an der Ostseite.
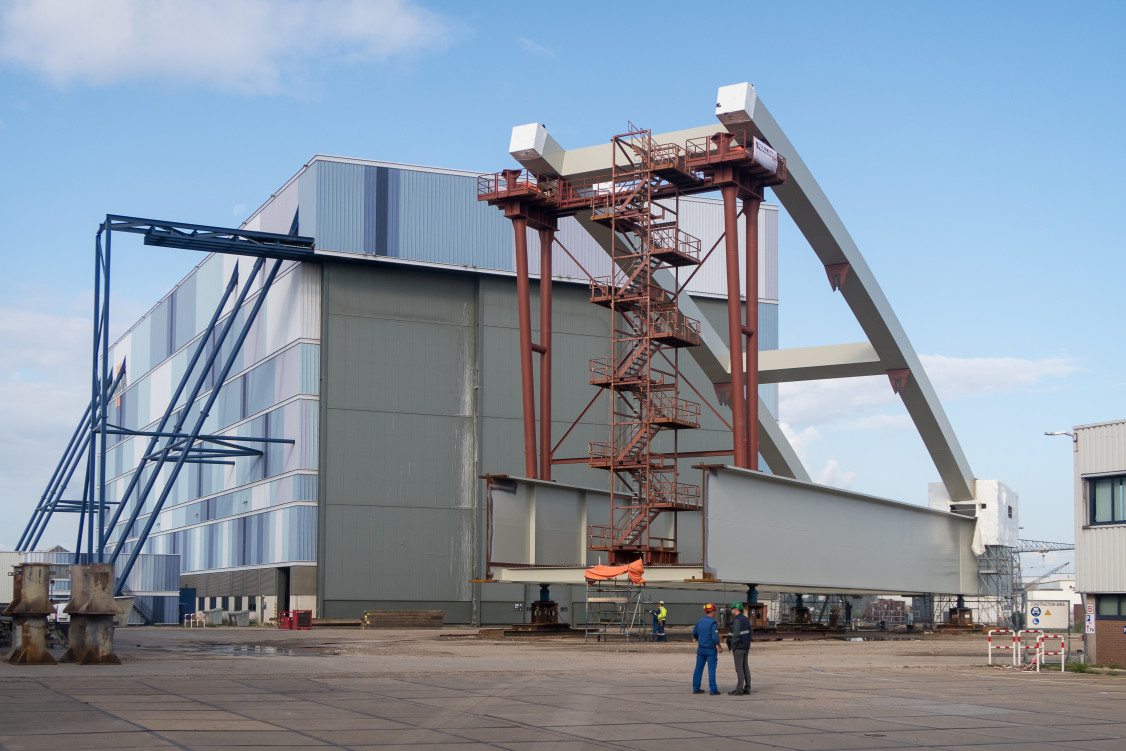
Parallel produzierte Hollandia 22 Hänger für die Thomassentunnelbrücke. Sie ist insgesamt 269 Meter lang – inklusive der 52 beziehungsweise 56 Meter langen Vorbrücken für Auf- und Abfahrt. Ihr schlichtes Design mit einem sehr schlanken Bogen fügt sich harmonisch in die Umgebung ein. Die Gesamthöhe von über 28 Metern ergibt sich aus dem 23 Meter hohen Bogen und dem Hauptgurt. Inklusive Bogen hat die 14 Meter breite Brücke eine Spannweite von 157 Metern. Entsprechend groß ist die Belastung der Stahlkonstruktion, die auf eine maximale Tragkraft von 12.750 Tonnen ausgelegt ist: Allein 4.200 Tonnen Grobblech wurden hier verarbeitet. Hinzu kommen 3.550 Tonnen für die Betondecke, 4.250 Tonnen an Ballast und Schienen sowie eine maximale, variable Last der Züge in Höhe von 850 Tonnen. Um dieses enorme Gewicht zu tragen und Vibrationen weitestgehend zu vermeiden, war eine sehr starke und steife Stahlkonstruktion erforderlich. Deshalb wurden vier sogenannte Kreuzgurte zwischen den Flanken des 5,5 Meter hohen und 1,6 Meter breiten Hauptträgers zur Versteifung eingeschweißt. Sie leiten die vertikale Krafteinwirkung durch den Gurt direkt in den Beton.
Kombination komplexer Bearbeitungsverfahren
Schon seit vielen Jahrzehnten vertraut Hollandia auf Qualitätsstahl vom Grobblechhersteller Dillinger und orderte dort für dieses Projekt 4.200 Tonnen Bleche der Stahlgüte S355 in den Varianten S355J2+N, S355K2+N und S355NL. „Es gibt nicht viele Stahlhersteller in Europa, die diese hohe Stahlqualität in solchen Dicken, Längen und Stückgewichten liefern können“, begründet Guus Olierook diese Wahl. Erstmals wurden 2.500 Tonnen davon direkt ab Werk durch die Dillinger Weiterverarbeitung als brenngeschnittene und kantenbearbeitete Bauteile geliefert. Ausschlaggebend für diesen Auftrag war eine für den Stahlbau innovative Technologie zur Schweißnahtvorbereitung. Gefragt war eine maschinell gefertigte Kombination aus einer sehr flachen Verjüngung und einer Tulpenformkante für sehr dicke und sehr lange Bleche. Für den Bau der Thomassentunnelbrücke versprach sich Hollandia von diesem Verfahren der Dillinger Weiterverarbeitung einen maßgeblichen Beitrag zur wirtschaftlichen Fertigung und besseren Einhaltung enger Toleranzen und Zeitschienen.
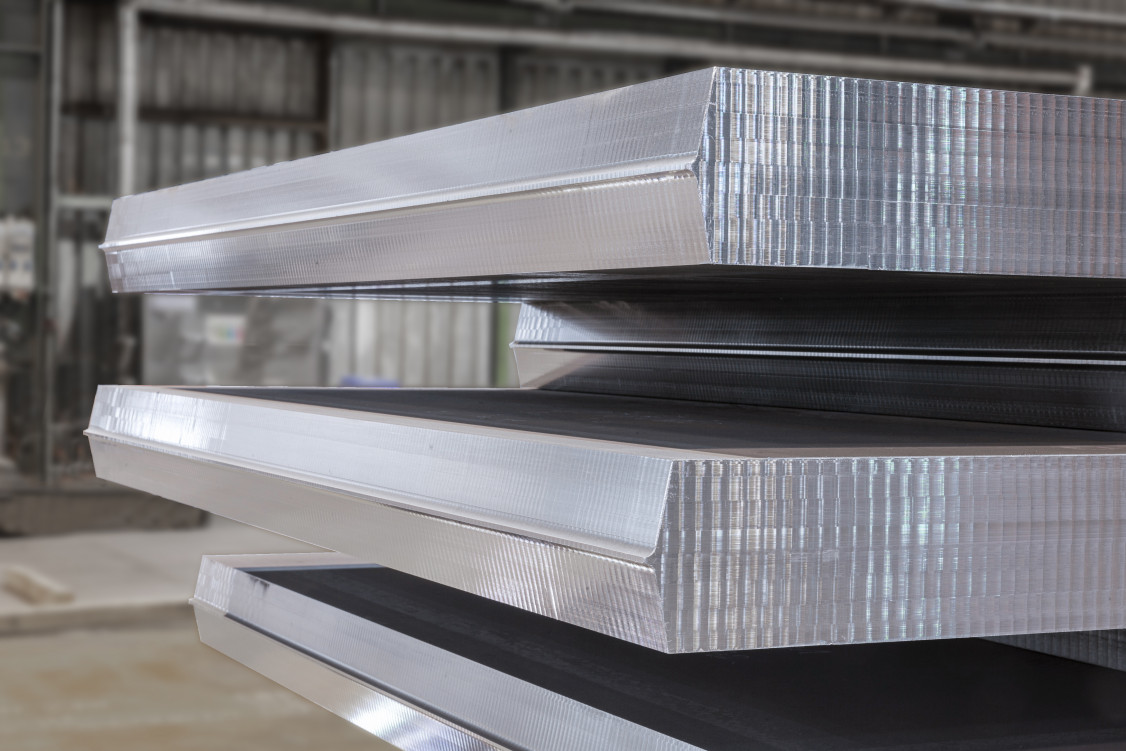
Normalerweise werden die Konturen von Gurtblechen mit notwendiger Nahtvorbereitung brenngeschnitten. Neben zusätzlichem Handlings- und Prüfaufwand sind dabei jedes Mal auch kleine Abweichungen bei den Abmessungen unvermeidbar: Je nach Dicke und Länge der Bauteile können Toleranzen von drei bis fünf Millimetern auftreten. Die Spezifikation der Rotterdamer Hafenbehörde duldet jedoch nur eine maximale Toleranz von ± 1 mm.
Die Dillinger Weiterverarbeitung bietet neben direktem Zugriff auf die Rohbleche vom Walzwerk beide Prozesse aus einer Hand an, sodass kein Zwischentransport anfällt. Durch die Vorfertigung von Bauteilen für die stark automatisierten Prozesse der Offshore-Wind- und Öl-/Gas-Industrie bringt sie zudem große Erfahrung in komplexen Brennzuschnitten und hochpräziser Schweißnahtvorbereitungen mit.
Im Brückenbau gelten jedoch bei den Projekten andere Parameter. Patrick Regnery, Leiter der Dillinger Weiterverarbeitung, sieht angesichts zunehmender Automatisierung in der Schweißtechnik steigende Anforderungen für eine integrierte, höchst projektspezifische Bauteil- und Schweißnahtvorbearbeitung.
Deshalb begann sein Betrieb schon frühzeitig mit der Entwicklung eines entsprechenden Verfahrens und investierte dafür auch in neue Maschinentechnologie. Die auf dieser Basis angefertigten Probebleche überzeugten die Techniker von Hollandia im Kontext der aktuellen Anfrage bei einem Besuch in Dillingen spontan: „Wir haben sofort gesehen, dass diese Bearbeitung eine perfekte Ergänzung für die Thomassentunnelbrücke wäre“, so Guus Olierook.
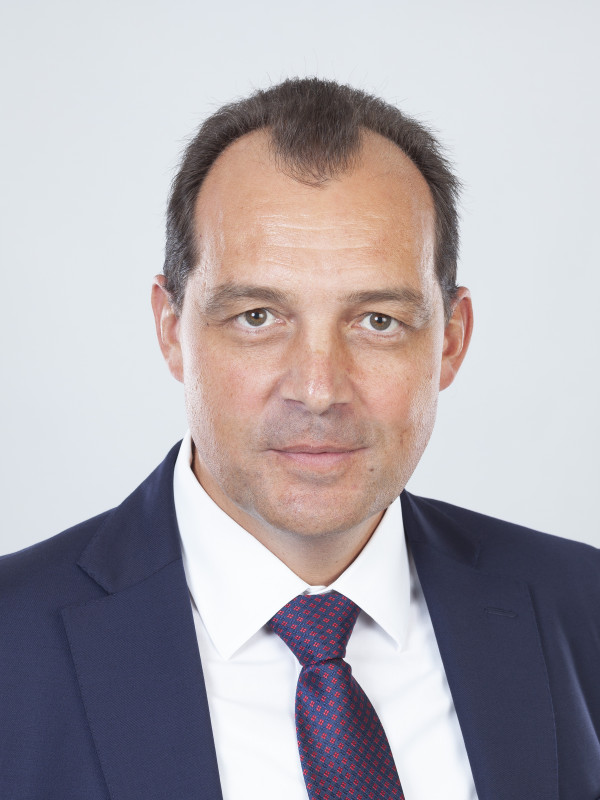
Enger Schulterschluss zwischen Stahlbau und Weiterbearbeitung
Im intensiven Austausch mit Hollandia wurden die Detailwünsche der Designer und die technische Machbarkeit bei der Dillinger Weiterverarbeitung diskutiert – mit dem Ergebnis, dass dieses Verfahren zur Nahtvorbereitung für den gesamten Hauptträger eingesetzt werden konnte. Zoltan Szabo, Leiter des niederländischen Vertriebsbüros von Dillinger, war in diesen Diskussionsprozess eng eingebunden. Er erinnert sich: „Im Vergleich zu den Anforderungen bei der Monopile-Herstellung für Offshore-Anwendungen war die von Hollandia gewünschte Nahtvorbereitung eine neue Herausforderung. Die Dillinger Weiterverarbeitung entwickelte deshalb für diese Anwendung eine individuelle Nahtgeometrie, die die spezifischen Anforderungen erfüllte.“
Projektleiter Olierook erklärt diese Vorgabe beispielhaft mit der Notwendigkeit zur exakten Positionierung eines 120 Millimeter dicken Blechs in über fünf Metern Höhe auf dem Hauptträger. „Da muss sichergestellt sein, dass alle gelieferten Teile exakt die richtige Größe und Bearbeitung haben.“ Er ergänzt: „Vor diesem Hintergrund war die Vorfertigung der Dillinger Weiterverarbeitung für unser Montagesystem perfekt.“ Die Anlage in Dillingen ist auf schnellen Durchlauf ausgelegt, sodass ein Blech ohne zwischenzeitliches Drehen an allen vier Kanten gleichzeitig mit unterschiedlicher Formgebung und in den gewünschten Abmessungen bearbeitet werden kann. So konnte Hollandia bei der Produktion der 20 Abschnitte des ca. 27 Meter langen Hauptgurts für die Gesamtträgerlänge von 2 x 269 Metern erstmals alle Bauteile – von einem Anbieter in einer Maschine rundum bearbeitet sowie exakt auf Länge und Breite geschnitten – direkt einbauen.
„Zu Beginn haben wir noch alles nachgemessen“, sagt Guus Olierook. „Aber wir haben schnell gemerkt, dass wir uns auf das Qualitätssystem der Dillinger Weiterverarbeitung verlassen konnten.“ Eine Nachbearbeitung der gelieferten Bauteile entfiel und dank der innovativen Schweißnahtvorbereitung nahm der Schweißprozess deutlich weniger Zeit ein, als bei den bisher im Stahlbau üblichen Nahtgeometrien. Obendrein gab es weder zeitaufwendige Zwischentransporte noch toleranzkritische Wechsel zwischen den üblicherweise unterschiedlichen Bearbeitungsbetrieben in der Lieferkette. „Mit der herkömmlichen Lösung hätten wir sicherlich vier bis sechs Wochen Zeit verloren“, schätzt Guus Olierook.
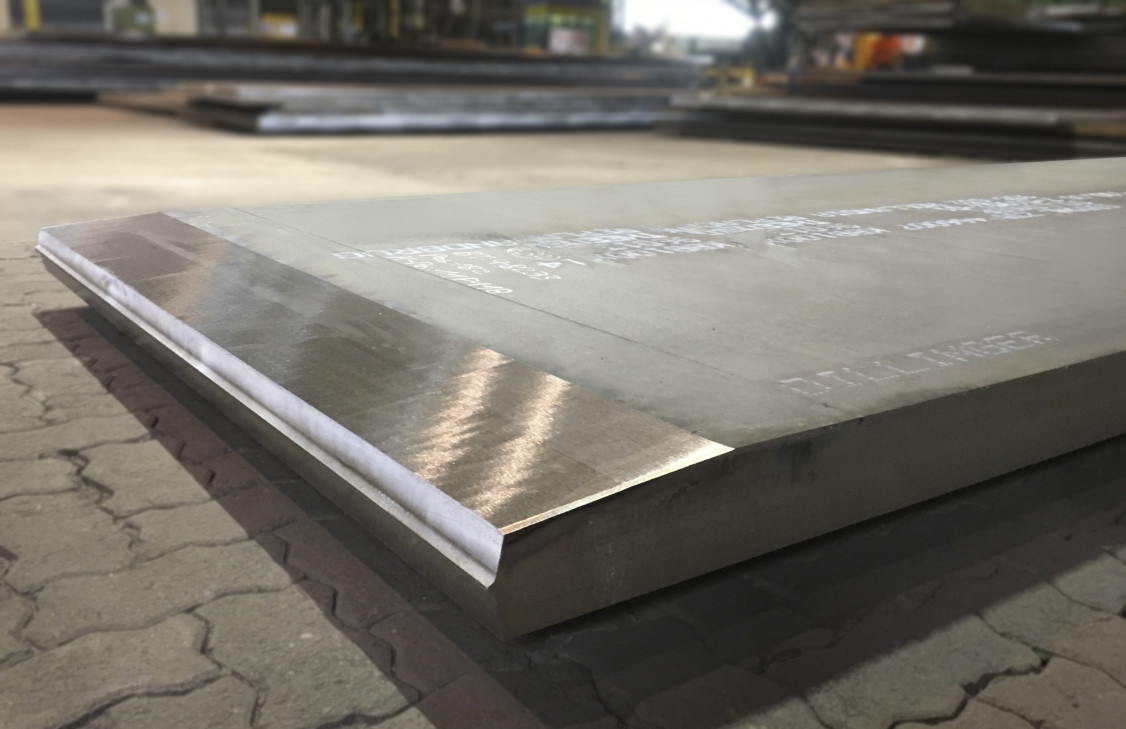
Durch die Beauftragung der Dillinger Weiterverarbeitung profitierte Hollandia aber noch von einem weiteren Vorteil: Anders als bei Grobblechwalzwerken üblich, ist man dort in der Lage die Bauteilfertigung an die individuellen Kundenbedürfnisse anzupassen. So sicherte Dillinger nicht nur die termingerechte Lieferung der richtigen Bauteile zur richtigen Zeit, sondern erschloss Hollandia auch mehr Flexibilität in der Produktion. Dazu trug auch die Möglichkeit bei, bis zuletzt Anpassungen in der laufenden Auftragsabwicklung zu berücksichtigen. Durch Übernahme der Zwischenlagerung konnte die Lieferung bei leichten Verspätungen verschoben werden, bei vorzeitigem Bedarf waren die fertig bearbeiteten Bleche ebenfalls just in time verfügbar. So konnte Hollandia binnen neun Monaten alle Komponenten für die Thomassentunnelbrücke produzieren und zum Montageplatz transportieren. Nach dem letzten Lift – dem Mittelteil der Brücke Anfang Dezember 2019 – werden die Aufhängungen bis Anfang 2020 installiert. Im Mai erfolgt dann termingerecht der Transport der gesamten Stahlkonstruktion auf ihren endgültigen Standplatz.
Für Guus Olierook ist der außerordentlich gute Projektverlauf auch der offenen Kommunikation mit der Dillinger Weiterverarbeitung zu verdanken. „Dieser Austausch auf Augenhöhe ist wichtig, um den Prozess des anderen zu verstehen.“ Deshalb wurde die Dillinger Weiterverarbeitung mit ihrer großen Expertise und Erfahrung in der Schweiß- und Umformtechnik bereits in der Ausschreibungsphase als technischer Entwicklungspartner miteingebunden. Mit entsprechendem Erfolg: „In einer gemeinsamen Anstrengung haben wir diese innovative Lösung gefunden“, würdigt der Hollandia-Projektleiter die konstruktive Zusammenarbeit mit den Bearbeitungsexperten aus Dillingen. Als erfahrener Entwicklungs- und Realisierungspartner ermöglichte die Dillinger Weiterverarbeitung die technische Umsetzung der gewünschten Stahlverarbeitung „im lebenden Projekt“, wie Patrick Regnery nicht ohne Stolz sagt. Herausgekommen ist nicht nur die von Hollandia geforderte Spitzenleistung in Stahl, sondern auch eine vertrauensvolle Partnerschaft als Basis für ein weiteres gemeinsames Brückenbauprojekt.
Schlagworte
BrückenbauSchweißnahtvorbereitungStahl