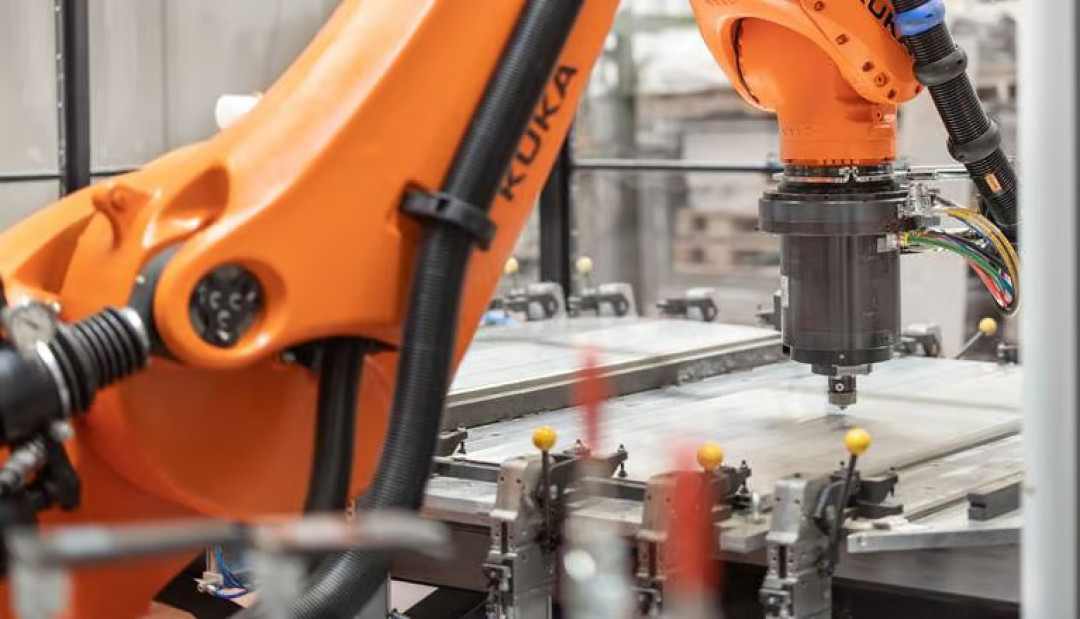
KUKA Welding Technologies for E-Mobility
The FSW cells (FSW: Friction Stir Welding) with various technologies and KUKA KR FORTEC robots are integrated into electric vehicle production lines: the robots in the cells weld battery trays together and join cooling plates to the battery trays in a second step. KUKA is also responsible for the entire friction stir welding process.
This is an important task as battery trays play a crucial role in electric vehicles. They must be leak-proof and resilient, support the correct temperature of the batteries and help to prevent the vehicle occupants from being endangered by the battery in the event of an accident. 3D welding is particularly challenging, for which robot-based FSW technology is suitable. This also requires complex clamping technology, KUKA was able to contribute engineering expertise for. A tool changer and a cleaning station for the FSW tools are also used for fully automated operation.
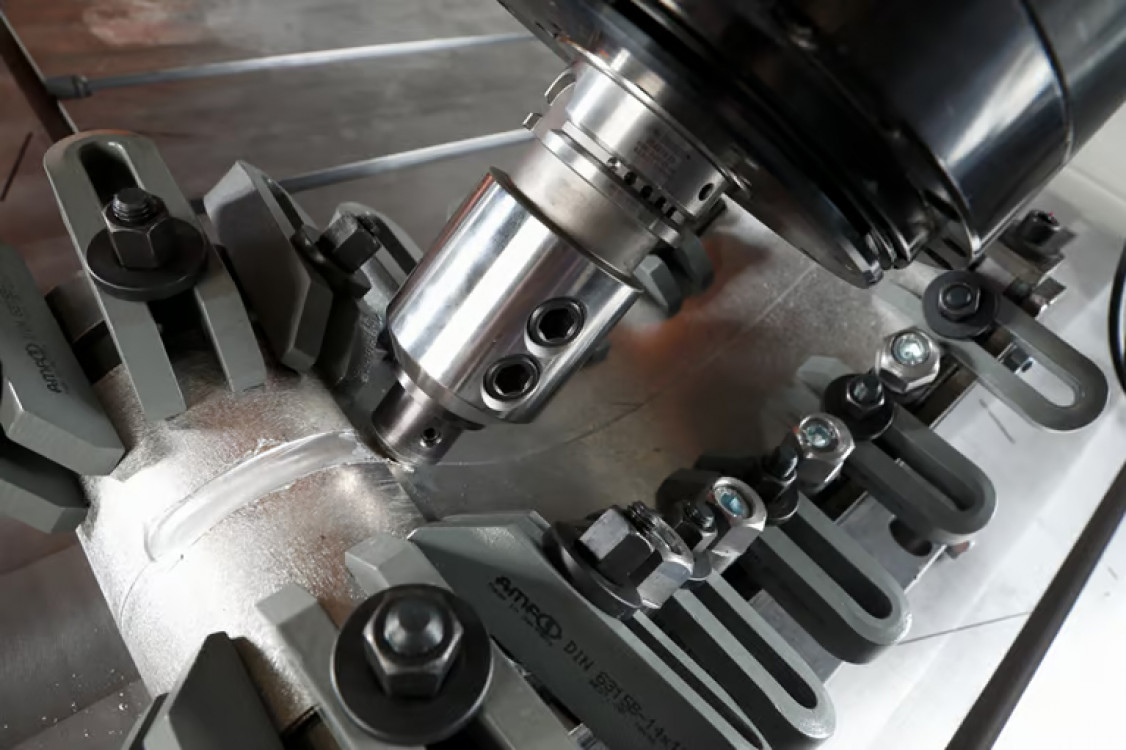
FSW: Higher quality, more efficient and more sustainable welding
In friction stir welding, a rotating, pin-like tool is guided between the component interfaces. The frictional heat causes the material to plasticize and the parts are joined. Even difficult-to-weld or dissimilar materials such as aluminium can be welded with magnesium, copper or steel. This process consumes less energy and material and does not require shielding gas or flux cored wire as in conventional processes.
FSW welding is used in a wide variety of industries that have special requirements for welding seams, e. g. battery containers, high-speed train sidewalls or tank structures of rockets. In addition to the growth market of e-mobility, the technology is also used in the aviation and electrical industries.
KUKA is working with research partners to further develop the technology: In order to monitor the quality of the weld seams during the process and thus reduce the time and costs of subsequent inspection, KUKA is working with partners in the AI production network of the University of Augsburg on an AI-based process monitoring system.
(Source: KUKA Press Release)
Schlagworte
E-MobilityFriction Stir WeldingRobotsWelding