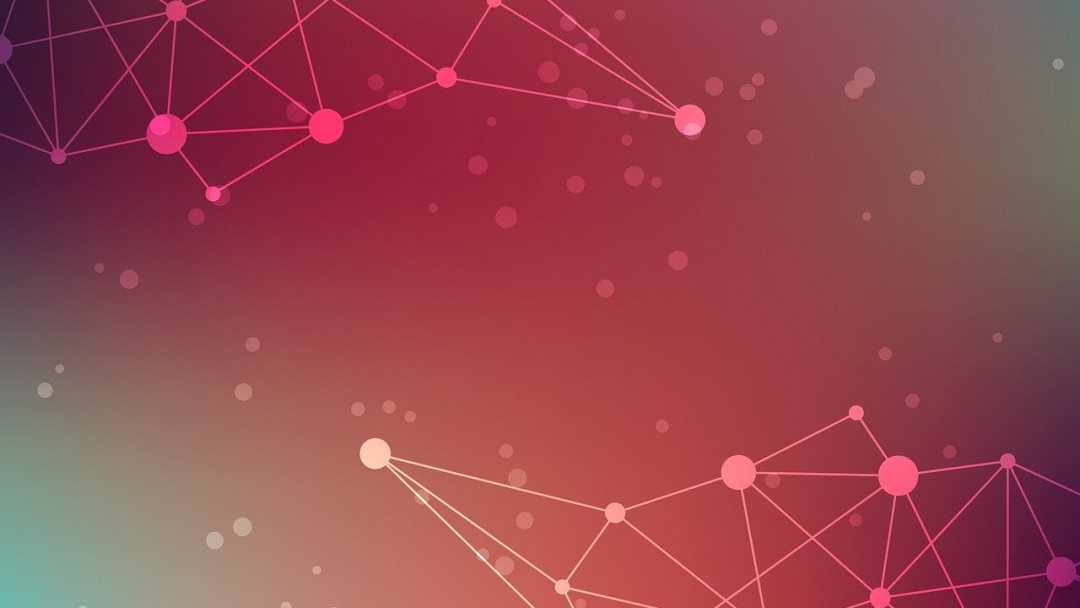
Multi-Material Joints of Carbon Fibre Composites and Aluminium for Lightweight Applications
The 26th Climate Change Conference has highlighted the urgent need to reduce global CO2-emissions. The transport sector, which is responsible for over 20 % of global emissions, has focused on fleet electrification as the primary strategy to achieve climate neutrality. However, the main challenges are the current weight of components, the cost of systems to ensure efficiency and long-term sustainability. The industry has recognized the need for transformative technologies and advanced production methods to develop lighter, more efficient and cost-effective solutions, essential for supporting this transition and achieving climate targets.
Electrical and electronic equipment in transport sectors, such as aeronautics and automotive, must efficiently dissipate accumulated heat to protect sensitive components and ensure longevity. Localized heat accumulation can affect performance and reduce service life. Consequently, components that require effective heat dissipation, such as electric motor housings, power electronics housings and battery cases, are typically made from conventionally manufactured steel or aluminium alloys.
In recent years, Carbon Fibre Composites (CFCs) have been increasingly replacing metals in products that require lightweight features with their outstanding mechanical strength, such as aircraft or high-performance vehicles. However, the use of CFCs has been limited to applications that require efficient heat dissipation due to their poor thermal conductivity. To address these limitations, a novel approach using a combination of aluminium and CFCs has been proposed to exploit the distinct advantages of both materials, referred to as metal-polymer multi-materials. These multi-materials aim to achieve lightweight structures with improved mechanical properties and good thermal management.
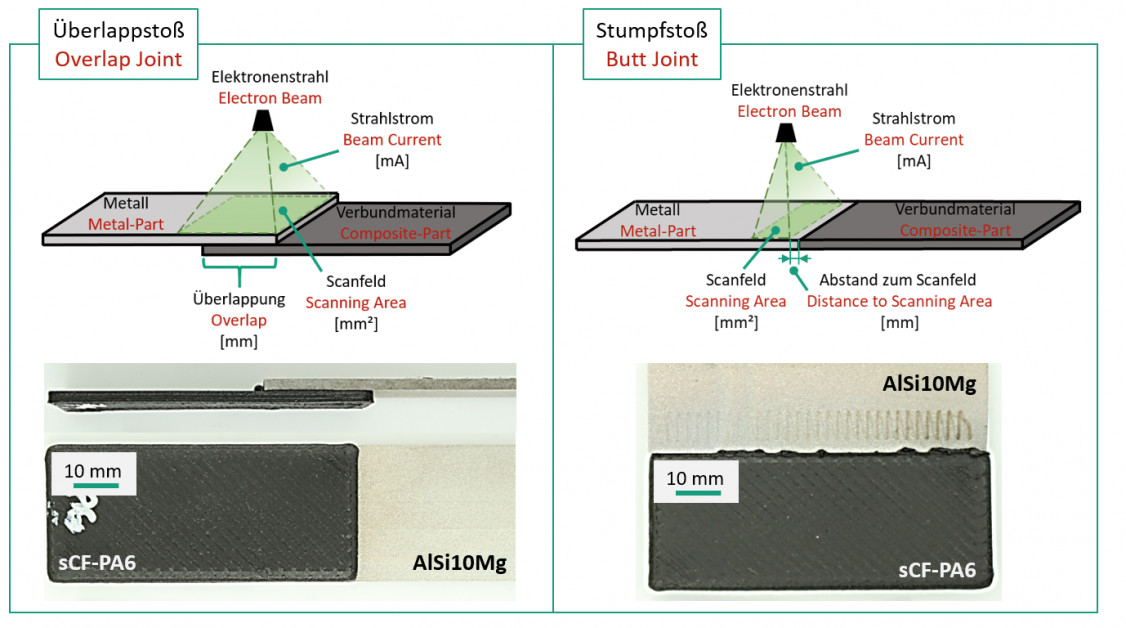
Electron Beam Bonding
The production of new metal-polymer multi-materials is a major challenge due to the difficulty of achieving a strong bond between dissimilar materials, resulting from their different physical and chemical properties. However, Fraunhofer IPK has developed a novel method Electron Beam Bonding to overcome this challenge using the innovative thermal joining technologies of the electron beam process. In this method, the thermal energy is applied uniformly to a defined scanning area on the surface of the metal part using electron beams to achieve the heat input required for the composite melting temperature. Heat transfer through direct contact between the composite material and the metal part causes localized melting of the composite, resulting in adhesion to the metal part. Electron Beam Bonding offers several advantages, including the ability to join in a vacuum chamber, which prevents the formation of oxide layers on metal parts or gas bubbles in composite parts. Furthermore, due to the flexibility of the electron beam movement and the ability to adjust the electron beam deflection make Electron Beam Bonding suitable for all geometric shapes and joint types, such as lap, butt, corner and T-joints.
The novel method has been developed within the project MULTHEM for joining additively manufactured aluminium and carbon fibre reinforced components to produce metal-polymer multi-materials. The project MULTHEM - Multi Material Additive Manufacturing for Lightweight and Thermal Management has received funding from the European Union’s Horizon Europe Research & Innovation Programme 2021-2027 under grant agreement number 101091495. In addition to research and technology organizations, end-user industrial companies are also involved in the project to apply this innovative approach to their products, such as radioaltimeter housings for aircrafts (Thales), electric motor housings for drones (AirElectric) and battery cases for electric bicycles (ÉireComposites). This innovative approach enables the creation of lightweight battery and motor housing structures with improved mechanical properties and cooling features.
(Source: Fraunhofer-Institute of Production Systems and Design Engineering IPK, Berlin)
Schlagworte
Climate ChangeElectron Beam WeldingTransformation