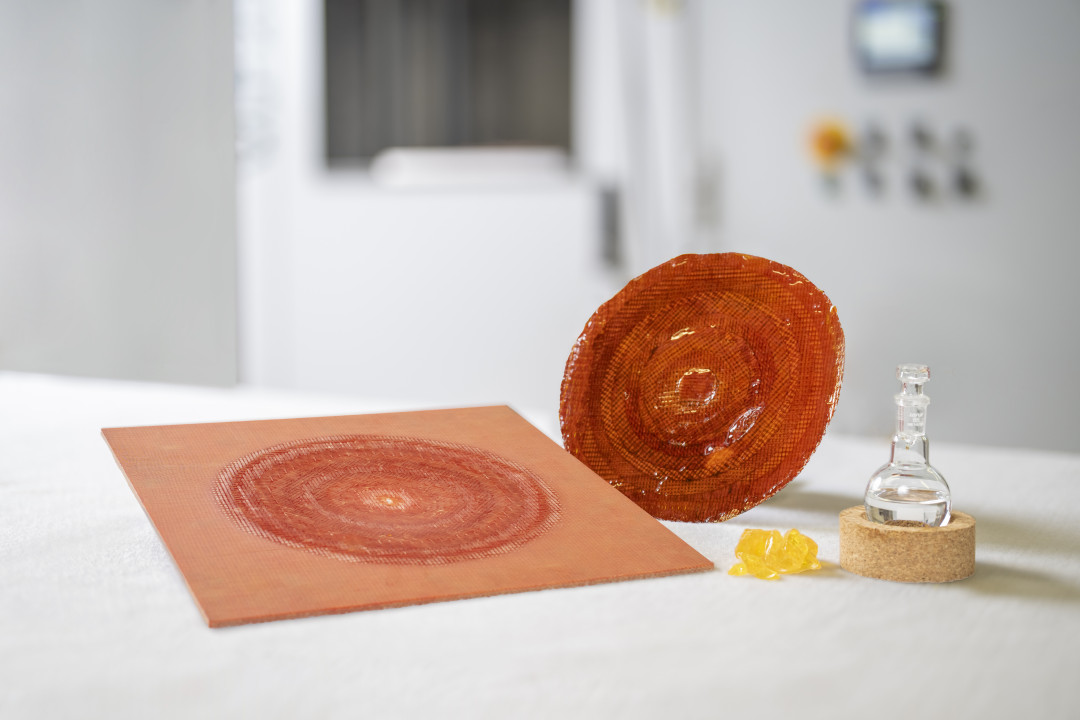
Polymer Patch Made from Dynamic Polymer Networks
Researchers at the Fraunhofer Institute for Manufacturing Technology and Advanced Materials IFAM have developed a new polymer patch that can significantly accelerate and simplify previously laborious, expensive, and time-consuming repair processes on damaged lightweight aircraft components. The thermoformable, recyclable repair patch is pressed onto the damaged area and fully sets in just 30 minutes. The innovative fiber-reinforced plastic is so versatile that it can be used in a wide range of different industries, from aviation to orthopedics.
Repairing lightweight fiber composite components like those used in aircraft wings, fuselage sections, tail surfaces and doors is a time-consuming and costly process with multiple work steps. The damaged area is typically repaired using a painstaking wet lamination process or by applying fiber-reinforced polymers (FRPs) or aluminum structures known as doublers to the surface. However, these methods involve a long curing time and require additional adhesives.
Researchers from Fraunhofer IFAM have now developed a repair patch made from dynamic polymer networks – also known as vitrimers – that shortens the previously lengthy and laborious repair process to just 30 minutes. What is really special about the innovative material – which is based on benzoxazines, a new class of thermosetting material known as a thermo-set – is that the polymerized plastic does not melt or otherwise behave like a traditional resin system used in wet lamination. The polymer’s dynamic networking processes make it possible to heat the material locally. The fully cured patch adapts to the repair site in its heated state. At room temperature, the polymer has thermosetting properties, so the patch is not sticky and is stable when stored. This saves energy, as the patch can be stored at room temperature and does not require refrigeration, which reduces storage costs.
The patch is applied to the lightweight component requiring repair using pressure and thermally induced exchange reactions. It enables rapid repairs, fully setting within 30 minutes. There is no need to work with reactive hazardous materials, as is necessary with traditional resin systems. The vitrimeric properties make it possible to remove the patch as and when needed, without leaving any residue behind. “Our adhesive-free, storage-stable fiber-reinforced patch enables direct repairs to damaged composite materials and hybrid structures. Because the polymer is a vitrimer by nature, the patch behaves like a conventional thermoset composite material during storage, but it also bonds cleanly and easily when simply heated, without any need for additional adhesives,” explains Dr. Katharina Koschek, head of the Adhesive Bonding and Polymeric Materials section at Fraunhofer IFAM in Bremen.
Use in aviation: resource-conserving and energy-efficient repairs to lightweight structures extend service life
The innovative material features high mechanical strength and thermostability, making it especially suitable for mobility applications such as automotive and railway vehicle engineering and in aviation. It can be deformed and has self-healing properties. Once it reaches the end of its service life, it can be recycled, since the polymer network can be dissolved and both the fibers and the polymer system can be reused. “Conventional thermosets cannot be deformed afterward, and they’re not recyclable. Our benzoxazine-based vitrimers, by contrast, exhibit all these properties. The versatile material covers many aspects of the sustainable use of polymers with an eye to the circular economy,” Koschek points out. “Through repair and reuse, it extends the service life of lightweight structures and helps to reduce the new raw materials consumed.” Another advantage is that it can be combined with other materials, making it also suitable for integration into structures made of metals such as steel.
Use in orthopedics: customized reshaping and adjustment of individual patient prostheses and orthoses
The versatility of the benzoxazine-based vitrimers opens up potential applications in various industries, even beyond the mobility sector. In orthopedics, for example, the thermoformable material could be used to realize individually adjustable orthoses and prostheses in the future. At present, custom fabrication of lightweight devices like these is a highly laborious process, as conventional fiber composite materials do not permit much adjustment once the resin cures. “Prostheses are custom-made for individual patients. But they don’t always fit. The slightest imperfection in the fit or physiological change can mean that the prosthesis or orthosis causes the patient pain or discomfort, interfering with their treatment. Previously, that meant that a new prosthesis would have to be made and due to the demand and amount of detailed manual work involved in orthopedics, that can take up to several months,” Koschek explains.
Using thermoformable materials could eliminate the need to remake these kinds of medical aids. In the CFKadapt project, researchers from Fraunhofer IFAM joined forces with orthopedics and prosthetics firm REHA-OT Lüneburg Melchior und Fittkau , E.F.M. and the Leibniz Institute of Polymer Research Dresden (IPF) to develop a novel fiber-reinforced polymers that is based on dynamic polymer networks and can be adjusted in various ways. The key difference between the new material and commercial matrix systems for orthopedic devices made from fiber composites is the possibility of readjusting and modeling the new material to the appropriate pressure or support points, which permits dynamic adjustment to the patient and their changing needs over the course of treatment. The trick is that the new polymer fiber composite mix can be heated locally and individually adjusted. “The benefits lie in the great design and configuration freedom and significant reduction of waste during production, along with longer service life for these devices, as they can be adjusted on an ongoing basis during treatment. For patients, the main factor is that they can get a custom-fitted orthopedic device as soon as possible,” Koschek says. Standardized production of components with subsequent individual adjustment also has the potential to yield cost benefits and improve the efficiency of the production process.
(Source: Fraunhofer IFAM Press Release)
Schlagworte
AircraftsComponentsLightweight ConstructionPolymers