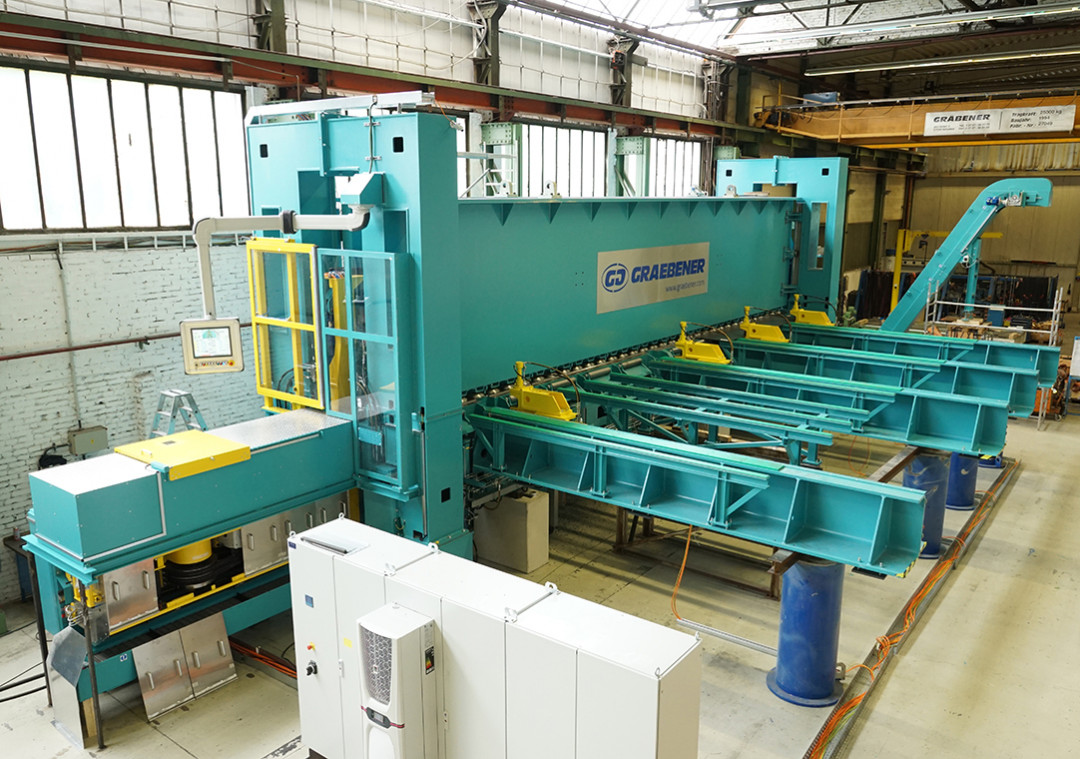
Time Savings Achieved through Simultaneous Milling in the Production of Offshore Platforms
A total of nine shipyards in the United States, Europe and China are already working with various plate edge milling machines from the German custom machine builder Graebener. For the first time, the company is now supplying its milling technology together with Ingenieurtechnik und Maschinenbau GmbH (IMG) to Southeast Asia a panel line that will be located in at the Malaysia Marine & Heavy Engineering Sdn. Bhd. shipyard (MMHE), which is currently setting up a new line for the production of offshore platforms. With the new 2-side plate edge milling machine from Graebener, two plates can be processed simultaneously, resulting in a doubled milling output.
MMHE operates the largest shipyard in Southeast Asia, is a globally renowned supplier for shipbuilding and is also known for its expertise in offshore production, conversions and repairs of ships and dry docks. The portfolio also includes the production of converter platforms for offshore wind turbines. Converter platforms provide the connection between an offshore wind turbine and the national power grid. They enable the generated electricity to be transported and fed into the grid by converting AC power into DC power, synchronizing the grid frequency and voltage and controlling and monitoring the power transmission.
During the production of these platforms, large, thick-walled plates are welded together to form large sections. At this point, the Graebener technology becomes important. Plate edge milling machines are generally used whenever large plates are being welded together. By means of the milling machines, the edges of the plates are prepared for the subsequent production step – welding. This milling process is also known as weld seam preparation.
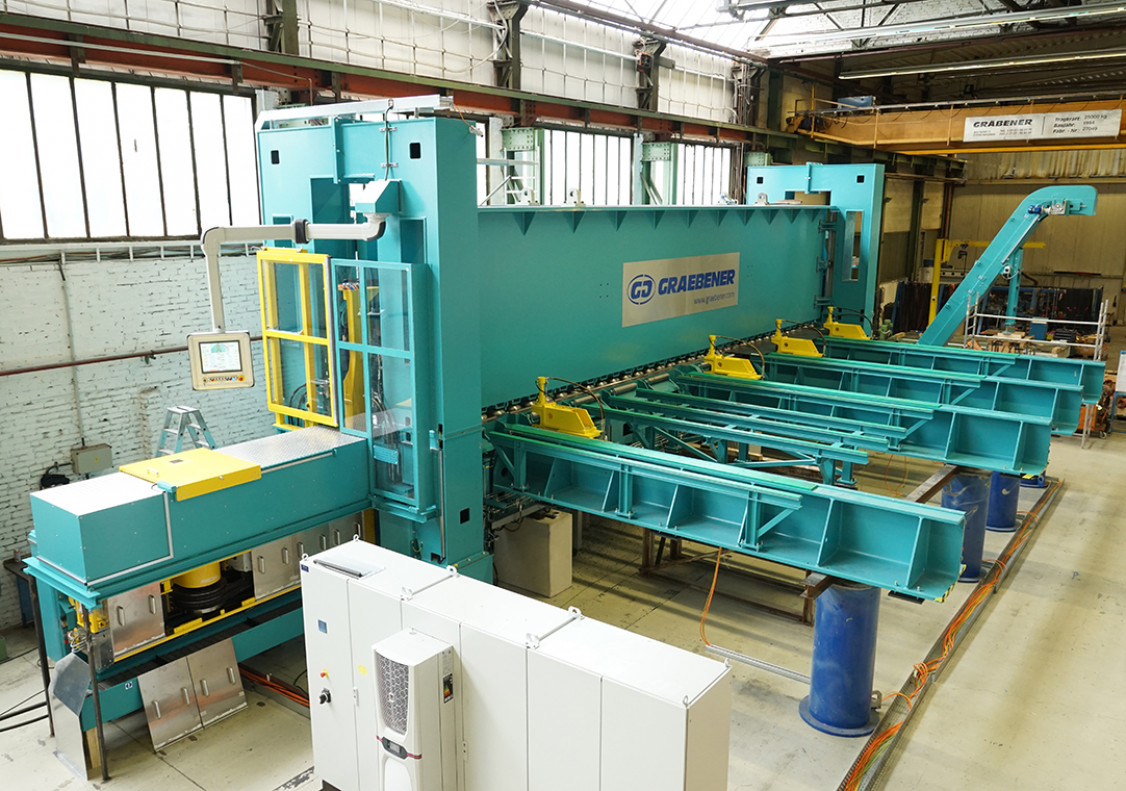
MMHE is now expanding its production site with a new production line. The start of production is scheduled for 2025. With the new production line, the goal is to make production even more efficient. The 2-side plate edge milling machine from Graebener is perfectly designed for this, as it allows two individual plates to be milled in one milling process, which doubles the milling output. Both plates – one on the infeed side, the other on the outfeed side of the system – are firmly clamped and then milled simultaneously with a milling head passing between the plates. The benefit of simultaneous milling of two plate edges is therefore a reduction in milling times of up to 50% which enables the panel line to finish the welding process faster.
The scope of delivery of the plate edge milling machine also includes three different milling heads. While one of the milling heads is used for chamfering the plates, the other two milling heads serve to produce a wide variety of X, I and Y seams. The plate thicknesses of the individual plates, which can measure up to 12,050 mm in length, vary between 6-25 mm.
Since 1998, this and similar Graebener milling technology has been used to prepare weld seams for ship decks, large pipes, vessels, wind towers and monopiles. This technology is now also being used in the production of the large offshore converter platforms. Following a joint visit to a renowned shipyard in northern Germany, which has been working with various highly automated Graebener equipment for years, MMHE relies on the long-standing cooperation between IMG and Graebener.
Graebener’s customized milling systems are available in a vast range of concepts. In addition to the 2-side plate edge milling machines, the custom machine builder also provides 1-side plate edge milling machines, 2-side plate pull-through milling machines, 4-side plate edge milling machine machines and complete panel production lines including laser hybrid welding technology.
(Source: Gräbener Maschinentechnik GmbH & Co. KG)