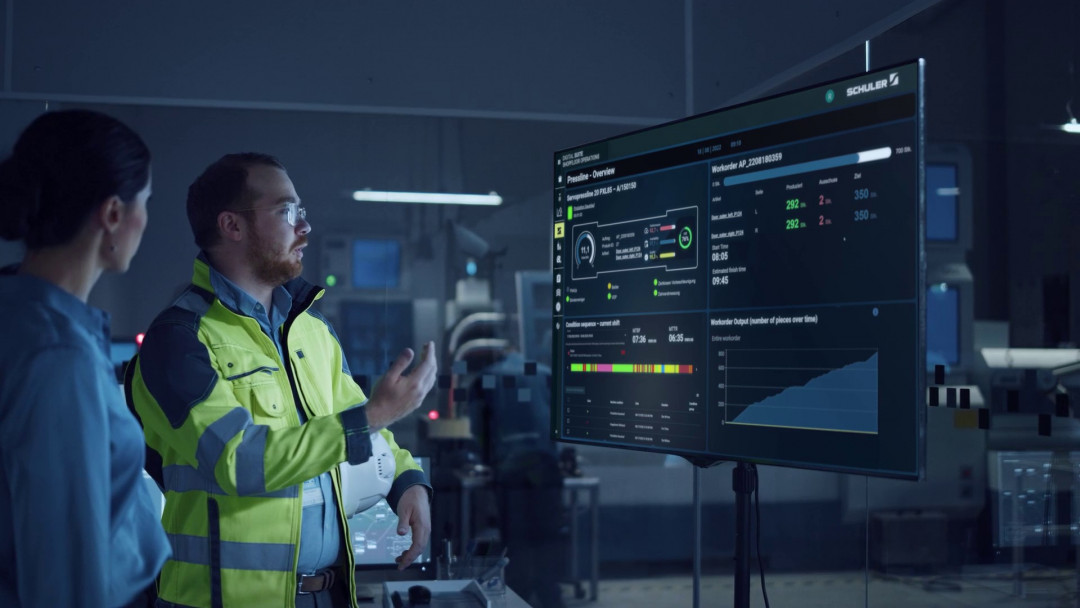
Facilitating Mobility and Sustainability
Schuler will showcase its product portfolioin the forming technology at the Blechexpo trade fair from November 7 through 10 in Stuttgart, Germany. Schuler's sheet metal forming lines are diverse: They range from the larger-than-man-sized C-frame press for packaging to press lines filling factory halls that form car doors and engine hoods, among other things.
Notching presses for electrical sheets and production lines for battery housings are also part of the portfolio. Added to this are the numerous digital applications that Schuler has already developed for the forming technology. Schuler will be presenting all these solutions at the Blechexpo trade fair from November 7 through 10 in Stuttgart at Booth 8306. "Our lines make mobility and sustainability possible because they produce, for example, the components for electric cars with a long range or electrolysers for the production of hydrogen," emphasizes Schuler CEO Domenico Iacovelli. "With the help of our applications from the Digital Suite, the production lines themselves can also be operated energy-efficiently and economically." Schuler's single presses are of modular design, so are the multi-stage press lines. ServoMAX can produce a particularly large number of parts cost-effectively.
For those who want to take advantage of all the benefits of servo technology but do not require maximum output, Schuler now offers the ServoNEXT press line. The MechNEXT is an additional mechanical press line without servo drive. Laser blanking lines cut the blanks which the press lines then form into body and structural parts. In addition to the established lines with two and three laser cutting heads, Schuler has now added a more cost-effective one to its product portfolio which operates with one cutting head. All laser blanking lines allow die-free blanking: To change from one geometry to the next the simple push of a button is all it takes.
Lighter components extend the range of vehicles – whether electric or fuel powered. A new process for hot stamping aluminium is therefore now used on hydraulic presses from Schuler, in which the light metal is heated, formed and simultaneously cooled within a very short time. The result is high-strength components with low weight. Schuler Service, with its experts around the world, helps customers increase the output of their lines and ensure availability.
Shopfloor Operations Management is the name of the latest application from Schuler's Digital Suite, which can even be used to optimize and control an entire press shop. Other solutions include applications from the field of machine vision as well as systems for component tracking and energy optimization. Furthermore, visitors to Schuler's stand at Blechexpo will be able to find out about lines to produce electrical sheets for motors or cylindrical and prismatic battery housings.
(Source: Schuler Group GmbH Press Release)
Schlagworte
BlechexpoE-MobilityFormingMetal FormingSheet MetalSustainability