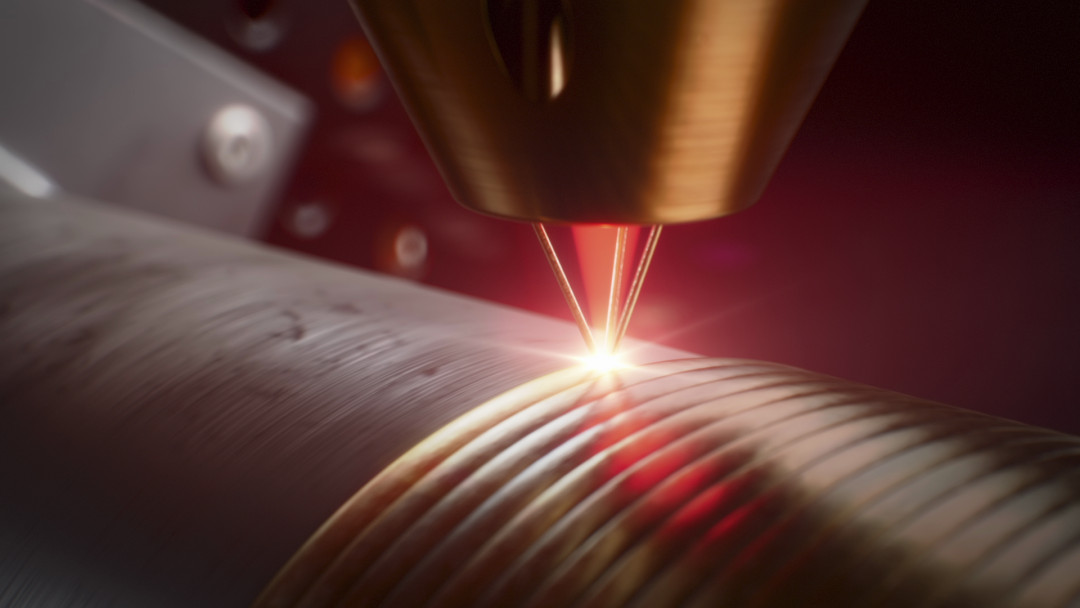
Laserline Presents Sustainable Solutions for Laser Cladding and Additive Manufacturing at Formnext 2024
Sustainable solutions for cladding and additive manufacturing will dominate Laserline’s presence at Formnext (November 19 through 22, 2024, Frankfurt a. M., Germany). The trade show highlight is the first blue industrial diode laser with 6 kW CW output power, which enables energy- and material-efficient processes in additive manufacturing of copper components. Its wavelength of 445 nm is absorbed by copper alloys five times better than infrared wavelengths, resulting in calm molten pools without pore formation.
The increase in power to 6 kW now enables even higher process speeds than before, opening up new opportunities for particularly efficient and thus CO2-reduced processes in cladding and additive manufacturing. Additionally, Laserline is expanding its portfolio of industrial diode lasers with particularly high beam qualities of 4 mm mrad and better by acquiring a majority stake in the US laser specialist WBC Photonics. Due to their focusability, these laser types are particularly suitable for additive manufacturing in powder bed processes..
Efficient and CO2-reduced coating processes
Laserline’s newly developed TwinClad and MultiWire optics, which will also be on display at the booth, contribute to optimizing the efficiency of cladding processes. The TwinClad models split the laser beam into a pre-beam and a main beam, making them particularly suitable for high-speed applications such as brake disk cladding. The innovative beam shaping technology enables efficient cleaning and tempering of the workpiece surface. Additionally, their flexible design allows for the customization of both the geometry of the weld spot as well as the amount and composition of the powder to meet various production requirements. The MultiWire optics, on the other hand, enable the superior application of coatings in any direction. With the help of a total of three wire feeders, the application rates can also be significantly increased.
Cladding of wind turbine plain bearings and brake discs
Energy- and material-efficient cladding concepts for wind turbine plain bearings and brake discs for road vehicles will also be presented at the booth. In the case of wind turbine plain bearings, laser cladding enables the realization of particularly workpiece-friendly coatings with long service life. The energy and material consumption are significantly lower compared to the conventional centrifugal casting process. For automotive brake discs, laser cladding guarantees long-term corrosion and wear protection, which reduces the amount of fine dust generated by the braking process by up to 90 per cent. Comprehensive process monitoring ensures high production reliability for both processes. To illustrate the process and the results, Laserline will be showcasing a sample setup for the double-sided cladding of brake discs with up to 30 kW laser power, as well as a multi-component plain bearing that can only be coated in this form using diode lasers.
Formnext, Booth C122 in hall 12.0.
(Source: Laserline GmbH Press Release)
Schlagworte
Additive ManufacturingCladdingCopperLaserSustainability