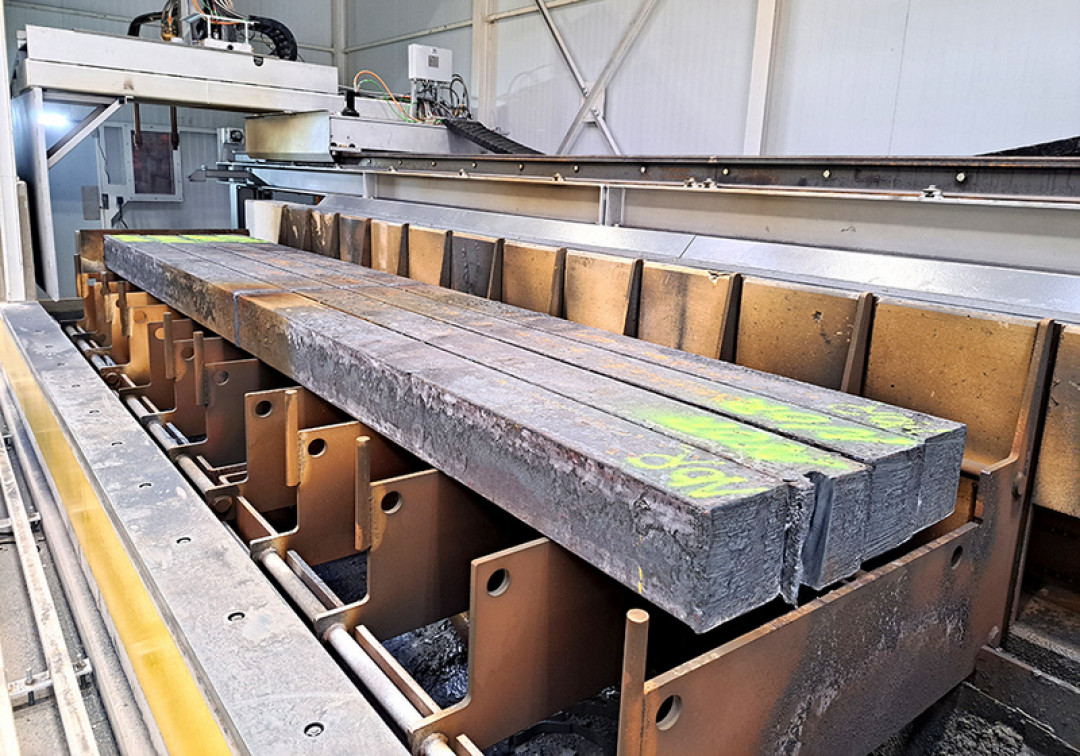
Primetals Technologies Streamlines Scrap Yard Processes by Implementing Torch-Cutting Solution
Recently, German special steel producer Lech-Stahlwerke (LSW) has granted the final acceptance certificate (FAC) to Primetals Technologies for an innovative scrap torch-cutting machine at its plant in Meitingen, Germany. The facility represents the latest development in scrap cutting, resulting in significantly reduced noise and zero dust emissions.
Benefits with In-House Scrap Cutting
The ongoing green transition of the metals industry is set to steadily increase the use of scrap in production processes. The World Steel Association projects that the amount of scrap will reach 1,000 million tons annually within a few years. These market conditions prompt steel producers to streamline their scrap management processes.
Traditionally, scrap cutting was outsourced. However, there are clear advantages for steel producers in operating their own cutting facilities. In this way, they can streamline their scrap sorting and management processes, and the ability to cut scrap to the precise target size ensures an optimal furnace charging process. Moreover, detailed knowledge of the metallurgical properties of the available scrap makes it easier to predict end-product quality.
Enhanced Occupational Safety
Another advantage of Primetals Technologies’ scrap cutting solution is the increased workplace safety for operators, which was a key factor in LSW’s decision to invest. Personnel control the machine remotely from a desk outside the cutting cabin, supported by a video surveillance system. Predefined cutting programs based on recipes simplify machine operation and reduce operating times.

Reduced Emissions
Manual scrap cutting activities have traditionally resulted in heavy noise pollution and significant dust emissions. These issues are effectively mitigated by Primetals Technologies’ scrap cutting solution. Torch noise is drastically reduced outside the cabin, and an effective dedusting system captures all dust emissions generated during the cutting process. This system prevents air pollution and allows the cabin to be housed within a hall, further reducing noise emissions.
Leading Expertise in Torch-Cutting
The scrap torch-cutting machine at LSW can handle various types of scrap, including billets and bundles of rolled bar, as well as tundish scull. This technology was developed by experts from Torch-Cutting Technologies (TCT), a Spanish company acquired by Primetals Technologies in August 2023. TCT is widely recognized for its competences in torch cutting and offers a broad range of innovative solutions for cutting applications in steel plants, rolling mills, forging shops, foundries, and scrap yards.
With approximately 800 employees, LSW produces over one million tons of raw steel annually. Since the first heat in 1972, more than 40 million tons of scrap have been recycled at LSW’s facilities. A key supplier to the automotive industry and its subcontractors, LSW operates two electric arc furnaces at its site in Southern Germany.
Key Facts: LSW’s Torch Cutting Facility
Capacity: 500 tons per day
Maximum thickness: 700 millimeters
Noise outside cutting cabin: below 90 decibels
(Source: Primetals Technologies, Limited)