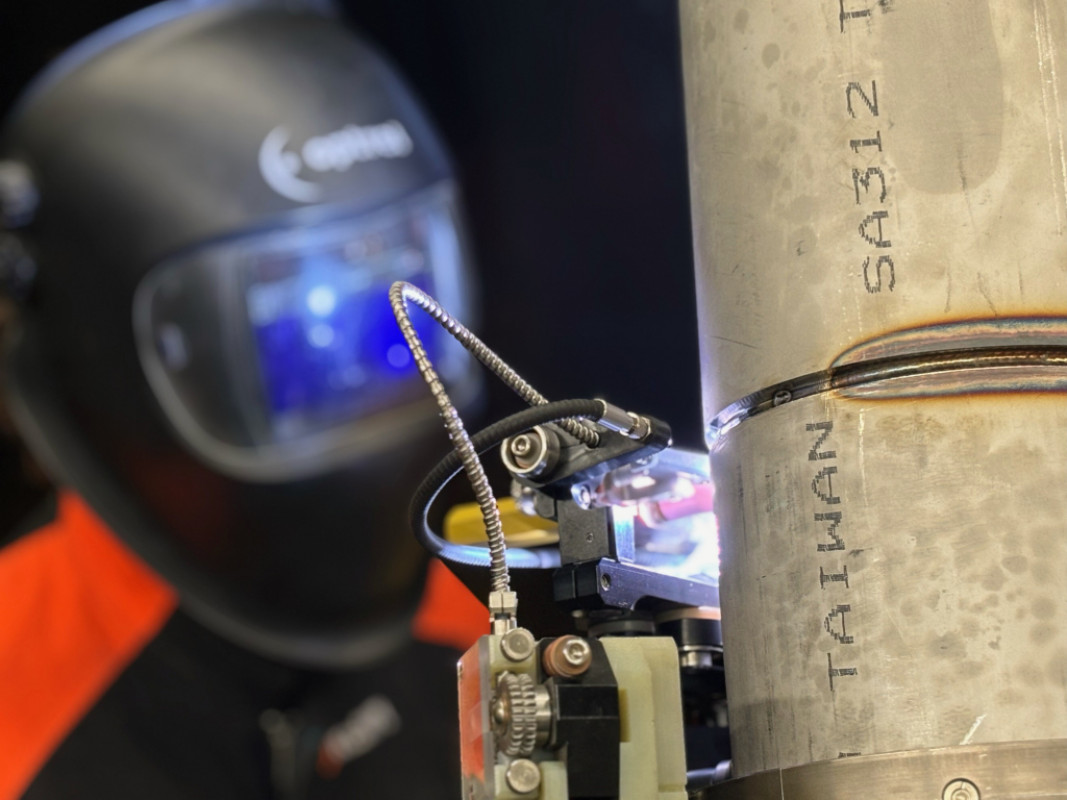
Fachchinesisch in Schweißersprache übersetzen: Aussagekräftige Analyseverfahren der Schutzgasströme finden erstmals praktische Anwendung in der Industrie
Durchschnittlich fällt etwa 50 Prozent des Aufwands beim WIG-Schweißen auf nachgelagerte Prüf- und Nacharbeiten. Bei höheren Qualitätsanforderungen steigt der Anteil dieser Arbeitsschritte schnell auf zwei Drittel des Produktionsprozesses, da engere Prüfungszyklen und aufwändigere Reparaturschweißungen erforderlich sein können. Dabei kann der Aufwand durch die Auswahl der Parameter des Schutzgases deutlich reduziert werden. Diese Faktoren lassen sich jedoch üblicherweise erst an ihren Effekten bewerten. Eine Korrektur ist dann maximal für das nächste Werkstück möglich, das unter Umständen eine Anpassung der anderen Prozessgrößen notwendig macht. Zwar können Schlierenmethoden frühzeitig bei der Ermittlung der passenden Schutzgasparameter helfen. Doch die präzisen bildgebenden Verfahren wurden bisher ausschließlich in der akademischen Forschung eingesetzt und ließen sich kaum in die industrielle Praxis übersetzen. Über diesen scheinbar unüberwindbaren Abgrund zwischen Industrie und Forschung hat die Wolfram Industrie eine Brücke gebaut: Durch eine Kombination aus Schlieren- und sensorischen Messungen bietet sie in ihrem Schweizer Schweißlabor Entwicklungen und Beratungen zur Optimierung des WIG-Schweißprozesses speziell für industrielle Anwendungen an.
Oxidiert die Elektrode, etwa, weil der Schutzgasstrom zu niedrig eingestellt wurde, dann tut es auch das Bauteil. Denn das WIG-Schweißen findet in einem geschlossenen System statt, in dem es zu Wechselwirkungen zwischen den einzelnen Komponenten Wolframelektrode, Schweißnaht und Schutzgas kommt. Dies bringt einige Herausforderungen mit sich, denn je nach Anwendungsbereich kann etwa eine poröse oder anderweitig fehlerbehaftete Schweißnaht am Bauteil fatale Folgen nach sich ziehen. Hinzu kommt, dass der Schweißprozess, also das Zusammenfügen der Komponenten, oftmals relativ spät innerhalb der Wertschöpfungskette stattfindet. Qualitätsmängel, die erst an dieser Stelle auftreten, können die gesamte Produktion folglich schmerzhaft ausbremsen.
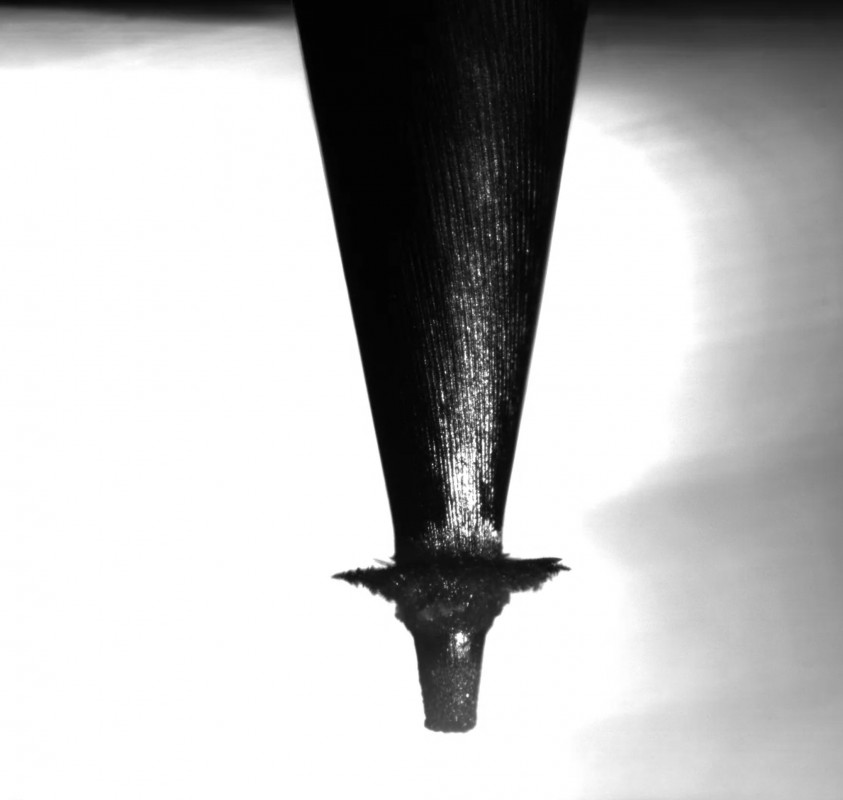
Allerdings handelt es sich beim Gasschutz um eine Einflussgröße, die sich nicht intuitiv bestimmen lässt. Auch Empfehlungen sind größtenteils nur allgemein gehalten und können von den bei einer spezifischen Anwendung tatsächlich benötigten Konfigurationen stark abweichen. Schwierigkeiten wie Elektrodenverschleiß, Zündprobleme oder Materialfehler werden daher häufig durch einen zu hohen Gasdurchfluss, der starken Turbulenzen unterliegt, oder einen zu geringen Volumenstrom hervorgerufen, der den Gasschutz wiederum anfälliger für Luftverwirbelungen und Zugluft am Arbeitsplatz macht. Bei einer unpassenden Konfiguration der Schutzgaszufuhr wird der WIG-Schweißprozess aus diesem Grund schnell zu einem kostspieligen Unterfangen.
Aufwändige Nacharbeiten und Produktionsausfälle
Einer der größten Kostenfaktoren entsteht durch Nacharbeiten, mit denen beim Schweißprozess aufgetretene Qualitätsmängel ausgeglichen werden. Hierzu zählen Reparaturschweißungen, die periphere Oxidationen entfernen und so die Oberflächenbeschaffenheit verbessern sollen. Hinzu kommen zerstörungsfreie Werkstoffprüfungen, bei denen die Schweißnaht etwa auf Porosität bis in den Mikrobereich hinein getestet wird. Während Oxidation durch den namensgebenden Sauerstoff hervorgerufen wird, entsteht Porosität im Metall üblicherweise durch Stickstoff oder Wasserstoff. Beides lässt sich in der Regel auf falsch konfigurierten Gasschutz zurückführen und durch eine Prozessverbesserung beseitigen.
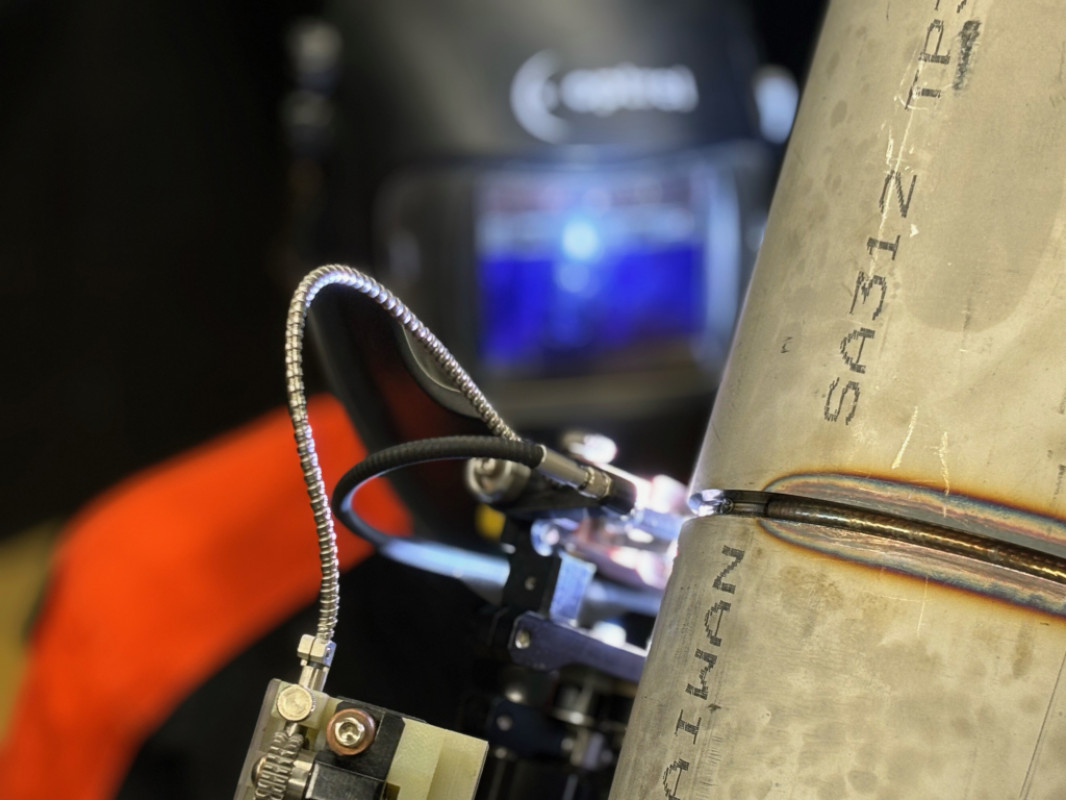
Mit steigendem Automatisierungsgrad in der Produktion fällt auch die Maschinenverfügbarkeit immer mehr ins Gewicht. Denn um wirtschaftlich rentabel zu sein, sind aufwändige und kostenintensive Schweißzellen, Orbitalanlagen sowie generell Automationen auf einen hohen Auslastungsgrad angewiesen. Die eingesetzte Wolframelektrode kann hier allerdings einen Strich durch die Rechnung machen: Turbulente Gasströme lassen selbst hochwertige Elektroden oxidieren, was nicht nur die Qualität der Schweißnaht, sondern auch die Herstellkosten signifikant erhöht. Falsch oder nicht ideal eingestellte Gasmengen und -zeiten machen daher häufige Verschleißteilwechsel und damit einhergehende Anlagenstillstände notwendig, was die Produktivität deutlich einschränkt. Dabei können schon kleine Anpassungen markante Verbesserungen erzielen.
Viel hilft nicht viel
Die dritte Kostengröße liegt im Verbrauch des Schutzgases selbst. Die Prämisse „viel hilft viel“ bringt beim Schutzgasschweißen keinerlei Mehrwert. Im Gegenteil: In der Praxis lässt sich beobachten, dass viele Probleme erst durch einen zu hohen Gasfluss entstehen. Neben der Verbesserung der Schweißqualität schlägt sich die Reduktion des unnötigen Gasverbrauchs also unmittelbar auf die Produktionskosten nieder. Besonders beim Einsatz von Mischgasen mit einem hohen Anteil an Helium kommen schnell erhebliche Mehrkosten zustande. Indem die Gaszufuhr speziell auf die jeweilige Anwendung hin optimiert wird, lassen sich folglich bis zu mehrere hundert Euro pro Produktionstag einsparen.
Zwar gibt es Messmethoden, mit denen sich der Gasschutz auf spezifische Bedingungen auslegen lässt. Diese finden bisher allerdings beinahe ausschließlich in der akademischen Forschung Anwendung. Für die Industrie bedeutet dies: Die Auswirkungen der einzelnen Parameter lassen sich in der Praxis erst an den jeweiligen, meist negativen Effekten beobachten. Erschwerend kommt hinzu, dass das Gas selbst mit dem bloßen Auge nicht wahrgenommen werden kann. Hinweise auf einen fehlerhaft eingestellten Schutzgasstrom sind für den Schweißer zunächst an Anlauffarben sowie dem Verschleiß der Wolframelektrode erkennbar. Die problematischeren Qualitätsmängel am Werkstück selbst wie Porosität findet man in der Regel nur bei einer prozessbegleitenden oder nachfolgenden volumetrischen Werkstoffprüfung. Eine Optimierung der Parameter kann sich also frühestens auf das nächste Werkstück auswirken – sofern dieses nicht völlig andere Prozessbedingungen erfordert.
Neues Bindeglied zwischen Akademie und Industrie
Um das aufwändige Trial-and-Error-Prinzip nicht länger hinnehmen zu müssen, betreibt die Wolfram Industrie an ihrem Standort in der Schweiz ein Schweißlabor. Dort können die Schweißexperten die Umgebungsbedingungen jeder beliebigen WIG-Schweißanwendung exakt nachstellen, messen und optimieren. Hierzu wurden zwei Ansätze aus der wissenschaftlichen Forschung für die Anwendung in der Industrie adaptiert: Zum einen sind dies Schlierenmethoden, ein bildgebendes Verfahren aus der Strömungstechnik, mit dem sich Gas- und Wärmeströmungen bei brennendem Lichtbogen hochauflösend abbilden lassen. Zum anderen kommen bei Wolfram Industrie sensorische Messungen zum Einsatz, die beispielsweise den Staudruck, die Geschwindigkeit und die chemische Zusammensetzung des Schutzgases erfassen. In Verbindung mit präzisen Positionsdaten lässt sich der Gasschutz auf diese Weise dreidimensional vermessen und unter Berücksichtigung sämtlicher Umgebungsbedingungen sowie Einflussgrößen für den einzelnen industriellen Anwendungsfall optimieren.
(Quelle: Gesellschaft für Wolfram Industrie mbH, Autor: Matthias Schaffitz, Anwendungstechniker bei Wolfram Industrie)
Schlagworte
FachkräftequalifizierungNacharbeitenPrüfungQualitätskontrolleQualitätssicherungReparaturschweißenReparaturschweißungenSchutzgasSchutzgasschweißenSchweißtechnikWIG SchweißenWIG-Schweißen