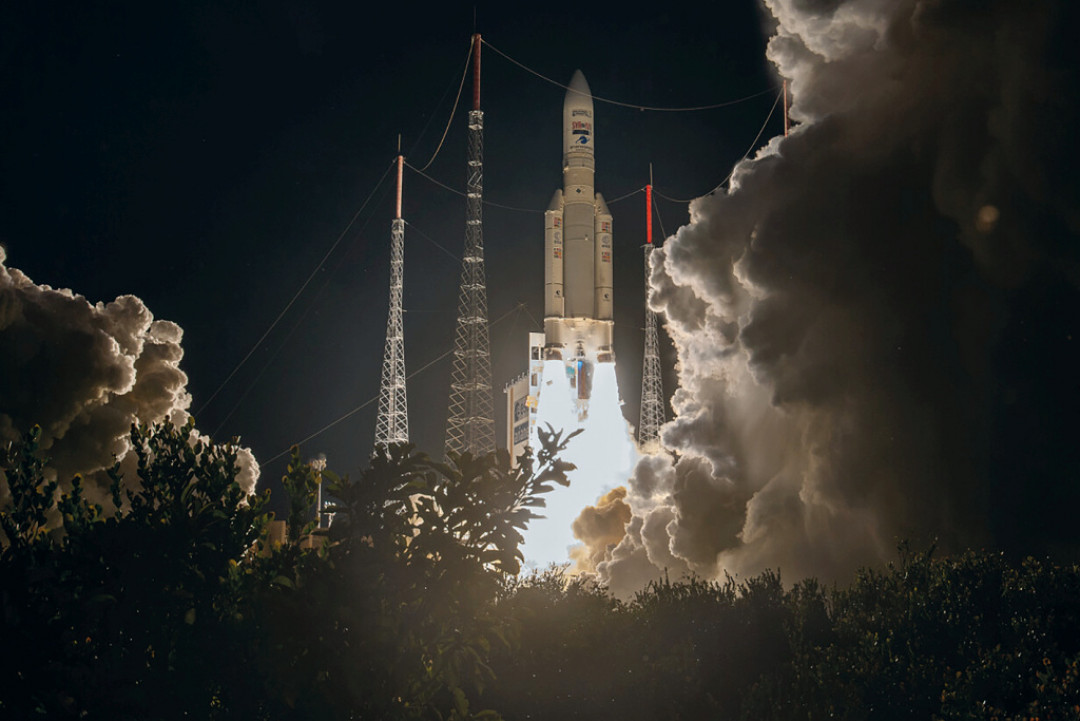
Fertigungstechnologien für die Zukunft der europäischen Raumfahrt
Der Weltraum war nie so nah, ein Flug ins All nie so greifbar wie heute. Um die Wettbewerbsfähigkeit europäischer Raumtransportsysteme zu steigern, entwickeln Forschende des Fraunhofer-Instituts für Lasertechnik ILT im Projekt ENLIGHTEN zukunftsweisende Fertigungstechnologien für Raketenkomponenten. Vom 22. bis 26. April 2024 präsentieren sie ihre Ergebnisse auf der Hannover Messe (Halle 2, Stand B24).
Nichts Geringeres als die erfolgreiche Zukunft der europäischen Raumfahrt haben sich Min-Uh Ko und sein Team am Fraunhofer ILT zur Aufgabe gemacht: Die Wissenschaftlerinnen und Wissenschaftler arbeiten im Rahmen des Projekts ENLIGHTEN (European iNitiative for Low cost, Innovative & Green High Thrust ENgine) an neuen Technologien, um die Kosten für die Raumfahrt zu senken und die Konkurrenzfähigkeit Europas auf diesem Gebiet zu stärken. Insgesamt 18 Partner sind in das Vorhaben involviert, das die Europäische Kommission vorantreibt, um im zunehmenden globalen Wettbewerb technologisch souverän zu bleiben und autonom agieren zu können.
Die Grenzen des Machbaren verschieben
Zu teuer, zu träge: Neue Schubkraft für die europäische Raumfahrt ist wortwörtlich das, was die Expertinnen und Experten am Fraunhofer ILT im Projekt leisten. Ihre Intention: die Düse eines Raketentriebwerks mittels Laserauftragschweißen (Laser Material Deposition, LMD) additiv zu fertigen und einen maßstabsgetreuen Demonstrator dazu aufzubauen. Die neu gedachte Fertigung ist ein entscheidender Schritt hin zu mehr Kosteneffizienz und beschleunigten Abläufen.
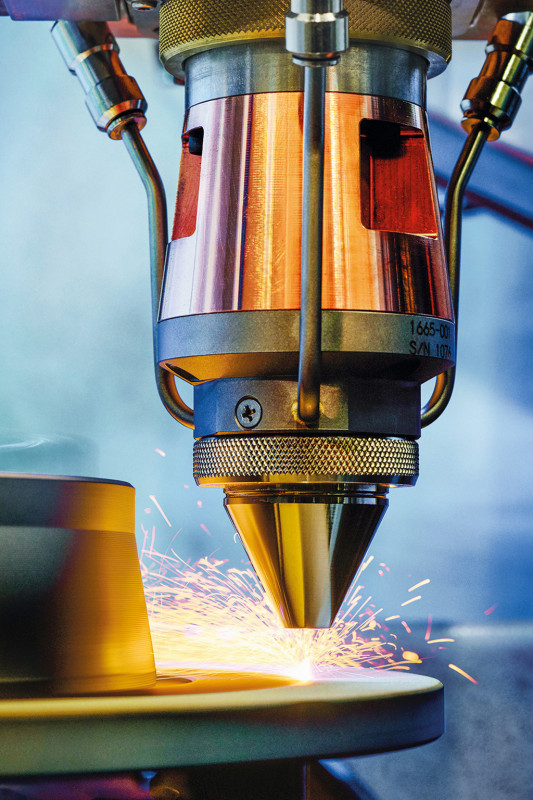
„Das Besondere ist, dass wir durch die vielfältigen Möglichkeiten der LMD-Technologie die Geschwindigkeit und Wirtschaftlichkeit bei der Herstellung neuartiger Generationen von Raketendüsen drastisch verbessern. Das untersuchte Design verfügt abgesehen von seinem großen Bauraum über außergewöhnlich filigrane und dünnwandige Kühlkanäle, die mit konventionellen Fertigungsrouten nur unter großem Aufwand realisiert werden können“, erläutert Teilprojektkoordinator Ko.
Flexibel, produktiv, exakt – und dadurch wegweisend
Andere Verfahren wie das drahtbasierte Lichtbogenverfahren, kurz WAAM (Wire and Arc Additive Manufacturing) oder Laser Powder Bed Fusion (LPBF), sind entweder nicht in der Lage, vergleichbar filigrane Strukturen zu realisieren, oder weisen eine erheblich geringere Produktivität als LMD-Verfahren auf. Zudem ist gerade beim LPBF der Bauraum stark eingeschränkt. „Das Spannende an der LMD-Technologie ist, dass das Prozess-Prinzip auf fast jede Anlagen-Kinematik transferiert werden kann. Dementsprechend ist der Bauraum auch einfach skalierbar“, präzisiert der Experte des Fraunhofer ILT Ko.
Die dünnwandigen Strukturen der Raketenschubdüse erfordern Strahlquellen mit einer spezifischen Strahlqualität, die einen besonders kleinen Laserstrahldurchmesser erzeugen. „In diesem Bereich sind wir besonders stark, weil wir im Haus diverse Strahlquellen und Optikkonfigurationen haben, die wir auf den Anwendungsfall individuell anpassen können“, verdeutlicht Jochen Kittel, Projektleiter des ENLIGHTEN-Vorhabens am Fraunhofer ILT.
Raketenfertigung auf der Überholspur
Die Düse des Fraunhofer ILT ist für den Einsatz als Komponente der nächsten Raketengeneration im Ariane-Programm ausgelegt. Die Ariane-Gruppe ist der Projektkoordinator des Projekts ENLIGHTEN und steuert das gesamte Vorhaben. Tatsächlich ist die Raketendüse mit konventionellen Methoden bereits herstellbar. Doch die vielen aktuell nacheinander gelagerten Prozessschritte führen zeitlich wie kostentechnisch zu Herausforderungen: Da kein Anbieter alle Schritte in einer lokalen Produktion umsetzen kann, müssen die Bauteile zu mehreren Standorten transportiert werden. Die dadurch entstehende Prozesskette zieht Produktions- und Lieferzeiten deutlich in die Länge.
„Mit einer Prozesstechnologie, die viele einzelne Prozessschritte einspart, gelingt uns nicht nur eine deutliche Kostenreduktion. Zeitgleich verkürzen wir die Produktionszeit einer Raketendüse deutlich. Diese liegt aktuell quartalsübergreifend deutlich über mehreren Monaten“, unterstreicht Projektleiter Kittel.
Enabler für die Industrie
Über Fertigungstechnik und Demonstrator-Realisierung hinaus liegt das Augenmerk der Fachleute des Fraunhofer ILT auf Prozessüberwachung und Qualitätssicherung. Ziel des Teams ist, die Zuverlässigkeit und Robustheit der am Fraunhofer ILT entwickelten Technologien so weit zu optimieren, dass die Forschenden diese für eine künftige Serienfertigung an die Industrie übergeben können. Aus diesem Grund wird parallel ein Prozessüberwachungssystem eingesetzt, um mit den Sensordaten eventuelle Prozess- Anomalien zu lokalisieren, sie zu beheben und damit die Bauteilqualität durchgehend zu gewährleisten.
„Wenn wir das Verfahren und den Demonstrator erfolgreich entwickelt haben, markiert das einen Durchbruch. Mit unseren Ergebnissen können wir die Industrie dazu befähigen, als Zulieferer für die Luft- und Raumfahrtindustrie künftig auf ihren eigenen Anlagen via LMD ebenso große, komplexe und filigrane Strukturen herzustellen“, ist Min-Uh Ko überzeugt.
Mit vereinten Kräften zu den Sternen
Die Initiative der Partner im Projekt ENLIGHTEN beweist: Wenn Europa seine Kräfte bündelt, kann es auch weiterhin eine bedeutende Rolle in der globalen Raumfahrt spielen.
Vom 22. bis 26. April 2024 präsentieren die Fraunhofer-ILT-Expertinnen und -Experten die aktuellen Ergebnisse aus dem laufenden Vorhaben für ein zuverlässiges und wettbewerbsfähiges europäisches Raumtransportsystem auf der Hannover Messe am Fraunhofer-Gemeinschaftsstand in Halle 2, Stand B24.
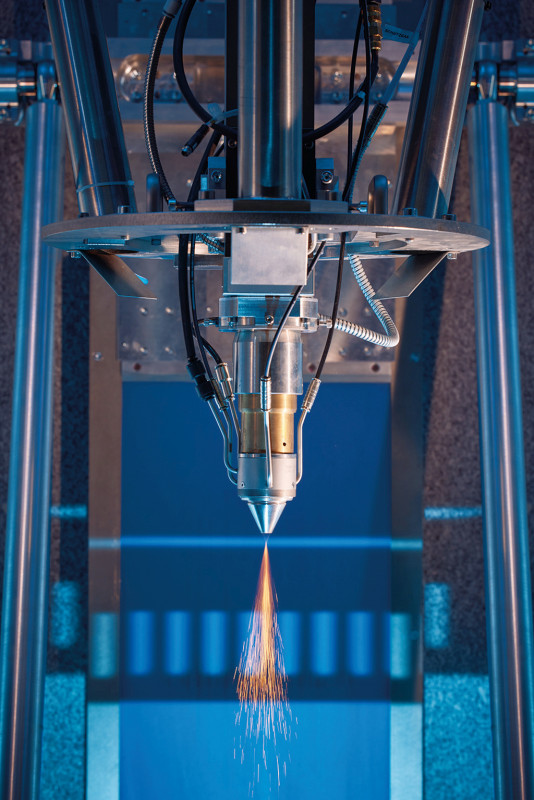
Die Zukunft der europäischen Raumtransportsysteme sieht dank Vorhaben wie dem ihren vielversprechend aus.
(Quelle: Presseinformation des Fraunhofer-Instituts für Lasertechnik ILT)
Schlagworte
Laser Powder Bed FusionLaserauftragschweißenLasertechnikLasertechnologienRaumfahrtRaumtransportsystemeWAAM