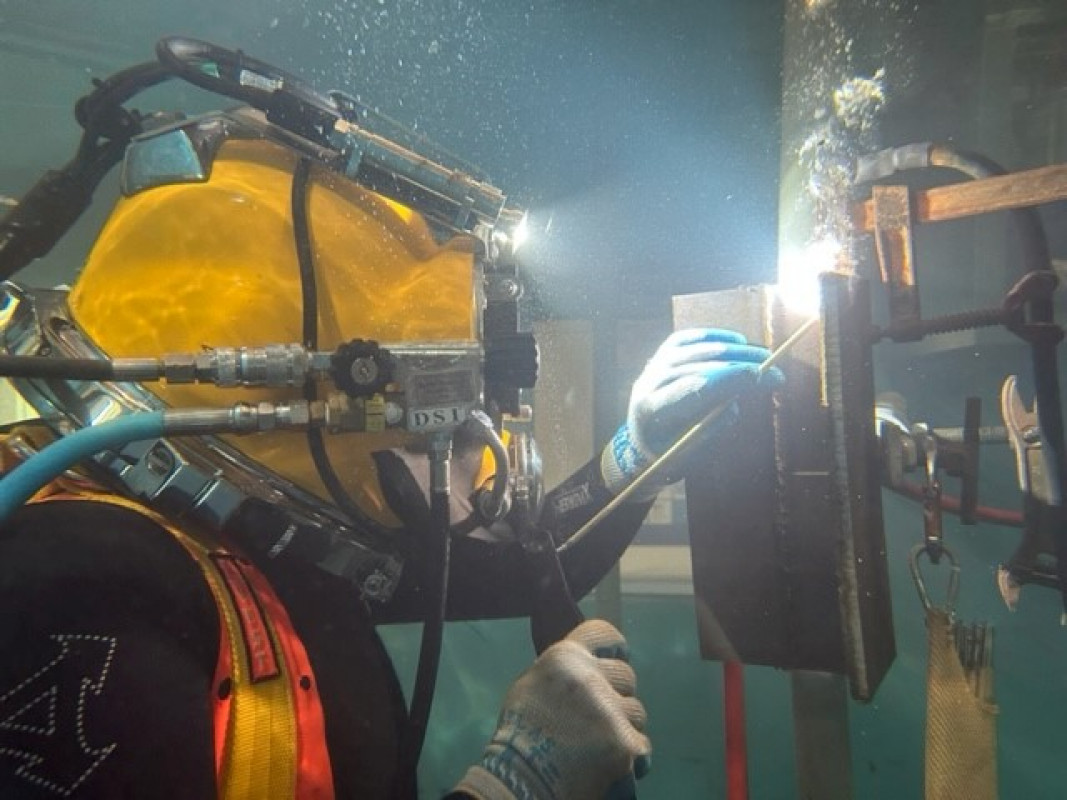
Underwater Weld Repairs - Requirements and Execution, Part 1
Introduction
Underwater welding, especially underwater wet welding, is gaining more and more acceptance. This is due not least to specially developed welding consumables, improved techniques and better training of the welder divers. Corrosion and the associated need for maintenance as well as accidents on underwater structures that cannot be brought easily to the surface, such as: ships, structures in the offshore oil and gas industry and other areas of application require underwater welding work. This article is a brief introduction to the differences between underwater dry and underwater wet welding, including their process limitations, with emphasis on underwater wet welding. The reader receives an overview of existing regulations, with the focus on the AWS D3.6M: Underwater Welding Code. The quality of underwater wet-welded connections is illustrated using examples of afloat repairs carried out on ships and on an offshore oil and gas floating asset.
Brief history of diving and underwater welding
Diving for the purpose of combat dates to the times of the Roman Empire and Ancient Greece. Plant stalks were used as snorkels. Over the following centuries, diving techniques and diving equipment were developed. While working in Venice, the "water city", in 1500, Leonardo da Vinci designed his scuba gear for sneak attacks on enemy ships from underwater. In 1829, the first diving helmet was designed and built by Charles Anthony and John Deane from Whitstable in Kent, England. In 1843, the Royal Navy founded the first diving school.
At the beginning of the 20th century, professional diving had already been around for hundreds of years, but underwater welding had not yet been developed. This changed when Konstantin Konstantinovich Khrenov, a Russian metallurgist, welding pioneer and university professor, developed a method for joining and cutting metals underwater and demonstrated it in 1932 with successful tests in the Black Sea. The first practical application of underwater wet welding took place in 1936 during the salvage of the merchant ship “SS Boris” from the Black Sea.
During World War II, underwater wet welding was used as an emergency repair method and in salvage operations. Cyril Jensen, a civil engineer and fascinated by Khrenov's work, started an underwater welding program in the mid-1940’s as part of the US NAVY Experimental Station for Welding Research, in Annapolis, Maryland, USA. In the late 1960’s and early 1970’s, underwater wet welding gained further momentum with the emergence of the offshore oil and gas industry. With the development of purpose build underwater wet welding electrodes, the development of underwater wet welder training curriculums and research aimed towards underwater wet welding, today we can produce wet welds comparable to their top site welded counterparts.
Types of underwater welding
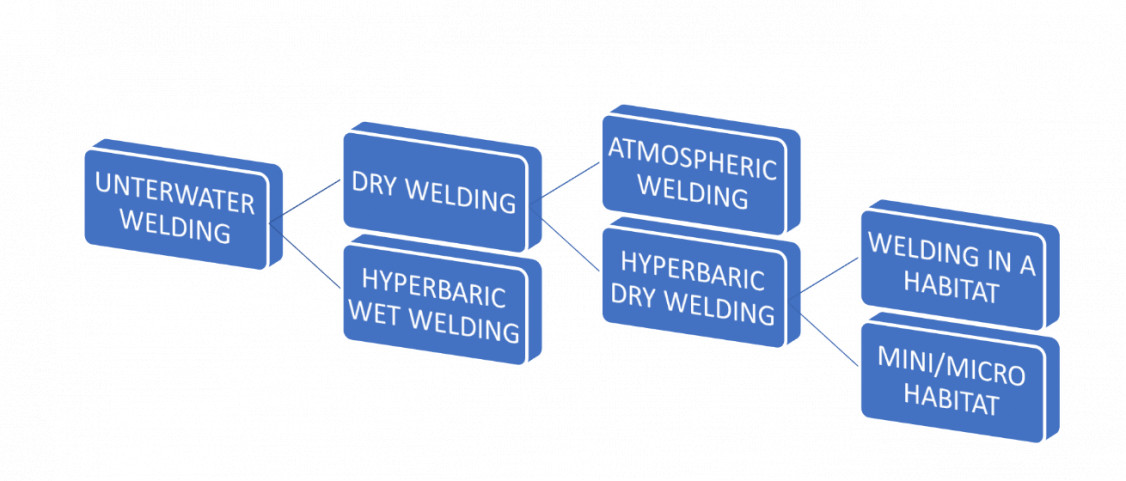
Underwater welding can be broadly categorized into two main techniques: underwater dry welding and underwater wet welding. Each method has its own set of advantages, limitations and applications.
Hyperbaric dry welding
The technical compromise between wet and one atmosphere welding underwater is hyperbaric dry welding. The challenges associated with these two techniques are to eliminate the wet environment and the high-pressure differential in the chamber. The repair site is surrounded within a working habitat, made of relatively lightweight materials, as it needs only to resist modest pressure differentials. The de-watering of the habitat is achieved by filling it with gas (breathing gas), which displaces the water. The ambient pressure at which the welding is performed corresponds to the pressure at the work site. However, the increased pressures influence the reaction of gases, slag and metals in all welding processes. High density gases increase the heat loss of the weld.
Hyperbaric dry welding using mini/microhabitat
Using a mini- or micro habitat, the diver is in the water while welding takes place in a dry environment. In the mini habitat, the electrode is inserted into the habitat through rubber grommets. In the Micro Habitat, the electrode holder, the welding electrodes, the materials and the tools are stored inside the habitat. The diver manipulates the electrode holder, electrodes and tools from the water side using permanently installed gloves, while watching through a window.
Hyperbaric wet welding
Hyperbaric wet welding is carried out at ambient pressure, with the welder-diver in the water. There is no physical barrier between the water and the welding arc. The welder diver in in the photograph below installs a slip-on flange with the shielded metal arc welding process (SMAW-111) on a stationary subsea pipe in a water depth of approx. 10 m just off the coast of St. Thomas in the US Virgin Islands.
Tune in for Part 2 tomorrow, featuring "Factors influencing the weld quality in hyperbaric wet welding"
Authors
Uwe Aschemeier, SGS Subsea Global Solutions, Miami FL, USA
Kevin Peters, SGS Subsea Global Solutions, Miami FL, USA