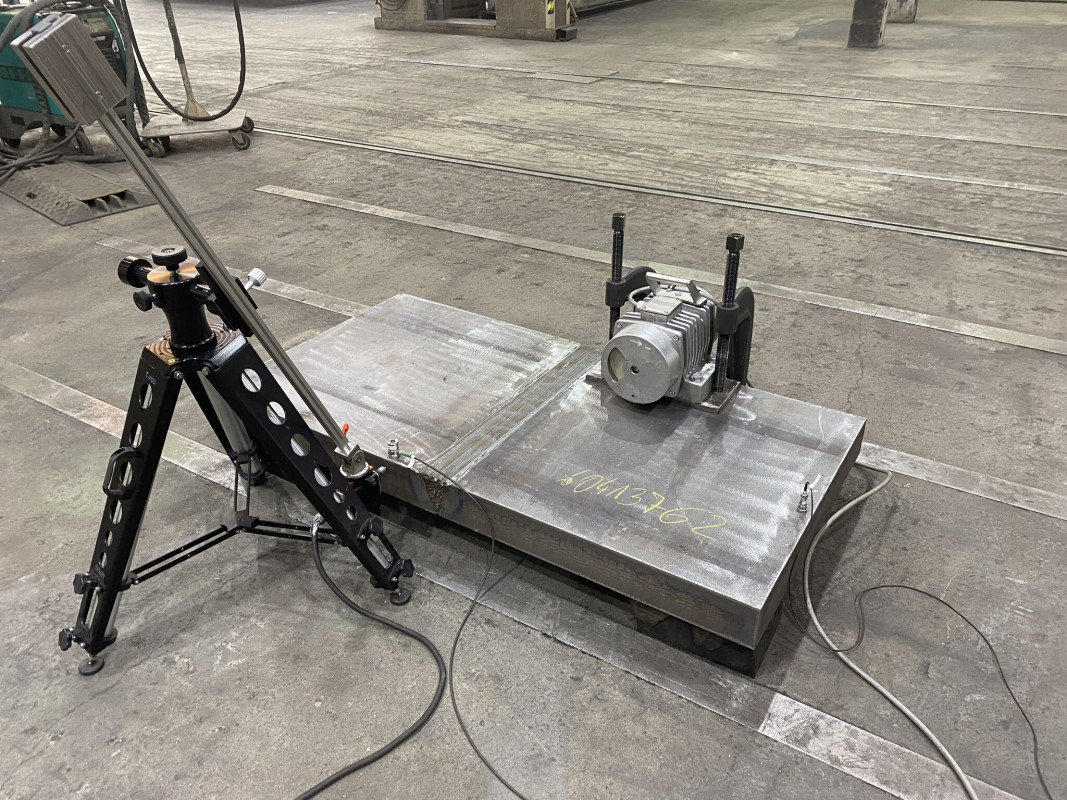
Entspannt bei Jebens: Dimensionsstabilität von Schweißbauteilen durch Vibrieren
In Bauteilen aus metallischen Werkstoffen entstehen während der Herstellung, Verarbeitung und Verformung Eigenspannungen, die ungleichmäßig ausgeprägt und verteilt sind. Bei der weiteren Verarbeitung können diese zu Verzug und Rissbildung am Bauteil, zusammen mit der Betriebslast sogar zu dessen Versagen führen. Traditionell gilt Spannungsarmglühen als Mittel der Wahl, um innere Spannungen in metallischen Gefügen abzubauen. Seit Jahrzehnten gleichermaßen bewährt, jedoch deutlich weniger bekannt und genutzt ist Vibrationsentspannen – ein Verfahren, das erheblich schneller, kostengünstiger und umweltfreundlicher ist. Angesichts steigender Anforderungen an Umweltschutz, Ressourcenschonung und Kostengefüge gewinnt Vibrationsentspannen zur Dimensionsstabilisierung von Schweißbauteilen vor, während oder nach mechanischer Bearbeitung deshalb mit Blick auf Nachhaltigkeit und Wirtschaftlichkeit an Bedeutung.
Als ausgewiesener Experte für große schwere Brennteile und komplexe Baugruppen setzt die Jebens GmbH mit Sitz in Korntal-Münchingen dieses Verfahren aus Überzeugung ein und tritt für dessen breite Anerkennung ein. Vor rund 100 Jahren in den USA eingeführt und seit 50 Jahren von der VSR-Industrietechnik GmbH auch in Deutschland vertrieben und entschieden verbessert, arbeitet Vibrationsentspannen mit gezielt eingesetzten Vibrationen in Bauteilbereichen mit vorhandenen Eigenspannungen. Durch die gezielte Lasteinwirkung des Unwuchtmotors in die Bereiche mit hohem Eigenspannungsanteil wird die Fließgrenze des Werkstoffs lokal überschritten. So kommt es zur lokalen Entspannung und zum Abbau von Eigenspannungen.
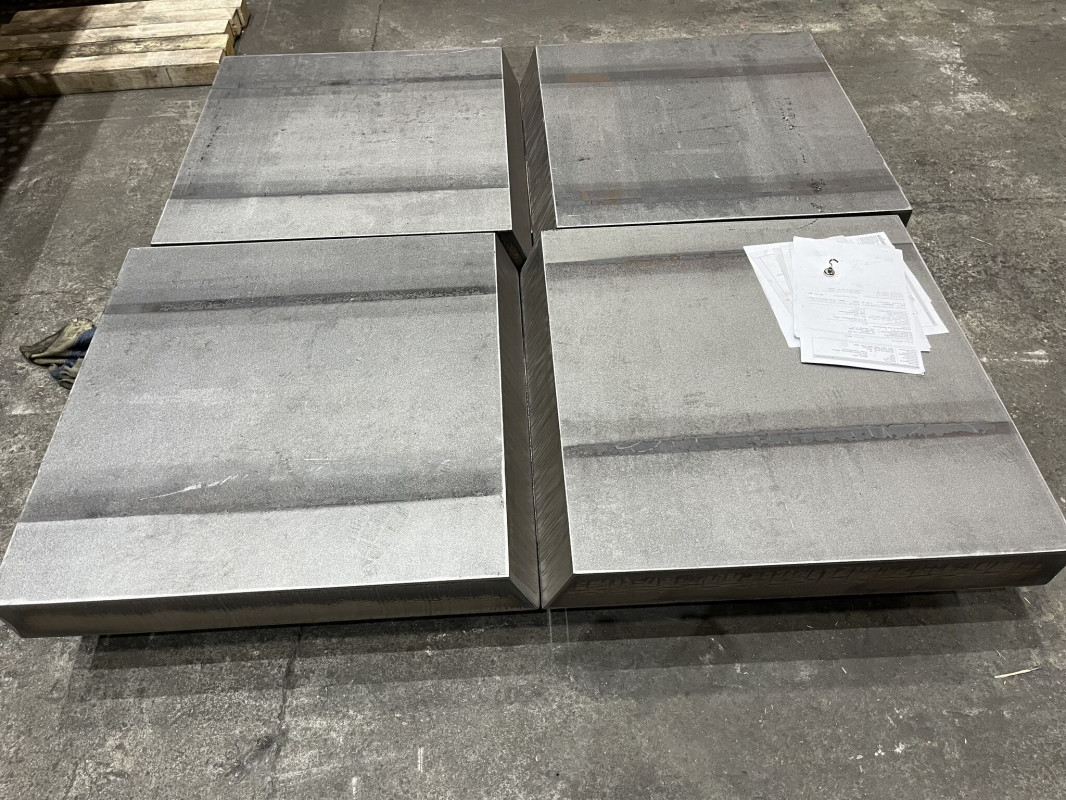
Der Entspannungsprozess
Zu Beginn des Prozesses gilt es, neben Material und Gewicht des Bauteils die richtige Lagerung des Werkstücks zu beachten. Sodann werden die erforderliche Mindestbeschleunigung im Bauteil von zehn Metern pro Quadratsekunde und die Maximaldrehzahl von bis zu 6.000 Umdrehungen pro Minute ermittelt und in Höhe der Eigenresonanzen eingestellt. Der Modalhammer erzeugt durch kurzes, kräftiges Anschlagen an das Bauteil mehrfach einen Kraftimpuls. Beim Vibrationsentspannen messen und überwachen zwei Schwingungsaufnehmer die im Bauteil durch den eingebrachten Impuls ausgelöste Beschleunigung. Ein triaxialer Beschleunigungsaufnehmer misst die Beschleunigung des Werkstücks in der X-, Y- und Z-Achse. Ein monoaxialer Aufnehmer misst an der Stelle des Blechs, die vom Motor am weitesten entfernt ist, wie viel Beschleunigung noch ankommt. Der Entspannungsprozess erfolgt in fünf Zyklen à bis zu zehn Frequenzen, in denen der Modalhammer jeweils die Eigenfrequenzen des Bauteils ermittelt. Sobald sich die Frequenz des Bauteils ändert, passt die automatische Steuerung mittels Modalanalyse Unwucht und Drehzahl entsprechend an. Anhand des Frequenzbandes wird der jeweilige Entspannungszustand des Bauteils ermittelt. Nach Abschluss der fünf Zyklen erfolgt eine Endmessung. Alle Frequenzen werden in einem Protokoll festgehalten und der Entspannungszustand in einem Diagramm abgebildet. Bei großen Bauteilen, wie sie bei Jebens an der Tagesordnung sind, muss der Motor mehrfach versetzt werden, um die Entspannung des gesamten Bauteils zu gewährleisten. Alle Bearbeitungsfrequenzen werden automatisch ermittelt, abgearbeitet und im Vibrationsprotokoll alphanumerisch und grafisch dokumentiert.
Durch die Modalanalyse ist nach Aussage von VSR-Industrietechnik ein wissenschaftlich haltbarer Nachweis erbracht, dass die Eigenspannungen im Bauteil so weit reduziert wurden, dass man Verzug im Bauteil ausschließen kann. Eine Rissbildung in Bauteilen ist durch die geringe Schwingungsamplitude ebenfalls ausgeschlossen. Rund 150 Anlagen zum Vibrationsentspannen hat das Unternehmen mit Hauptsitz in Duisburg bis heute verkauft. Namhafte Industrieunternehmen wie ThyssenKrupp, Audi, Ford, Caterpillar, Liebherr oder Sennebogen setzen dieses Verfahren seit Jahrzehnten in ihrer eigenen Fertigung ein oder schreiben ihren Zulieferern dessen Anwendung vor. Auch bei Jebens vertrauen bereits viele anspruchsvolle Industriekunden auf das Vibrationsentspannen für Komponenten für Abkantpressen mit bis 100 Tonnen Teilegewicht, für Schmiedemanipulatoren mit bis 40 Tonnen Teilegewicht oder auch für Pressen mit bis 80 Tonnen Teilegewicht.
Die Vorteile
Für dieses Verfahren sprechen zahlreiche Vorteile: Während eine durchschnittliche Spannungsarmglühung rund 6,6 Tonnen CO2 emittiert, betragen die CO2-Emissionen beim Vibrationsentspannen nur noch 0,03 Tonnen. Dem Energieverbrauch von 32.400 kWh für Spannungsarmglühen stehen nur 8 kWh beim Vibrationsentspannen gegenüber. Auch der erforderliche Zeitaufwand ist deutlich geringer: Für eine Ofenfahrt werden in der Regel 72 Stunden benötigt, Vibrationsentspannen dauert bei großen Bauteilen nur etwa acht Stunden. Zudem entsteht beim Vibrationsentspannen keine Zunderschicht am Bauteil, die anschließend per Sandstrahlen entfernt werden muss. Das erspart nicht nur kostenaufwendige Nachbearbeitung, sondern ist auch materialschonender. Nachträgliches Richten entfällt in der Regel ebenfalls, da beim Vibrationsentspannen kein Verzug entsteht. Da jede Bauteilgröße zwischen 100 Kilogramm und 200 Tonnen sowie sogar extreme Bauteilgeometrien vor Ort behandelt werden können, entfällt auch der Transport zu einem geeigneten Glühofen. Trotz des höheren Personalaufwands während der Behandlung ist Vibrationsentspannen durch die enormen Einsparungen bei Energie, Nacharbeit, Transport und Zeitaufwand die erheblich kostengünstigere Lösung, um Eigenspannungen zu reduzieren. Aus Sicht von Jebens sprach überdies für das Verfahren, dass die hier gefertigten Bauteilabmessungen oft so groß sind, dass eine komplette Glühung nicht möglich oder ein passender Ofen nur mit sehr hohem Aufwand erreichbar ist. Nicht zuletzt ist für vergütete Bauteile keine Glühung machbar, da bei der hierfür zulässigen Glühtemperatur kein nennenswerter Spannungsabbau erfolgen würde.
Der Vergleichsversuch
Dennoch gibt es auch bei Jebens Kunden, die das Verfahren noch nicht zulassen. Anders als für das Spannungsarmglühen gibt es hierfür in der FKM-Richtlinie zur Berechnung der Festigkeit von Maschinenbauteilen keinen etablierten Faktor als Bemessungsrichtline zum Nachweis der Ermüdungsfestigkeit. Deshalb führte Jebens jetzt einen vielbeachteten Vergleichsversuch zur Verformung beim Fräsen von spannungsarmgeglühten und vibrationsentspannten Bauteilen durch. Ziel dieses Versuchs war es, Rückschlüsse über den Spannungszustand im Bauteil herzuleiten. Zu diesem Zweck schnitt Jebens zwei Bleche mit 110 Millimetern Dicke auf 800 x 800 Millimeter zu. Sodann brachte das Unternehmen an einer Seite eine Schweißnahtvorvereitung für eine V 110 Naht an und heftete die Bauteile von Hand. Anschließend wurden sie mit einem Schweißroboter verschweißt.
Beide Schweißungen erfolgten mit der gleichen Parametrierung. Die Parameter wurden zudem so gewählt, dass möglichst hohe Eigenspannungen im Schweißnahtbereich entstanden. Ein Plattensatz wurde anschließend spannungsarmgeglüht, der andere vibrationsentspannt. Sodann sollte durch Fräsen im Schweißnahtbereich eine Veränderung der Eigenspannungen in den Bauteilen erzeugt werden und zur Verformung der Werkstücke führen. Da Eigenspannung im Gegensatz zu Verformung bei einem Bauteil nicht messbar ist, wurden auf der Rückseite der Plattensätze je drei Messnuten eingefräst. In diesen Nuten sollten nach jedem Fräsdurchgang per Laser die jeweiligen Ebenheitsabweichungen gemessen werden. Eine erste Messung erfolgte als Nullmessung in diesem Zustand. Auf der Schweißnahtoberseite wurde eine breite Fräsbahn herausgefräst, um Schweißgut und WEZ komplett abzufräsen. Pro Fräsgang wurden drei Millimeter zugestellt. Insgesamt erfolgten drei Fräsdurchgänge mit einer Spandicke von drei Millimetern. Bei den ersten beiden Durchgängen wurde mit Kühlschmiermittel gefräst, beim dritten Fräsdurchgang ohne. Die einzelnen Fräsdurchgänge wurden ebenfalls immer mit den gleichen Parametern umgesetzt. Nach jedem Durchgang wurde die Ebenheit der Messnuten gemessen und in ein Diagramm eingetragen, in dem jede Bahn separat dargestellt ist. Die vereinheitlichte Skalierung der Diagramme erlaubte den direkten Vergleich der Ergebnisse: Bei dem vibrationsentspannten Bauteil war die Durchbiegung nur ein Drittel so groß wie bei dem spannungsarmgeglühten Bauteil. Daraus lässt sich aus Sicht von Jebens die Annahme ableiten, dass in dem vibrationsentspannten Bauteil die Eigenspannungen geringer sind als in dem spannungsarmgeglühten.
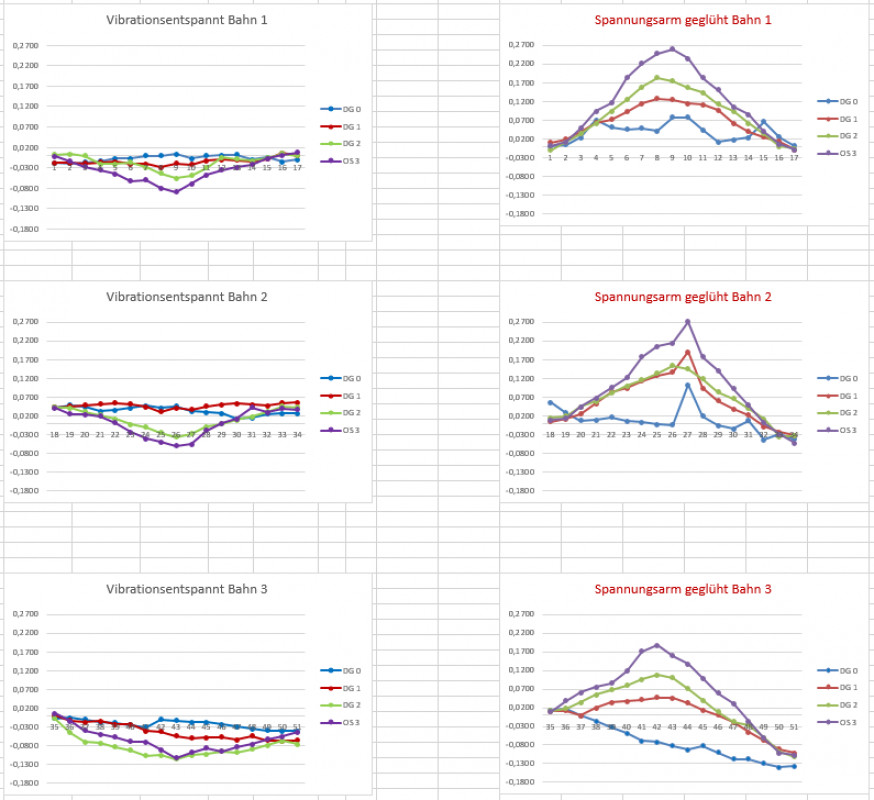
Dieses Ergebnis in der Praxis bestätigt eine theoretische Studie, die VSR bereits vor einigen Jahren mit der RWTH Aachen University durchgeführt hat. Die Aachener Forscher belegten per FEM-Berechnung, dass Vibrationsentspannen die Effizienz von Spannungsarmglühen übertrifft. Eine Aussage, die auch Anwender wie Audi, Ford oder ThyssenKrupp in eigenen Praxisuntersuchungen bestätigt sahen und das Verfahren fortan einsetzten. Vibrationsentspannen ist deshalb aus Sicht von Jebens und VSR-Industrietechnik ein ebenso sicheres Verfahren wie herkömmliches Spannungsarmglühen, verweist dieses jedoch mit der Summe der Vorteile in den meisten Fällen auf die Plätze.
(Quelle: Jebens GmbH)
Schlagworte
BauteileEigenspannungenMetalleSchweißtechnikSpannungsarmglühenVibrationsentspannen