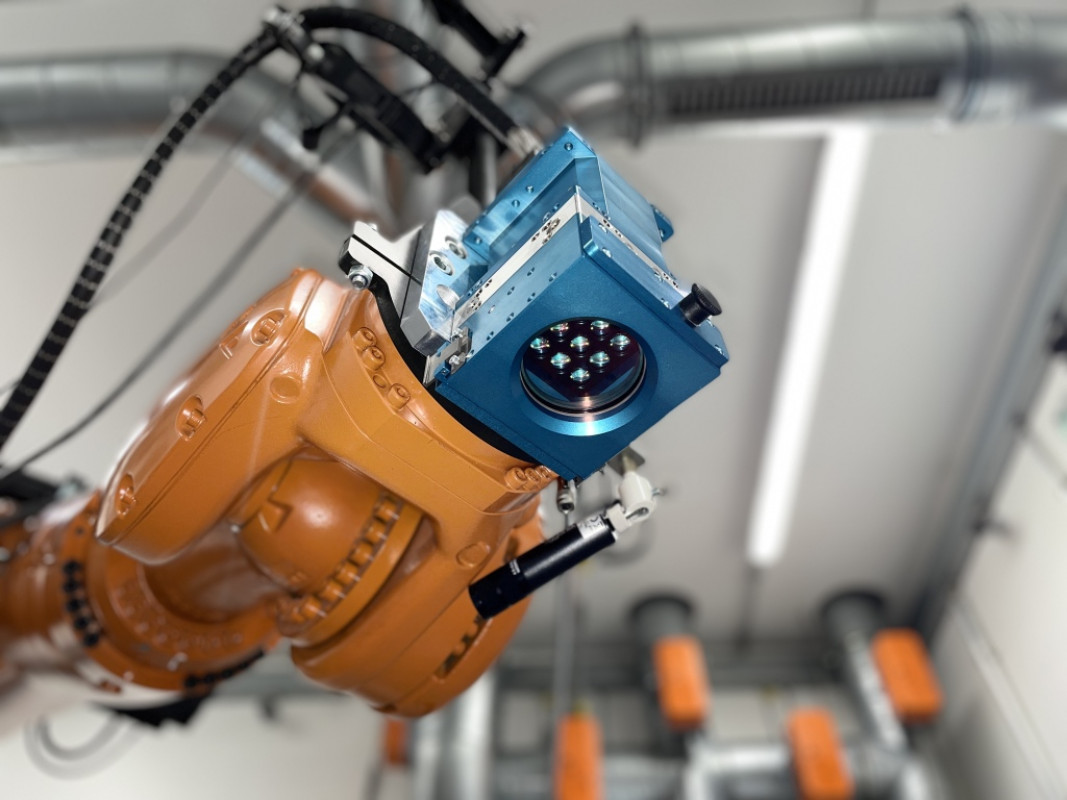
Zwei neue Optikkonzepte verbessern die Schweißnaht bei der Hairpin-Fertigung und dem Fügen von Kunststoffen auf Metall
Das Strahlwerkzeug Laser ist aus modernen Fertigungen nicht mehr wegzudenken. Dabei wachsen die Anforderungen bezüglich Effizienz und Einsatzmöglichkeiten – und damit auch die Grenzen der Laser. Bei neuen Anwendungsfeldern, Bauteilgeometrien und Werkstoffen kann es passieren, dass konventionelle Optiken mit eingeschränkten Bewegungsradien und limitierten Strahlformungsoptionen nicht mehr ausreichen, um ein fehlerfreies Schweißergebnis zu garantieren. Hierzu zählen z.B. das Zusammenfügen von thermoplastischen Kunststoffen und Metall als Strukturkomponenten in der Fahrzeugkonstruktion und das Verschweißen von Hairpins in E-Motoren. Daher haben die Laserspezialisten von LMB gemeinsam mit Partnern zwei neue Konzepte entwickelt, mit denen sich das Schmelzbad durch eine flexiblere Ansteuerung und präzisere Leistungsverteilung positiv beeinflussen lässt. Mit dem Twin-Weld-Verfahren wird eine bessere Vermischung im Schmelzbad erreicht, sodass Spalte schneller überbrückt werden können. MULTISPOT erlaubt es, die Intensitätsverteilung innerhalb eines Laserfokus lokal und zeitlich zu variieren. So kann die Leistung erstmals präzise an die Schweißnahtgeometrie und die Materialeigenschaften angepasst werden.
„Der Laser ist ein etabliertes Werkzeug in der Fertigung“, weiß Dipl.-Ing. Peter Schlüter, Geschäftsführer der LMB Automation GmbH. „Trotz seiner vielseitigen Möglichkeiten und Ausprägungen birgt die Verwendung allerdings ein paar Stolpersteine, die durch Anpassungen und stetige Weiterentwicklung aus dem Weg geräumt werden können.“ So ist Laserstrahl nicht gleich Laserstrahl: Die Form beeinflusst die Produktqualität, indem sie Leistungsdichte, Schnittbreite, Schmelzbaddynamik und Wärmeeinflusszone bestimmt. Je nach Anwendung kann der Strahl fokussiert, aufgeweitet oder geteilt werden. Besonderes Augenmerkt sollte dabei auf dem Schmelzbad liegen, das sich auf die Geometrie, Festigkeit und Mikrostruktur der Verbindung und somit die Qualität der Schweißnaht auswirkt. Je besser sich diese Dynamik mit einer optimierten Optik ort- und zeitunabhängig steuern lässt, desto eher können typische Probleme wie Risse, Poren, Spritzer, Hinterschnitte oder eine unzureichende Durchdringung im Keyhole vermieden werden.

Aufbau einer Optik mit rotierenden Komponenten
Ein typischer Fall, bei dem die Kombination aus anspruchsvollem Werkstoff und unzureichender Flexibilität der Optik zu Problemen führen kann, ist das Schweißen von Kupferverbindungen, die z.B. in der Statorfertigung bei den Hairpins gelegt werden. Die viskose Kupferschmelze führt zu einer ausgeprägten Prozessdynamik, wodurch das Material sehr schnell zu spritzen anfängt. Für die Fertigung ist aber ein möglichst spritzarmer Prozess notwendig, da kein ausgeworfenes Material in den Stator gelangen darf. Um dies zu gewährleisten, nutzt LMB im Twin-Weld-Verfahren eine angepasste Bifokal-Optik, die den Strahl in der Vorwärtsbewegung im Vergleich zu herkömmlichen, feststehenden Scanneroptiken zusätzlich teilt und in kleinen Kreisen um die optische Achse rotieren lässt. „Die beiden Teilstrahlen sorgen im Schmelzbereich durch zwei Keyholes dafür, dass das aufgeschmolzene Material besser vermengt und durch die Drehbewegung in den Spalt hineingedrückt wird“, erklärt Schlüter. Dadurch gewinnt die Schweißnaht an Festigkeit. Gleichzeitig sorgt die Teilung und Rotation dafür, dass die Zeitspanne beim Überfahren eines Referenzpunktes gegenüber nur einem Fokuspunkt halbiert und der gesamte Schweißvorgang damit beschleunigt wird.
Mit der Kombination aus hoher Rotationsgeschwindigkeit und flexibler Optik ermöglicht es das Twin-Weld-Verfahren erstmals, alle Konturen mit dieser Optik zu bearbeiten. Mit einer feststehenden Bifokaloptik wäre dies gar nicht erst möglich. Darüber hinaus reduziert die höhere Rotationsgeschwindigkeit deutlich die Anzahl der Poren, die im oberen Bereich der Schweißnaht auftreten. „Da insbesondere CU-Bauteile sehr stark zur Spritzerbildung neigen, wollten wir dem unbedingt vorbeugen. Dies gelingt uns durch zügiges Anschmelzen und Hineindrücken des erwärmten Materials, sodass es gar nicht erst nach oben aus dem Keyhole entweichen kann“, so Schlüter.
Laseroptik zum Fügen von Kunststoffen mit einer breiten Naht
Thermoplastische Kunststoffe stellen eine neue Herausforderung für das Laserschweißen dar. Sie kommen bei der Realisierung von Leichtbaukonzepten zunehmend als Strukturbauteile zum Einsatz. Das Laserschweißen von Kunststoffen ist zwar nicht neu, wird jedoch vor allem zum Erzeugen relativ schmaler Schweißnähte etwa im Bereich von Mikrofluidanwendungen eingesetzt. Für Strukturbauteile sind hingegen große Anbindungsflächen zwischen den einzelnen Bauteilkomponenten erforderlich, um eine hinreichende Kraftübertragung zu gewährleisten. Damit beim Fügeschweißen von unterschiedlichen Kunststoffen sowie von Kunststoffen mit Metallen höhere Festigkeiten und Dichtigkeiten erreicht werden können, sind breitere Schweißnähte notwendig, als sie sich mit Standardoptiken erstellen lassen. „Prinzipiell können mit homogenisierten Laserfokussen durchaus breite Schweißnähte erzeugt werden“, wirft Schlüter ein. „Untersuchungen haben allerdings gezeigt, dass die maximalen Prozesstemperaturen beim Fügen mit einem großen Laserfokus bei kleinen Radien zu einer partiellen Überhitzung des Materials im Innenbereich führen.“ Wesentlicher Grund hierfür ist die stark eingeschränkte oder gar nicht vorhandene Möglichkeit, die Intensitätsverteilung innerhalb des erforderlichen großen Laserstrahlspots während des Fügeprozesses örtlich und zeitlich variieren zu können.
Hier setzt der neue MULTISPOT Schweißkopf an, den LMB gemeinsam mit sechs Partnern im Rahmen eines „KMU-innovativ“-Projekts entwickelt hat. Die Optik nutzt eine Matrix aus 3x3 Laserdioden, die einzeln ansteuerbar sind, wodurch die Intensitätsverteilung im Laserfokus sehr flexibel bestimmt werden kann. Hierfür wird jede der Einzeloptiken von einer eigenen Laserdiode versorgt. Dies hat den Vorteil, dass z.B. in einer Kontur beim Abfahren von Kurven der äußere Bereich im Fokus mit einer höheren und der innere mit einer reduzierten Strahlleistung beaufschlagt werden kann. Damit lässt sich der Schweißvorgang wesentlich präziser an die Schweißgeometrie sowie an die Materialeigenschaften anpassen.
Zusammenspiel von Kunststoff und Metall im Leichtbau
Als besonders vielversprechend hat sich diese Optik beim Verschweißen von Kunststoff mit Metall gezeigt, das beispielsweise beim Fahrzeugbau für Türen oder im Innenraum immer häufiger zur Anwendung kommt. „In den Versuchen war das tragende Element ein Blechrahmen, an den zum Schutz und vor allem zur Gewichtsreduzierung eine Verkleidung aus Kunststoff angebracht werden sollte“, berichtet Schlüter. Dabei muss die Schweißung eine hohe Festigkeit erreichen und dicht sein, damit keine Feuchtigkeit an den Rahmen gelangt. Zur Vorbereitung des Prozesses wurden die Fügeflächen des Metallteils zunächst mit einem anderen Lasersystem aufgeraut. Anschließend wurden beide Bauteile zusammengepresst und das Metall mit dem neuen MULTISPOT-Schweißkopf erhitzt. Durch eine eingebrachte Leistung von 100 W pro Diode konnten in Summe 900 W eingesetzt werden, um den angepressten Kunststoff an der Kontaktfläche zum heißen Metall aufzuschmelzen. Dank der anpassbaren Intensitätsverteilung floss die Schmelze gleichmäßig ohne Wärmeverluste in die strukturierten Bereiche, sodass eine besonders homogene und stabile Naht entstanden ist.

Beide Optiken kommen derzeit für tiefergehende Anwendungsversuche in Prototypaufbauten zum Einsatz, um zu herauszufinden, wie sich die Intensitätsverteilung und das Schmelzergebnis bei unterschiedlichen Geometrien und Werkstoffen verhalten. Hieraus sollen wichtige Erkenntnisse gewonnen werden, wie der Aufbau und die Betriebskosten durch mögliche Anpassungen zukünftig noch effizienter gestaltet werden können. Für LMB zeigten beide Projekte, dass sich ein stetiges Hinterfragen und Weiterentwickeln etablierter Konzepte auszahlt: „Alles begann mit einer einfachen Frage: Wie lässt sich der Wirkungsgrad des Lasers bei der Einbringung in das Werkstück verbessern? Am Ende stehen jetzt zwei praktikable und zukunftsweisende Optikkonzepte, die das Werkzeug Laser ein Stück weit vielseitiger letztendlich den Leichtbau zukunftsfähiger machen können“, resümiert Schlüter.
Weitere Informationen ffinden Sie hier:
(Quelle: Presseinformation der LMB Automation GmbH)
Schlagworte
BauteilgeometrieFügen von KunststoffenHairpin-SchweißenKunststoff-Metall-VerbundKupferverbindungenLaserstrahlschweißenLasertechnologienLeichtbauPrototypenbauSchweißnähteWerkstoffe