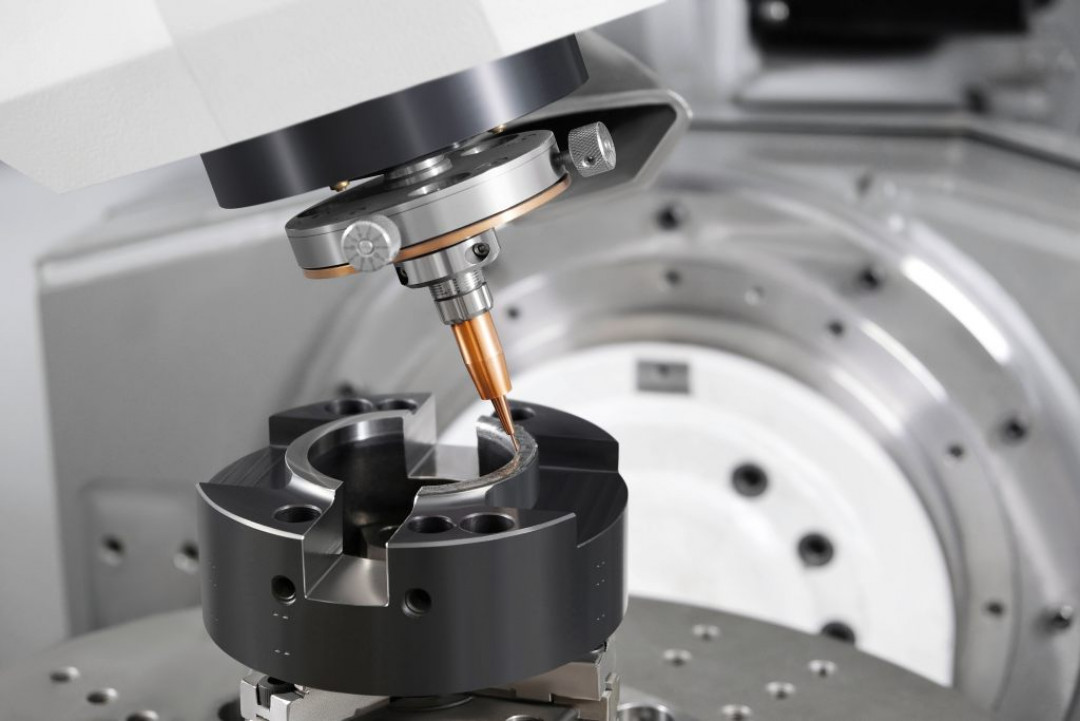
Reparieren, nicht neu produzieren! Mit automatisiertem LMD
Im Sinne von ökonomischer, wie ökologischer Nachhaltigkeit ist dieser Aufruf absolut zutreffend und zukunftsgerichtet. Wenn es darum geht, Formen und Komponenten zu reparieren, statt neu zu produzieren, ist das Laserauftragschweißen (Laser Metal Deposition/LMD) eine bewährte Schlüsseltechnologie – mit einem wachsenden Potenzial an neuen Anwendungsgebieten. Im Fokus des Workshops „reFORM“ beim OPEN HOUSE 2022 der CHIRON Group stand die Automatisierung von LMD-Reparatur-Prozessen. Und eines hat sich gezeigt: So ganz einfach ist das nicht. Aber wer es umzusetzen weiß, gewinnt Zeit, spart Kosten und – handelt ausgesprochen nachhaltig.
Eigentlich ist es wie beim Zerspanen, nur funktioniert LMD genau andersrum. Statt Material wegzunehmen, wird es aufgetragen. Mittels Pulver oder Draht, oder beides in Kombination. Was bei einem der Vorschub und Schnitttiefe ist, ist beim anderen Auftragsrate und Schichtdicke. Wo der eine sein Werkstück kühlt, heizt der andere es auf. So oder so muss am Ende des Tages das Bauteil in geforderter Qualität und Wirtschaftlichkeit produziert werden – mit den immer gewichtigeren Zusatzkriterien energetisch nachhaltig und Ressourcen schonend.
Prozesstechnologie LMD – automatisiert reparieren
Mit dem Ziel vor Augen über Voraussetzungen und Möglichkeiten automatisierter LMD-Prozesse zu sprechen, war geballte Expertise beim Workshop „reFORM“ der CHIRON Group in Tuttlingen vertreten. Ein sehr anschauliches Bild zur Motivation, sich dieser Herausforderung zu stellen, gab Cedric Bardenhagen, Key Account Manager bei der Siemens AG, in seinem Vortrag über die Programmierung additiver Fertigungsprozesse: Ein neu produziertes Zahnrad mit Ø 500 mm und 230 kg Gewicht bedarf knapp 2.000 kW/h in seiner gesamten Produktionskette. Für die Stahlproduktion und das Schmieden der Form sind das 90 Prozent der Energie, für Zerspanung und Nachbehandlung die restlichen zehn Prozent. Ein aus recyceltem Stahl produziertes Zahnrad verbraucht im Vergleich „nur“ noch 39 Prozent der Herstellenergie. Wenn man so ein Rad jetzt mit einem automatisierten LMD-Prozess repariert, benötigt man lediglich noch 17 Prozent der Energiemenge eines neuen Rades, respektive 42 Prozent zu einem recycelten, um mit dieser wieder in Form gebrachten Komponente beispielsweise ein Windrad zum Laufen zu bringen. Kurz gesagt: Reparieren mit additiver Fertigung ist hochpositiv für die Klimabilanz!

Materialien und Schweißen – das ist Wissenschaft
Doch zunächst zurück ganz an den Anfang des Prozesses, den Ursprung. Und da steht immer das Material. Für Formen und Werkzeuge werden in der Regel hitzebeständige Chromstähle verwendet. Die Beanspruchungen, denen ein Umformwerkzeug unterliegt, können sehr unterschiedlich sein. Ob das ein Schmiedewerkzeug für die Herstellung einer Generatorwelle mit 250 Tonnen Eigengewicht ist oder eine Kegelwalze für die Produktion von nahtlosen Ringen – die auftretenden Belastungen unterscheiden sich zum Teil grundlegend. Dies hat Dr. Michael Nolde, in der Geschäftsleitung der Capilla Schweißmaterialien GmbH, am Beispiel einer vollautomatisierten Schmiedeanlage vom Schmiederohling bis zum Fertigteil eindrücklich aufgezeigt.
Um Form und Werkzeug verschleißbeständiger zu machen, werden mittels verschiedener Schweißverfahren beanspruchungsgerechte Schutzschichten aus Eisen-, Kobalt oder Nickellegierungen aufgebracht. Was man bei der Herstellung von Neuwerkzeugen, aber auch bei deren Reparatur im verschlissenen Zustand, z. B. Ausbrüche und abgenutze Stanzflächen, materialseitig und verfahrenstechnisch zu beachten hat, ist in der Tat eine Wissenschaft für sich. Allerdings kann nur so eine gute Form- und Werkzeugqualität erzielt werden – lange Standzeiten sind die Folge. Bestenfalls übertreffen diese sogar die von ungeschweißten Neugesenken. Diese Erkenntnis stellen ein unabdingbar wertvolles Wissen für die erfolgreiche Umsetzung von automatisierten LMD-Prozessen dar. Die gut 40 Jahre Erfahrung haben die rund 30 Workshopteilnehmenden regelrecht gespürt.
Multifunktionale Anlage für automatisierten LMD-Prozess – 3D-Metalldrucker AM Cube bewährt sich in der Praxis
Dieses hochspezialisierte Wissen um Materialeigenschaften bei Schweißprozessen haben das Team Additive Manufacturing der CHIRON Group, die Gastgeber des Workshops, für die Entwicklung des AM Cube genutzt. Bei der heute sehr großen Materialvielfalt ist die Flexibilität der Anlage ein wichtiges Kriterium für einen automatisierten LMD-Prozess: So viele Formen und Konturen, so viele Materialien sind in der täglichen Praxis im Einsatz, da macht es Sinn, dass die Anlage einfach und schnell wechselbare Auftragsköpfe hat – bis zu drei sind möglich. Einmal ist Pulver das bevorzugte Schweißmaterial, einmal Draht – der Anwender hat alle Optionen.
Dominik Hipp, Leiter Werkzeugbau bei der Hammerwerk Fridingen GmbH, ist so ein Anwender, verantwortlich für die Produktion von Gesenken und Werkzeug, um eine Tagestonnage von rund 200 Tonnen gewährleisten zu können. Zusammen mit der CHIRON Group arbeitet er an mehreren Projekten, unter anderem an der Reparatur von Schnittringen. „Das automatisierte Schweißen auf dem AM Cube erfüllt unsere Qualitätsanforderungen und steigert die Standzeit um den Faktor 2,5 bis 3.“ berichtet Hipp in seiner Präsentation. „Ausschlaggebend, die LMD-Reparatur zu automatisieren, war auch die Tatsache, dass man für das manuelle Schweißen kaum noch qualifizierte Fachkräfte findet. Jetzt wo der automatisierte Prozess steht, ist es wichtig, die Mitarbeiter in den automatisierten LMD-Prozess einzuführen und dafür zu begeistern, um in Zukunft noch mehr Formen zu reparieren und damit unsere Produkte wie auch unsere Klimabilanz zu verbessern,“ so Dominik Hipp.

Daten sind das A&O – Basiswissen, Steuerung und digitale Systeme kombiniert
„Prozesskontrolle und Dateneffektivität sind bei automatisierten LMD-Lösungen ein Muss“, davon ist Till Oeschger, Projekt Manager AM Cube bei der CHIRON Group, überzeugt. Warum er so denkt, so denken muss, zeigt sich besonders deutlich in der sehr beeindruckenden Präsentation von Prof. Dr. Hadi Mozaffari-Jovein, Werkstoffwissenschaftler an der Hochschule Furtwangen Universität. Was die Teilnehmenden des Workshops im Vortrag erkannt haben, war die Komplexität des Themas: Von den physikalischen, chemischen und mechanischen Anforderungen an Werkzeug und Werkstoff bis zum Auftragsschweißen für graduierte Legierungen. Da kommen eine Menge Faktoren zusammen. Und damit letztlich auch Parameter und Daten, die in der Konstruktion des Bauteils verwendet werden müssen, um automatisierte LMD-Prozesse sicher und reproduzierbar zu machen.
Wertvoll sind diese Daten auf mehreren Ebenen. Mit Siemens NX CAM lassen sich mit den Anlagen- und Werkstückdaten die Bearbeitungsabläufe komfortabel programmieren und mit Hilfe des digitalen Zwilling vorab simulieren. Ein fehlerfreies und bereits optimiertes Programm kann 1:1 auf die Anlage übernommen werden. „Der Aufwand für die CAD-/CAM-Programmierung liegt für einen Schnittring bei gut 90 Minuten und das ist schnell“, betont Quentin Leibinger, Application Engineer AM bei der CHIRON Group.

Auch während der Bearbeitung auf der realen Maschine spielen Daten eine wichtige Rolle. Alle relevanten Prozessdaten werden über zwei neue digitale Systeme der CHIRON Group erfasst: Via DataLine AM lassen sich alle relevanten Prozessdaten kontinuierlich live darstellen, aufzeichnen und in einem kompakten Qualitätsreport dokumentieren. Produkt- und Prozessqualität können so sicher beurteilt werden. VisioLine AM visualisiert und speichert Videodateien, die über mehrere Kamerasysteme erfasst werden. Einmal eingegebene Parameter und Toleranzen dienen als Referenz und im Fall von Abweichungen kann man sofort gezielt eingreifen. Ein großes Plus für den Werker:in. Die kontinuierliche Sammlung und Analyse der Daten hilft enorm, den idealen Prozess zu definieren, sind sich Leibinger und Oeschger einig.
Am Ende ist es eine Turnkey-Lösung – Knopf drücken und starten
Wenn man ein Fazit zum Workshop ziehen möchte, dann dieses hier: Der Aufruf „Reparieren, nicht neu produzieren!“ mit automatisiertem Laserauftragschweißen ist sicherlich kein einfach umzusetzender Prozess. Doch nicht anders als wie beim spanenden Prozess auch, entstehen aus Technologiepartnerschaften, dem Expertenwissen mit dem Finger am Puls der Praxis und schließlich den Erfahrungen aus gemeinsamen Projekten neue innovative Lösungen. Die Ergebnisse und Erkenntnisse aus dem Workshop geben berechtigten Anlass dazu. Im Sinne der Nachhaltigkeit sehr gute Aussichten.
(Quelle: Presseinformation der CHIRON Group SE)
Schlagworte
Additive FertigungInstandsetzungLaser Metal DepositionLaserauftragschweißenLMDReparaturSchweißtechnik