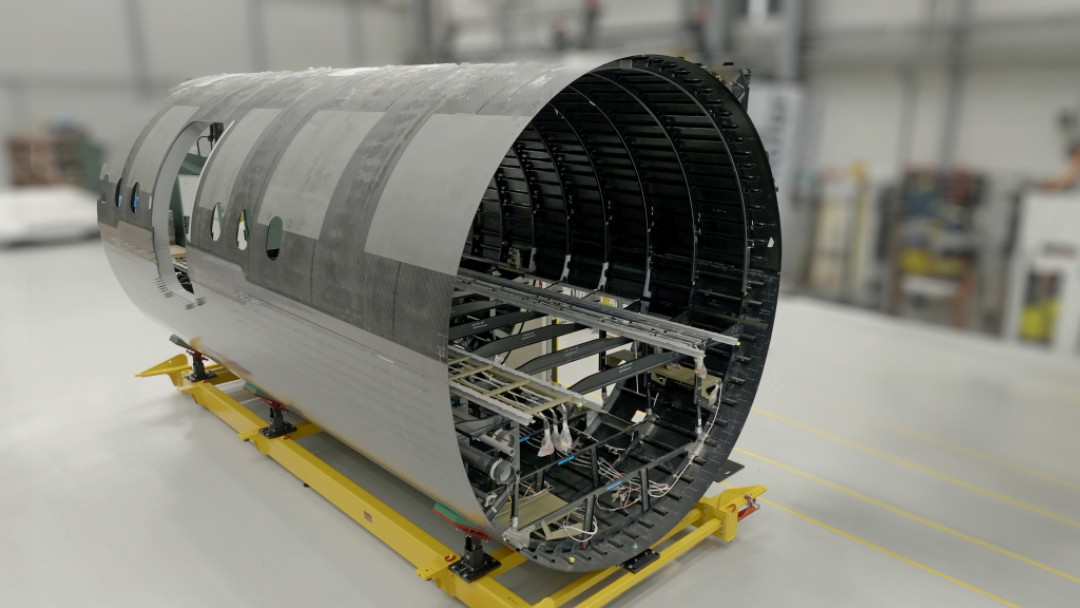
Lasertechnologie für ein leichteres Fliegen der Zukunft
Einen entscheidenden Fortschritt auf dem Weg in Richtung neuer ökologischer Flugzeugbaukonzepte hat das Fraunhofer-Institut für Werkstoff- und Strahltechnik IWS erzielt. Ein Forscherteam aus Dresden erbrachte innerhalb des EU-Programms Clean Sky 2 im Projekt „Multifunctional Fuselage Demonstrator“ (MFFD) den Nachweis zum spanlosen Fügen von kohlenstofffaserverstärkten Bauteilstrukturen aus Thermoplast. Der entwickelte automatisierte Verfahrensansatz verband die obere und untere Hälfte des weltweit größten CFRTP-Flugzeugrumpfsegments. Die neuartige Bauweise sowie das eingesetzte CONTIjoin-Verfahren ermöglichen neben dem Einsparen von Arbeitsaufwand, wie etwa beim Bohren und Nieten, massive Gewichts-, Material- und Zeitreduktion. Das soll die Produktion zukünftiger Verkehrsflugzeuge schneller, umweltfreundlicher und wettbewerbsfähiger gestalten. Die Forschenden präsentieren ihre Ergebnisse und die Systemtechnik auf der Internationalen Luft- und Raumfahrtausstellung ILA 2024 in Berlin.
Produktionstechnologien für den thermoplastischen Rumpf von morgen erforscht ein internationales Konsortium unter der Leitung von AIRBUS. Im Rahmenprogramm „Large Passenger Aircraft“ (LPA) gelang es innerhalb des MFFD-Projekts dem Team um Dr. Maurice Langer, Gruppenleiter Kleben und Faserverbundtechnik am Fraunhofer IWS, erstmals weltweit unter Einsatz einer CO2-Laserstrahlquelle das Schweißen langer Verbindungsnähte an großvolumigen thermoplastischen Flugzeugfaserverbundstrukturen außerhalb eines Autoklaven zu demonstrieren.
Auf der linken Seite des MFFD erzeugte der am Fraunhofer IWS entwickelte Verfahrensansatz die finale Längsnahtverbindung zwischen der oberen und unteren Rumpfhälfte eines acht mal vier Meter messenden Abschnitts des Flugzeugrumpfsegments aus „Carbon Fiber Reinforced Thermo-Plastics“ (CFRTP) – in Originalgröße. Das so genannte CONTIjoin-Verfahren, eine Kombination aus CO2- Lasertechnologie und hochdynamischer Strahlablenkung, regelte in Echtzeit die Laserleistung, um die Temperatur in der Fügezone konstant zu halten und ermöglichte zugleich die automatisierte Anpassung der Strahlfigur im Schweißspalt.
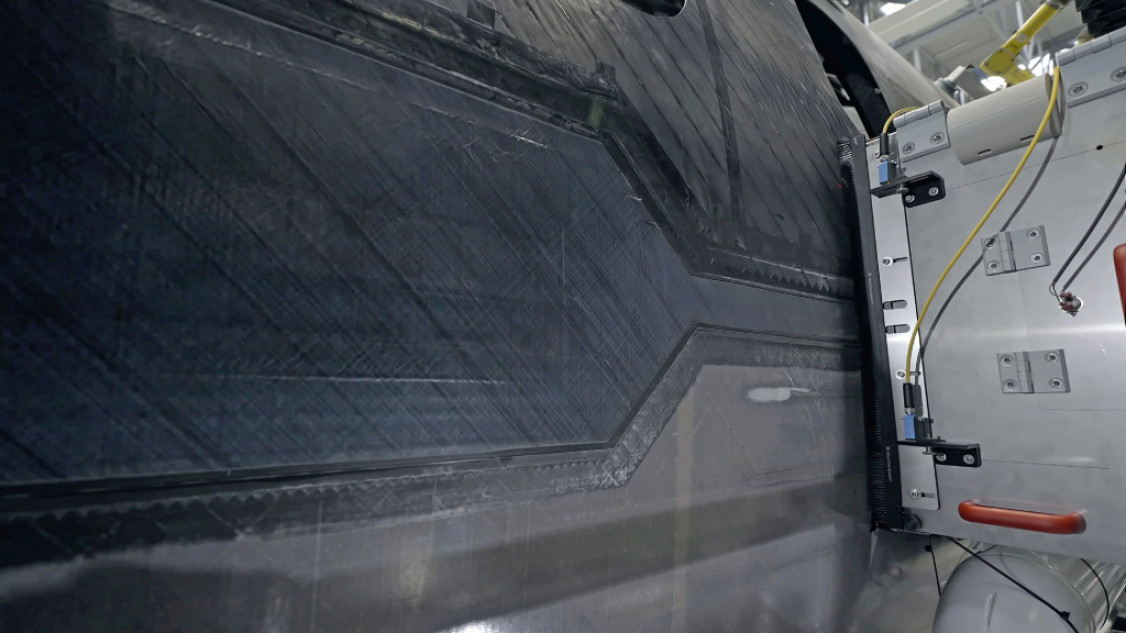
Gewicht erheblich eingespart
Das neuartige Verfahren macht den Einsatz mechanischer Verbindungselemente überflüssig und verzichtet zudem auf Materialdopplungen wie bei klassischen genieteten Überlappverbindungen. Die Rumpftonne aus geschweißtem, thermoplastischem Verbundwerkstoff wiegt somit deutlich weniger als heute übliche Sektionen. Dies markiert einen wichtigen Schritt im Flugzeugbau unter Einsatz neuartiger Hochleistungsmaterialien, da es das Fügen von hochfesten und schweißbaren Faserverbund-Großbauteilen ermöglicht.
Die Herausforderung bestand darin, Materialien wie PAEK zu verarbeiten, das eine für Kunststoffe vergleichsweise sehr hohe Wärmeform- und Temperaturbeständigkeit aufweist. „Herkömmliche Fertigungsverfahren für diese Materialien sind oft energieintensiv und aufwendig“, erläutert Dr. Langer. „Wir haben deshalb gemeinsam mit dem Projektpartner AIRBUS einen Verfahrensansatz entwickelt, in dem wir mittels einer gestuften Schäftungstechnologie Bauteile außerhalb des Autoklaven miteinander fügen können und zugleich hervorragende Festigkeitseigenschaften dieses Verbundes erreichen.“ Herkömmliche Verfahren seien in dieser Hinsicht limitiert, insbesondere wenn es um hohe Produktionsraten und großvolumige Bauteilstrukturen der Luftfahrt gehe. Dr. Langer betont: „Neue Materialklassen erfordern innovative Fertigungsmethoden. Erklärtes Ziel war es, am Multifunctional Fuselage Demonstrator das Rumpfgewicht um bis zu eine Tonne zu reduzieren.“ Über die Betriebsdauer des Flugzeugs hinweg betrachtet ließen sich aufgrund des geringeren Gewichts und einer verbesserten Integration der Systemarchitektur der Gesamtenergiebedarf, der Treibstoffverbrauch sowie der Ausstoß von Luftschadstoffen wie Kohlenstoffdioxid und Stickstoffoxiden signifikant senken. „Mit dem am Fraunhofer IWS entwickelten CONTIjoin-Verfahren ist uns somit ein wichtiger ökonomischer und ökologischer Schritt für die zukünftige Flugzeugentwicklung sowie angrenzende Anwendungen gelungen“, unterstreicht Dr. Maurice Langer.
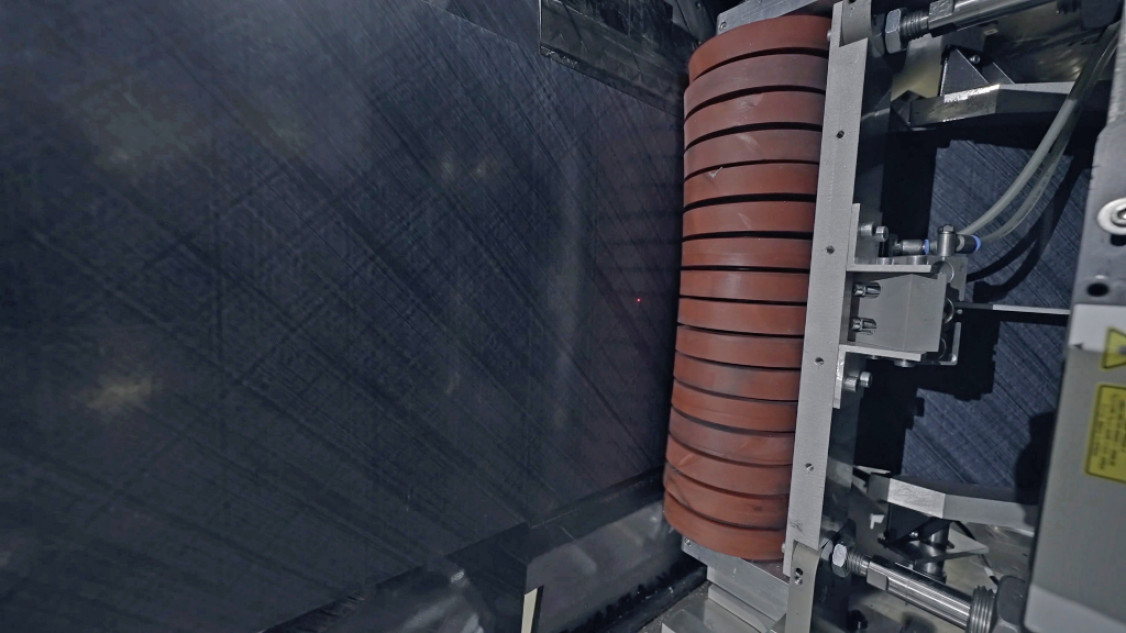
Flugzeughalbschalen per Laser geschweißt
Der Schlüssel zum Erfolg lag für das Team darin, die Ober- und Unterschale des Flugzeugkorpus durch kontinuierliche Ablage mehrerer übereinander angeordneter Laminatstreifen, so genannter „Straps“, schrittweise miteinander zu verbinden. Die mit jedem Arbeitsschritt zunehmend von 60 bis 360 Millimeter breiter werdenden Streifen wurden hierzu automatisiert in eine auf den Oberflächen der Halbschalen eingebrachte Stufengeometrie (Schäftung) abgelegt. Die so erzeugten Überlappverbindungen stellen den zunächst unterbrochenen Kraftfluss des Faserverbundmaterials zwischen den Halbschalen wieder her und bilden einen verlässlich lastenübertragenden Verbund. „Eine weitere Besonderheit für diesen Prozess stellt die Wellenlänge des eingesetzten CO2-Lasersystems dar“, fügt Dr. Langer hinzu. Das CONTIjoin-Verfahren biete den einzigartigen Vorteil, dass die Wellenlänge von 10,6 Mikrometern in dem relevanten Kunststoffanteil des Faserverbundmaterials eine deutlich höhere Einkopplung (Absorption) der Laserstrahlung aufweist, als die herkömmlich eingesetzten Faserlaser mit 1,06 Mikrometern. „Dadurch lässt sich der erforderliche Energieeintrag im Bereich der zu fügenden Grenzflächen zwischen den einzelnen Bauteilen auf ein Minimum reduzieren, wodurch die heute typischerweise nachfolgenden Prozessschritte vollständig entfallen.“
Technologien des Fraunhofer IWS machen den Unterschied
Ein weiterer essentieller Technologiebaustein stellt das ebenfalls am Dresdner Institut entwickelte „ESL2-100-Modul“ dar. „Damit können wir verschiedenste Sensorsignale verarbeiten und daraus abgeleitet entsprechende Steuerungsalgorithmen implementieren“, erläutert Peter Rauscher, Gruppenleiter High-Speed Laserbearbeitung am Fraunhofer IWS. „Das bietet sowohl die Möglichkeit der Überwachung als auch der adaptiven Steuerung des Schweißprozesses in Echtzeit. Mit herkömmlicher Ansteuerelektronik wäre dies nicht möglich. Damit gelingt es uns zum Beispiel neben der Regelung der Schweißtemperatur entlang des Schweißspalts auch die Position, Breite und Krümmung der Flugzeughalbschalen zu berücksichtigen.“
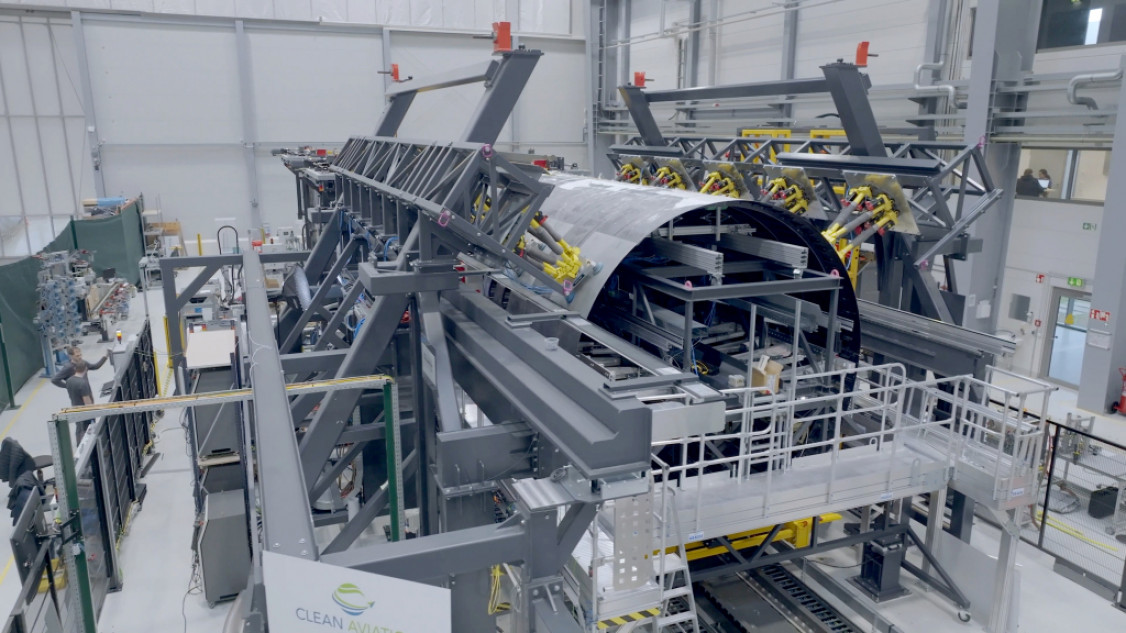
Das Setup bestand zudem aus zwei zusammenwirkenden Bewegungseinheiten, den so genannten Endeffektoren. Die Aufgaben des Straphandling-Endeffektors bestand darin, das aufzubringende Laminat während der kontinuierlichen Ablage präzise zu führen und es konturgetreu breitenabhängig an die Flugzeughalbschalen anzudrücken. Der zweite Endeffektor ermöglichte die Laserstrahlführung sowie pyrometrische Erfassung der Temperatur in der Fügezone. Jeder Endeffektor bewegte sich dafür synchron zum anderen auf einem eigenen linearen Achsensystem, um die Übertragung möglicher Vibrationen oder Verformungen durch das Andrücken der Laminatstreifen von der optischen Strahlführung des Lasersystems zu entkoppeln. Während die konzeptionelle Ausarbeitung und Umsetzung des gesamten Anlagen- sowie Steuerungssystems inklusive Mensch-Maschine-Schnittstelle auf einer vollständigen Eigenentwicklung beruhten, kamen bei den sonstigen eingesetzten Systemkomponenten wie beispielsweise Laserstrahlquelle, Pyrometer oder X-Y-Scannern, kommerziell erhältliche Industriekomponenten zum Einsatz.
Nächste Schritte: Technologiereife erhöhen und weitere Anwendungsgebiete erschließen
Auf diese Weise gelang es, sowohl die Technologieentwicklung als auch die Skalierung und Anwendung des Verfahrens anhand von Großstrukturen aus thermoplastischem Faserverbundmaterial wie dem MFFD zu demonstrieren. Der nächste Schritt besteht nun darin, das Technologie-Reife-Level (TRL) zu erhöhen und somit einen weiteren Schritt in Richtung Qualifizierung der Luftfahrttauglichkeit zu gehen. Dr. Langer erklärt: „Die entwickelte CONTIjoin-Technologie ist nicht nur für den Flugzeugbau interessant, sondern auch für andere Branchen. Die entwickelte Verfahrenslösung könnte so neben der Luftfahrt auch für Anwendungen im Schiffs-, LKW- und Aufliegerbau sowie im Schienenverkehr oder bei der Weiterentwicklung moderner Windenergieanlagen interessant sein.“ Eine Herausforderung bestehe darin, die Akzeptanz und den Einsatz sowohl der thermoplastischen Composite-Materialien als auch entsprechender Verfahren in den unterschiedlichen Branchen zu etablieren.
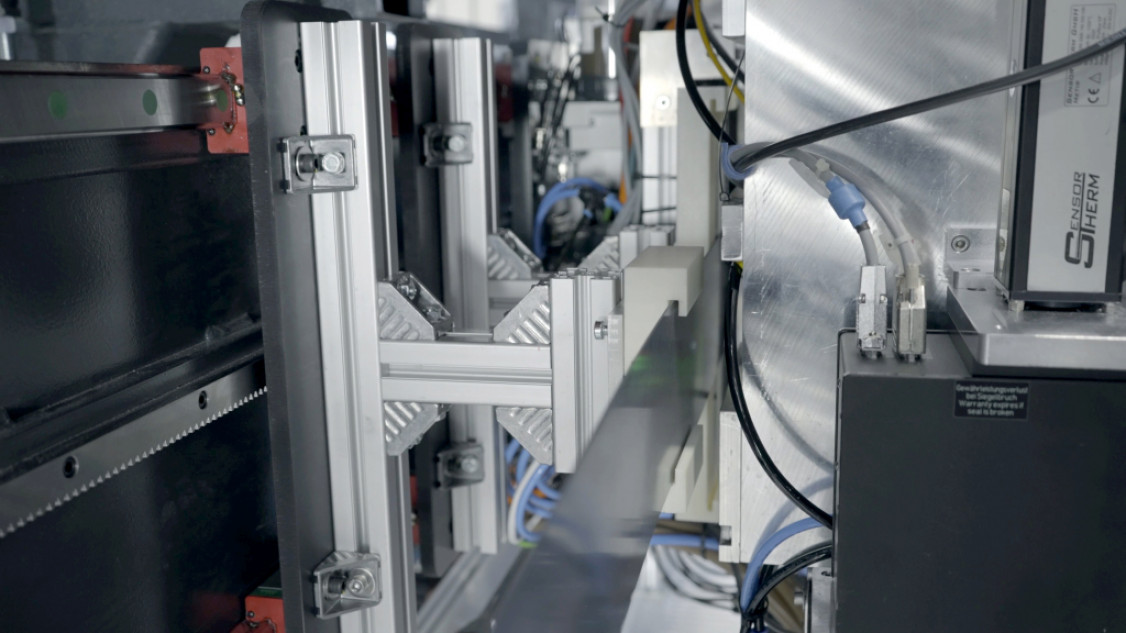
- Acroflight Ltd, Witham, UK
- Aernnova Aerospace S.A., Vitoria, Spanien
- Aeromechs srl, Aversa, Italien
- AIMEN – Asociación de Investigación Metalúrgica del Noroeste, O Porriño, Spanien
- Airbus
- Aitiip Centro Tecnológico, Zaragoza, Spanien
- ALPEX Technologies GmbH, Mils, Österreich
- BCC – Brunel Composites Centre, University London, UK
- CETMA – Centro di Ricerche Europeo di Technologie, Design e Materiali, Brindisi, Italien
- CT Engineering Group – Ct Ingenieros Aeronauticos de Automocion e Industriales Slu, Madrid, Spanien
- CTI Systems, Lentzweiler, Luxembourg
- Diehl Aviation Laupheim GmbH, Laupheim, Deutschland
- Diehl Comfort Modules GmbH, Hamburg, Deutschland
- DLR – Deutsches Zentrum für Luft und Raumfahrt, ZLP Augsburg, Deutschland
- DLR – Deutsches Zentrum für Luft und Raumfahrt, ZLP Stade, Deutschland
- Element Materials Technology, Sevilla, Spani
- FADA – Andalusian Foundation for Aerospace Development / CATEC – Center for Advanced Aerospace Technologies, Sevilla, Spanien
- FFT Produktionssysteme GmbH & Co. KG, Fulda, Deutschland
- Fraunhofer-Gesellschaft, Fraunhofer-Institut für Chemische Technologie ICT, Pfinztal, Deutschland
- Fraunhofer-Gesellschaft, Fraunhofer-Institut für Fertigungstechnik und angewandte Materialforschung IFAM, Stade, Deutschland
- Fraunhofer-Gesellschaft, Fraunhofer-Institut für Gießerei-, Composite- und Verarbeitungstechnik IGCV, Augsburg, Deutschland
- Fraunhofer-Gesellschaft, Fraunhofer-Institut für Werkstoff- und Strahltechnik IWS, Dresden, Deutschland
- GKN Aerospace, Fokker Aerostructures BV, Papendrecht, Niederlande
- GKN Aerospace, Fokker ELMO BV, Hoogerheide, Niederlande
- HSLU – Hochschule Luzern, Luzern, Schweiz
- KVE Composites Group, The Hague, Niederlande
- LSBU – London South Bank University, London, UK
- NLR – Royal Netherlands Aerospace Centre, Marknesse, Niederlande
- Ostseestaal GmbH & Co KG, Stralsund, Deutschland
- Premium AEROTEC, Augsburg, Deutschland
- Rescoll, Pessac Cedex, Frankreich
- SAAB AB, Stockholm, Schweden
- SAM XL, Delft, Niederlande
- Techni-Modul Engineering, Coudes, Frankreich
- Technische Universität München, Lehrstuhl für Carbon Composites, München, Deutschland
- Technische Universiteit Delft, Delft, Niederlande
- TWI – The Welding Institute, Cambridge, UK
- UPAT – University of Patras, Patras, Griechenland
- XELIS GmbH, Herford, Deutschland
Über das Clean-Sky-2- und Clean-Aviation-Projekt „MFFD“
Im Rahmen des von der EU geförderten Projekts „Large Passenger Aircraft“ („LPA“) hat die Fraunhofer-Gesellschaft in Stade mit internationalen Projektpartnern jeweils eine maßstabsgetreue Ober- und Unterschale des „Multi Functional Fuselage Demonstrator“ (MFFD) durch automatisierte Positionier- und Fügeprozesse miteinander verbunden. Das Verschweißen der linksseiteigen Längsnäht der beiden acht Meter langen CFK-Halbschalen, die einen Durchmesser von etwa vier Metern aufweisen, schloss die Herstellung des größten thermoplastischen CFK-Flugzeugrumpfsegments der Welt erfolgreich ab. Erstmals wurde in einem Forschungsprojekt ein Rumpfsegment in Originalgröße aus thermoplastischen CFK-Werkstoffen hergestellt, um Machbarkeit sowie ökologische und ökonomische Vor- und Nachteile darstellen bewerten zu können.
Als Fügeverfahren zum Schließen des Thermoplast-Flugzeugrumpfs wurde zusammen mit dem Projekt-Koordinator Airbus das CO2-Laserschweißen für die linke sowie das Ultraschallschweißen für die rechte Längsnaht ausgewählt. Im
Gegensatz zu aktuellen Nietverfahren bieten beide Verfahren den Vorteil des staubfreien Fügens. Allerdings wurden sie bisher weder in der Produktion noch in der Forschung bei derart großen CFK-Bauteilen und mit den benötigten speziellen Qualitätsanforderungen angewendet. Der Bedarf für ein staubfreies Fügen ergibt sich aus der erstmals durchgeführten Vorintegration beider Schalen mit einer Vielzahl von ebenfalls schweißtechnisch montierten Struktur- und Systemkomponenten, die ein nachträgliches Entfernen von Staub und Spänen nicht zulässt.
Mehr Informationen finden Sie hier:
(Quelle: Presseinformation des Fraunhofer-Instituts für Werkstoff- und Strahltechnik IWS)
Schlagworte
FaserverbundeFaserverbundtechnikFlugzeugstrukturenFügetechnikKlaebtechnikLasersystemtechnikLasertechnologienLeichtbauSchweißtechnikThermoplaste